Monthly Archives: June 2023
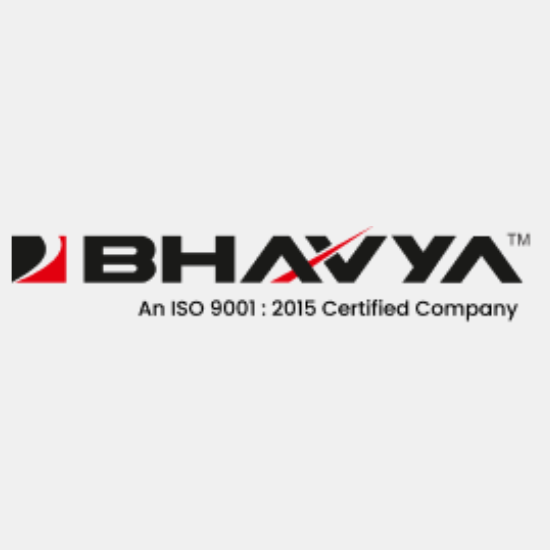
Radial Drill Machines Revolutionize Precision Engineering
Radial drill machines have played a pivotal role in revolutionizing precision engineering. These machines provide a versatile and efficient solution for drilling holes accurately and precisely in various materials. With their unique design and capabilities, radial drill machines have become…