Monthly Archives: April 2013
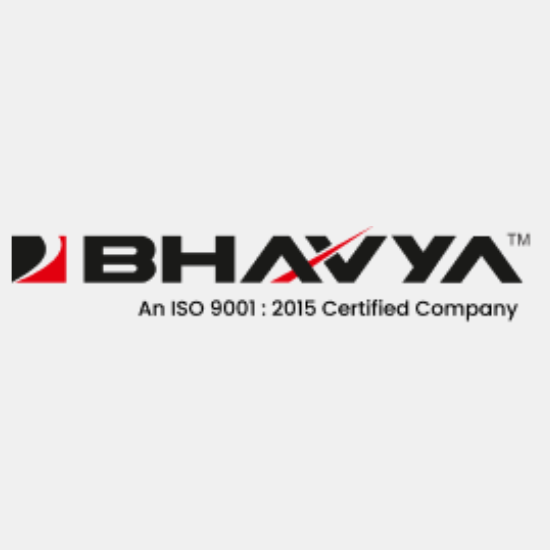
Rising Challenges & Opportunities for Power Press Manufacturers in India
The power press is a powerful sheet metal machine. It is mainly used for cutting, bending, pressing, forming and stamping sheet metal into different shapes and sizes. This highly precise and versatile machine deforms and cuts metal by pressing it…
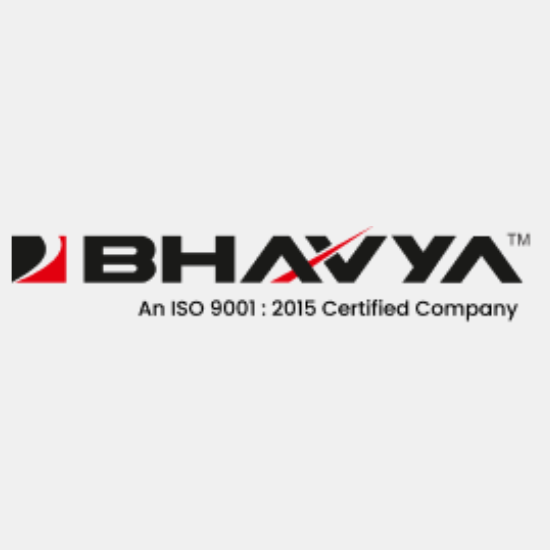
How to Select Best Radial Drill Machine for Different Industrial Drilling
A drilling machine is primarily utilized for drilling holes of various depths and sizes on different surfaces. Moreover this versatile machine is also used for performing some other operations such as counter boring, countersinking, lapping, reaming, screwing, spot facing, and…
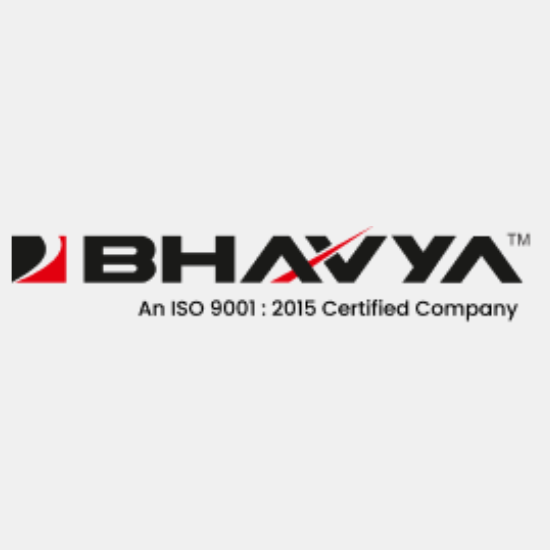
Rising Demand of Woodworking Machineries Across the World
Woodworking machines are highly popular and widely used equipments. They are basically utilized for performing various processes on wood, such as cutting, carving, drilling, finishing, grinding, joining, molding, sawing, sanding, shaping, etc. It help to avoid manual labor and the conventional…
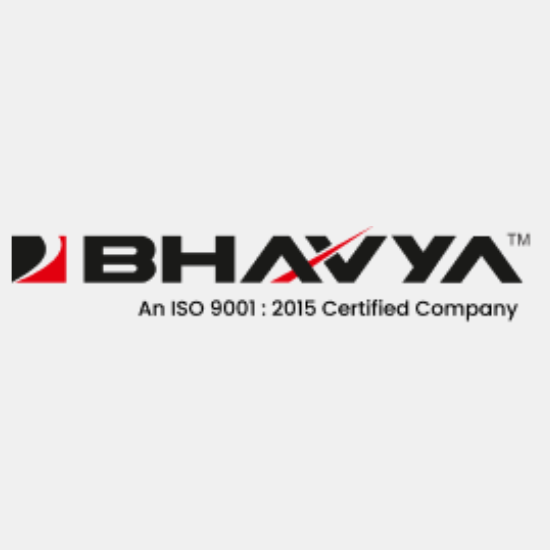
Know the Important Safe Guards while Operating Milling Machine
A milling machine includes a cutter that functions at a high speed. Hence, it can harm the user if not operated properly. Moreover, the milled material may cause serious injuries, because the metal chip is very sharp. Further the metal…
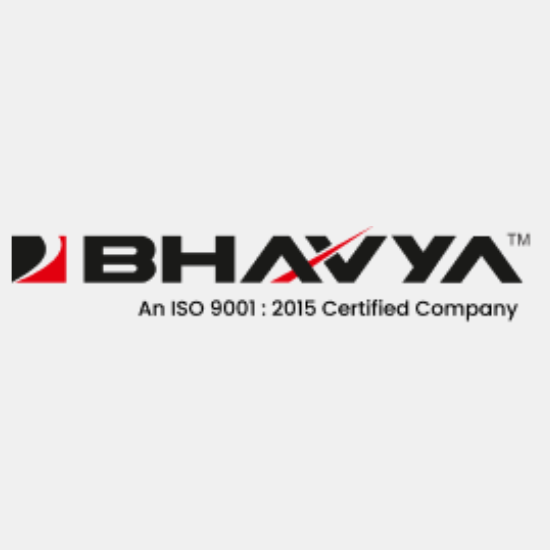
FAQs on Press Brake
A press brake is primarily used for accurately bending various types of metal sheets and plates. Some frequently asked questions are as follows: Q. What is camber? A. Camber is actually a small piece of cap which is placed on…
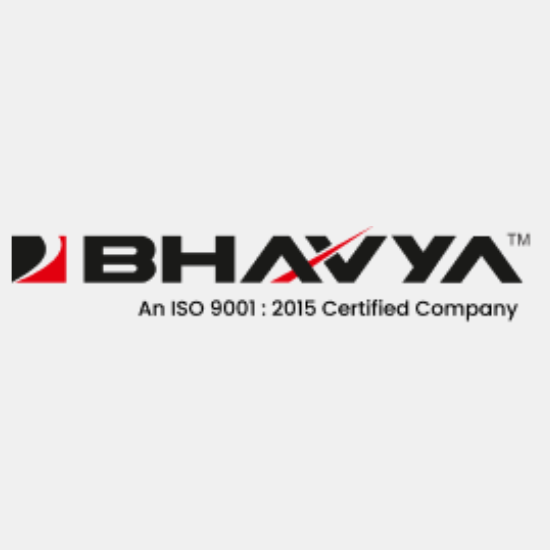
Sheet Metal Machineries for Shearing, Bending & Cutting
The various sheet metal machineries for shearing, bending and cutting are described below: Press Brake The mechanical press brake has a sturdy frame built from high grade steel. It also consists of steel plates with appropriate thickness and machined guide…