Monthly Archives: April 2021
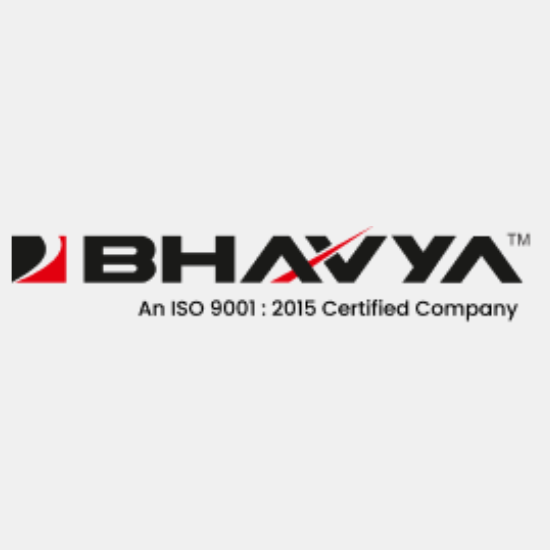
Emerging Global Trends and Demands of Hydraulic Ironworker
An Ironworker is a class of machines that are used to notch, shear, and punch holes in a steel plate or structure. They install and reinforcing iron and steel to form roads, buildings, bridges, etc. They use force either by…