Monthly Archives: March 2019
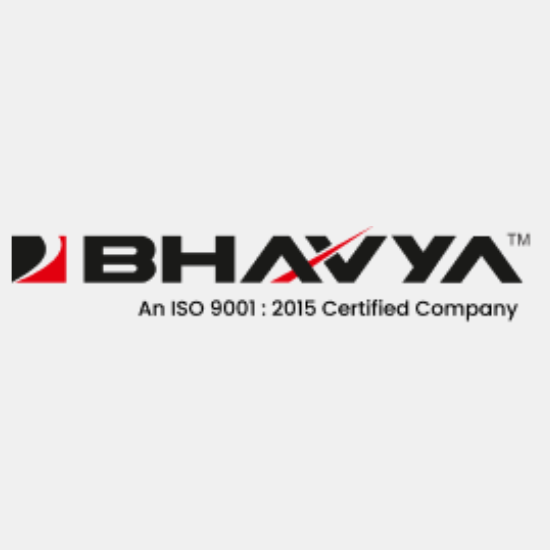
Latest Advancements in CNC Machining Center
Any CNC milling or drilling machine is referred to as a CNC machine center. There machines tend to include an automatic tool changer along with a table to clamp the workpiece. The way it works is that a tool rotates…
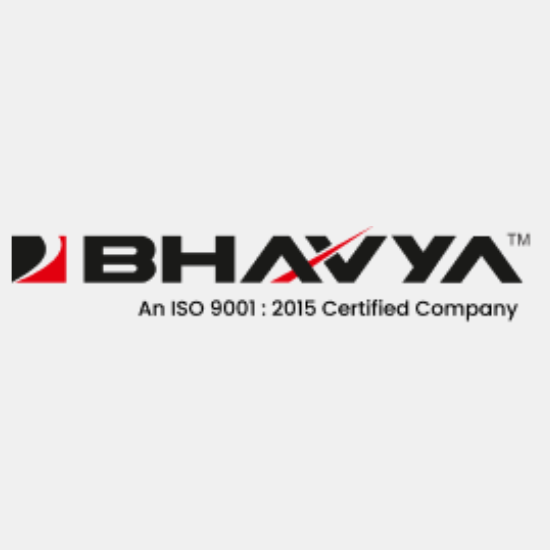
All About Hydraulic Surface Grinder
A surface grinder as the name suggests is meant for grinding operations. This is one of the most common machines for grinding operations. The main purpose is to ensure a smooth finish on a flat surface. There are a several…