Monthly Archives: March 2012
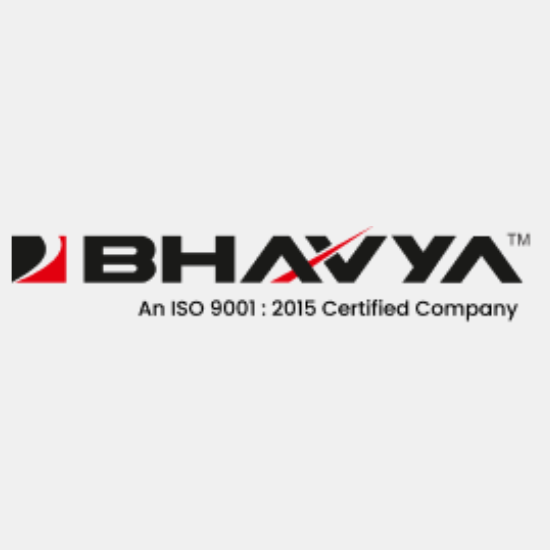
Shaping Machine, Slotting Machine, Milling Machine
Forms of Metal Forming Machinery - Shaping Machine, Slotting Machine, Milling Machine, Lathe Machine Different kinds of metal working machineries are used to form the metals into required shapes and sizes. These include the metal shaping machines, metal cutting machines,…
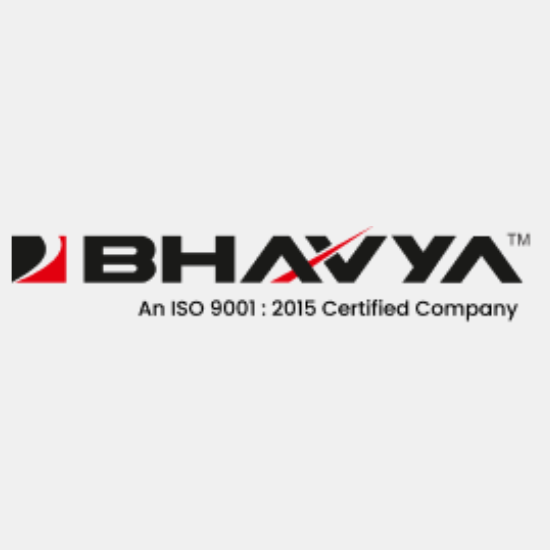
Sheet Bending – Press Brake, Power Press
Sheet Bending Process and Machines Sheet bending is a process of metal forming through which metals are bent into desired forms. In a sheet bending process the metals are casted into the required form by exerting a strong force on…