Monthly Archives: February 2023
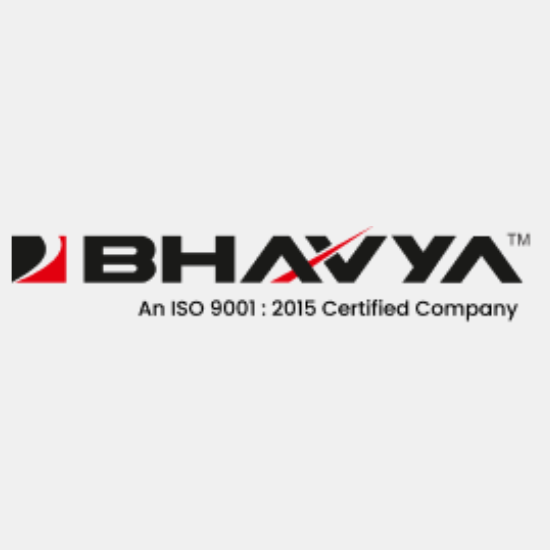
All About Chamfer Machine
A chamfer machine is a machine tool that is used to create a chamfer, which is a beveled edge on a workpiece. The chamfer machine can be used to create chamfers on a range of materials, including metal, plastic, and…
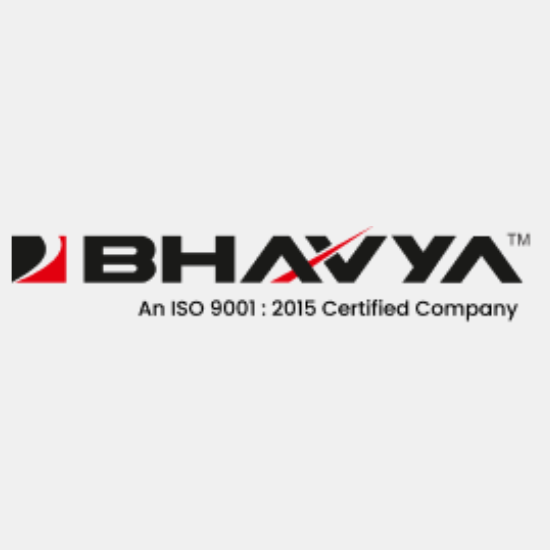
CNC Busbar Machine – Features, Applications and Benefits
A CNC Busbar Machine is a computer-controlled machine used for cutting, punching, bending, and forming copper or aluminum busbars. Busbars are used in electrical power distribution systems to carry large currents and distribute them to various components. The CNC Busbar…
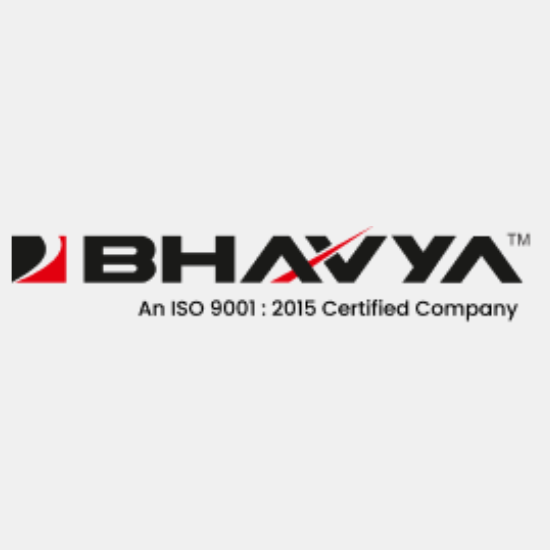
Universal Tool Grinder – Features, Applications and Benefits
A Universal Tool Grinder is a machine used for sharpening and grinding various cutting tools such as drills, end mills, reamers, and other metal cutting tools. The grinder is designed to perform a wide range of grinding operations to sharpen…
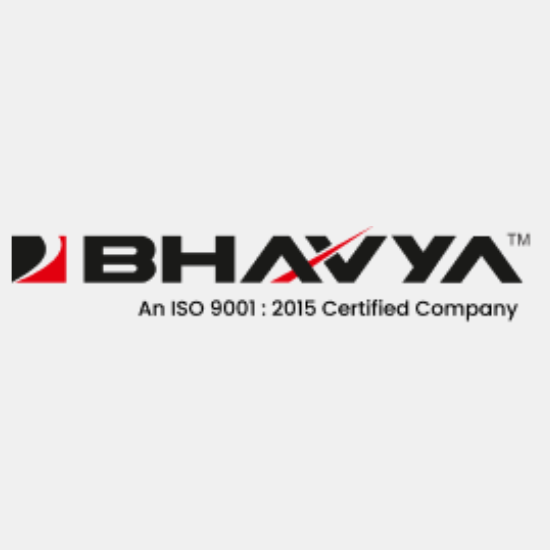
Bandsaw Blade Sharpener – Features, Applications and Benefits
A Bandsaw Blade Sharpener is a machine that is used to sharpen bandsaw blades used for cutting wood, metal, and other materials. Bandsaw blades tend to become dull over time due to the constant friction and wear and tear that…
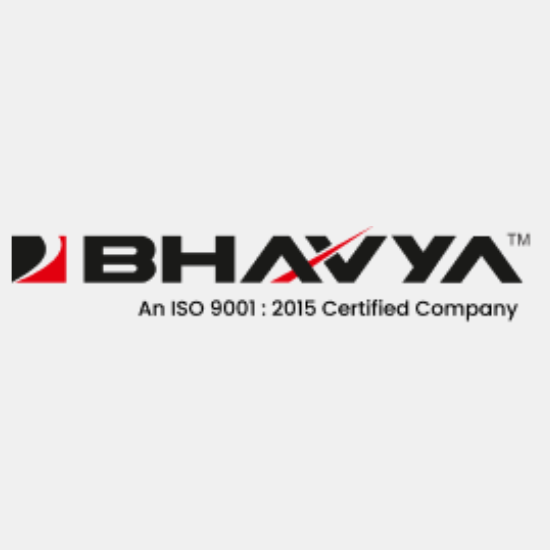
Tool & Cutter Grinding Machine Features, Applications and Benefits
What is Tool & Cutter Grinding Machine A Tool and Cutter Grinding Machine is a type of machine used to manufacture, sharpen, and repair various cutting tools such as milling cutters, drills, reamers, and other types of tools used in…