Category Archives: Press Brake
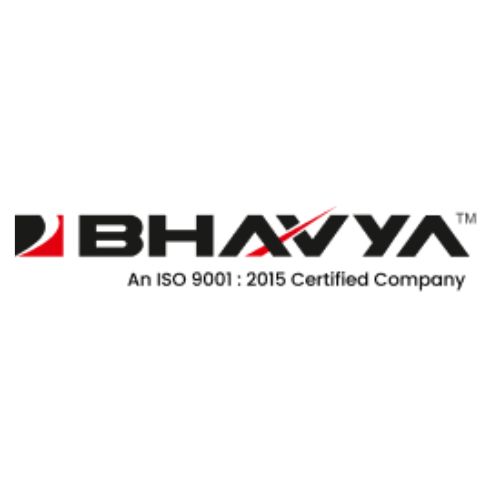
Regional Hotspots for Press Brake Machines Demand in South Africa
South Africa’s manufacturing and metal fabrication industry is undergoing a marked transformation, fueled by growing infrastructure investment, localization of production and the rise of precision engineering. At the heart of this shift lies a growing demand for high-performance Press Brake…
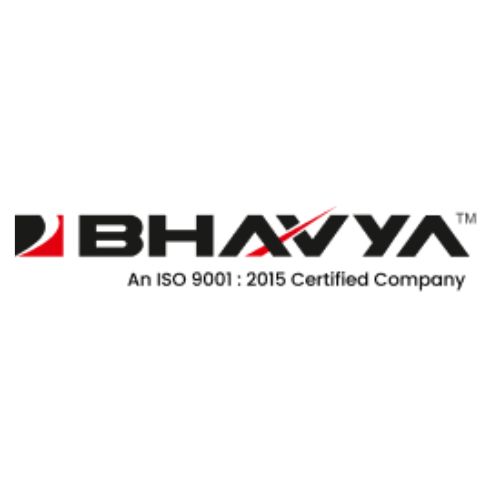
The Significance of Accessories in CNC Press Brake Machines
A CNC Press Brake Machine is a highly precise metal bending machine used in industries like automobile, aerospace, metal fabrication and construction. While the CNC Hydraulic Press Machine itself is a technological marvel, its efficiency and precision depend significantly on…
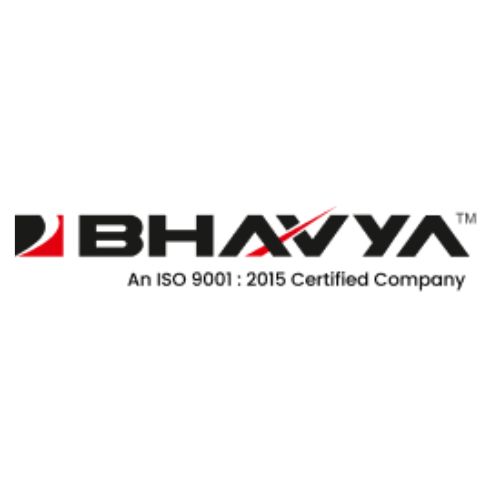
CNC Press Brakes and the Oil & Gas Industry: Applications in the Middle East
The oil and gas industry in the Middle East is a cornerstone of the global economy, producing a significant share of the world’s energy. The industry relies heavily on precision manufacturing and advanced machinery for its infrastructure, particularly in building…
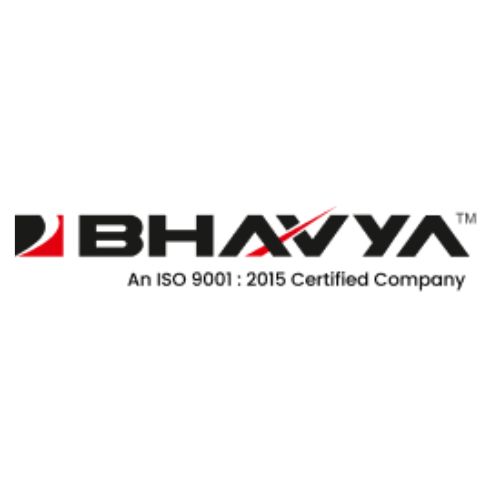
CNC Press Brake Machines: Precision, Efficiency, and Reliability for Industrial Bending
Introduction In today’s fast-paced manufacturing environment, precision and efficiency are critical for staying competitive. CNC press brake machines offer the perfect solution for precise bending and forming of various materials, particularly sheet metal. These machines provide user-friendly and cost-effective solutions…
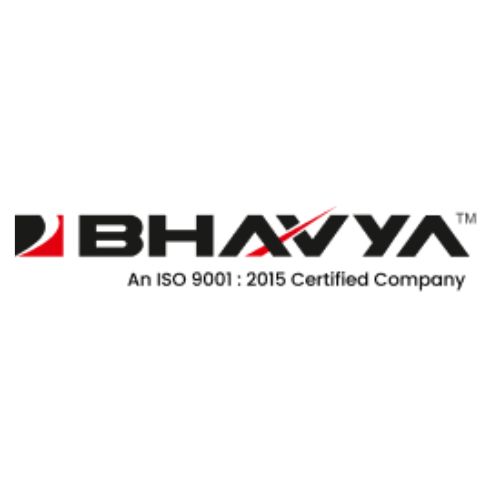
Press Brake Machine Market in United Arab Emirates
In this article, we will explore the Press Brake Machine Market in United Arab Emirates (UAE) and analyze the key market players, their key strategies, and future prospects. We will also explore the growth trends of the metal fabrication equipment…
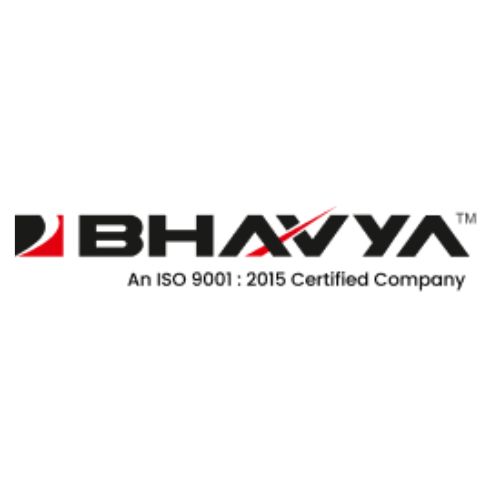
Press Brake Demand in UAE
What is driving the Press brake demand in the UAE? What are the opportunities and threats in this market? How will you segment this market? Here are some of the key points to consider. In addition, we will discuss the…
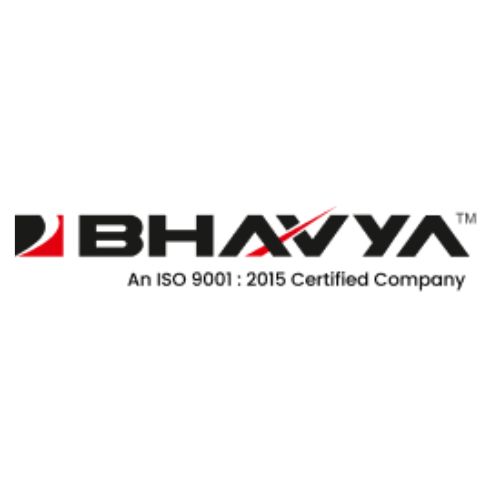
Tips for Choosing a CNC Press Brake
A CNC Press Brake machine is a great option for a company that produces large quantities of finished products. The main considerations for selecting a CNC Press Brake are the complexity of the designs to be created, how many axes…
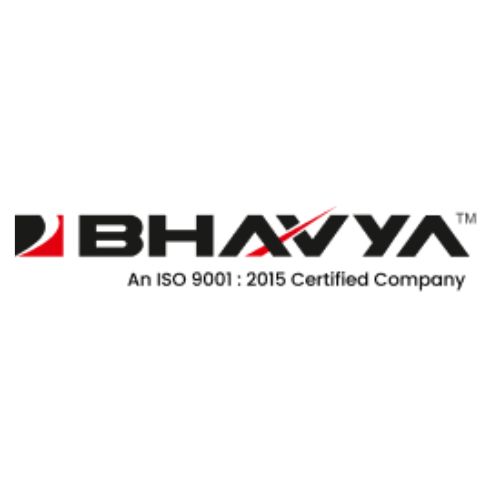
NC Press Brake Machines – Highly Versatile, and Efficient Press Brake Machines
An NC Press Brake machine is a tool that is used in the bending of thin plates. It consists of a bracket, a working table, and a clamping plate. The working table and clamping plate are connected by a hinge.…
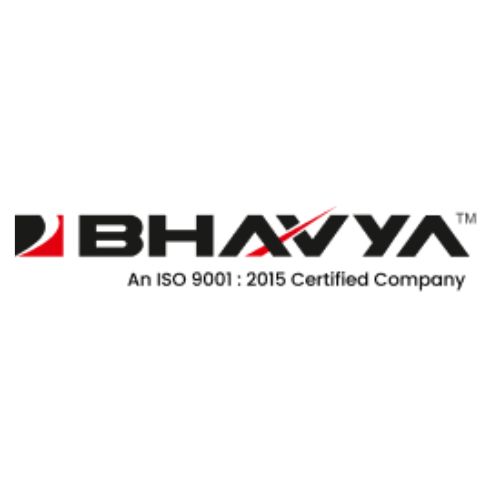
The Features, Functions & Benefits of a Press Brake Machine
If you are in the fabrication industry, you must have a Press Brake Machine. These heavy hydraulic presses are essential for bending sheet metal to a predetermined shape. Bhavya Machine Tools offers various press brakes to suit your fabrication needs.…
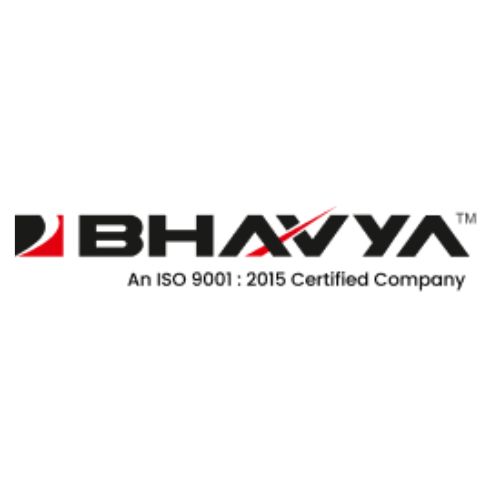
Features, Benefits, and Costs of CNC Press Brake Machines
If you're in the market for a CNC Press brake machine, you're probably wondering which features to look for and which benefits it offers. This article will walk you through the features to consider, workbench, and costs of CNC Press…
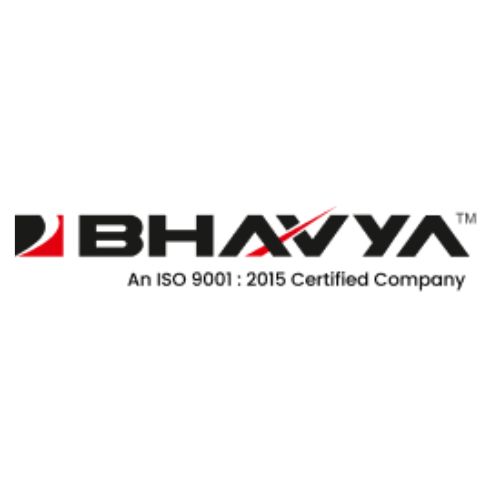
Press Brake Demand in Asia
Press brake demand in Asia is projected to grow at a CAGR of 8.2% over the next five years, largely due to increasing demand for fabricated metal products. One of the major restraints of the market is the slowing down…
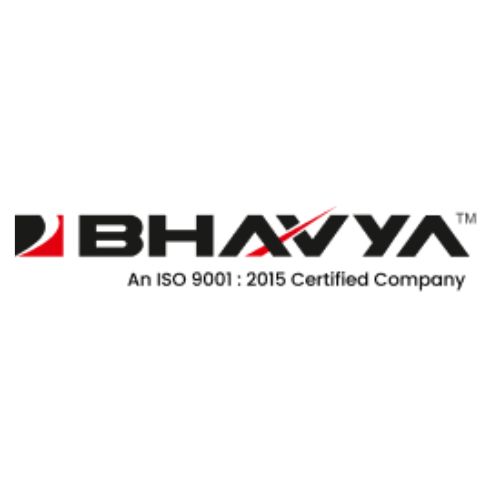
How to Select the Best CNC Press Brake System
A CNC press brake is the most popular type of brake available on the market. It is considered as the intelligent choice for many applications, because of its variety of uses, flexibility, safety, and economy. Most importantly, these brakes have…
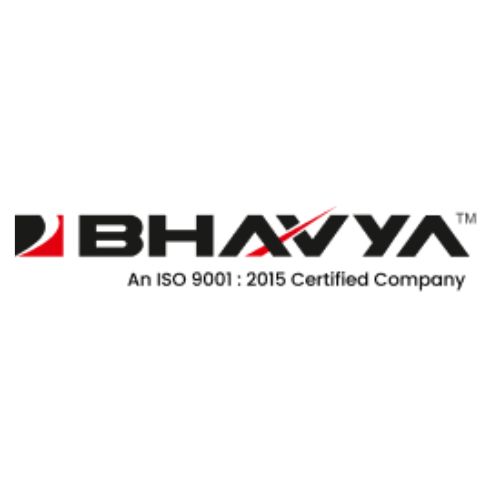
Different Press Equipments in Kitchen Ware Production
Metal Parts in Used For Kitchen Ware Design Cooking utensils made of metal have great demand all over the world because of its durability and wear and tear resistant nature. Creating different shapes of utilities still have excellent reception from…
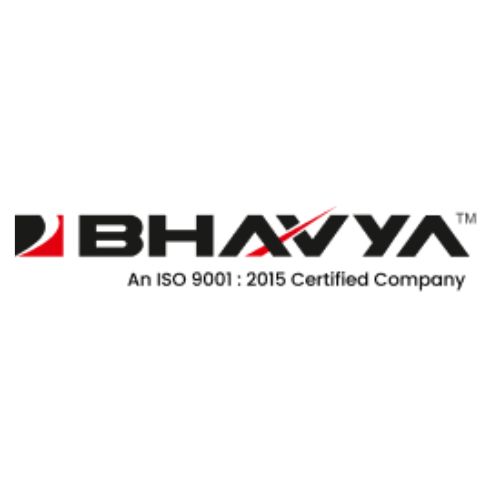
What are Combination Tools and how beneficial they are for Shaping?
What are combination tools? Selection of specific apparatus stays the key point of achieving unusual kinds of shaping. Apart from implementing dies, addition of utensils can help in enhancing machining operation. This methodology also provides good results in terms of…
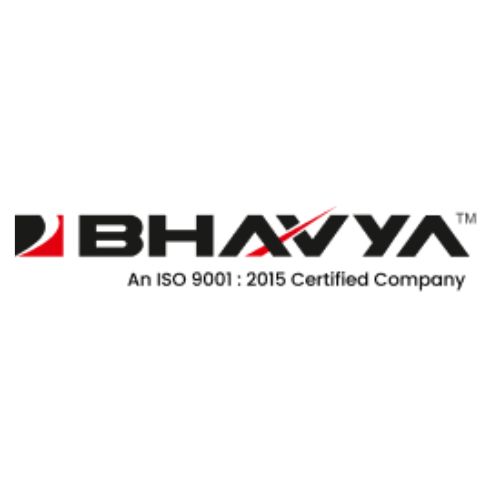
5 Important Revisions in Traditional set up of Press
Traditional Press Setup Traditional press brake setup was found to be with hydraulic principle and the usage can be traced back to ancient Mesopotamia and Egypt. Later as years went on Greeks introduced some changes into the provisions considering suitability…
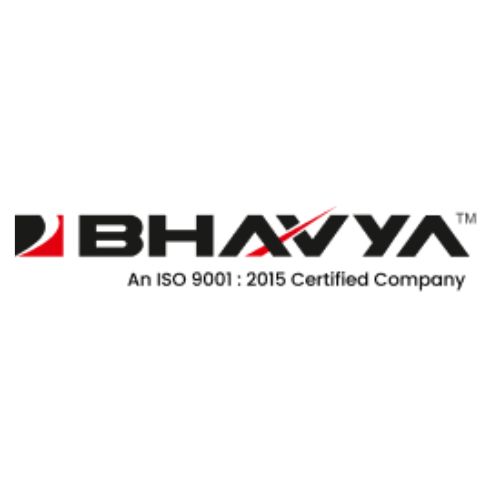
All About CNC workshop Machineries
Automated Operation Features in Workshop Machineries Machines that are applied to carry out critical core engineering works are termed as workshop components. These components were in use since several years back; however, with the advent of designing machines with computer…
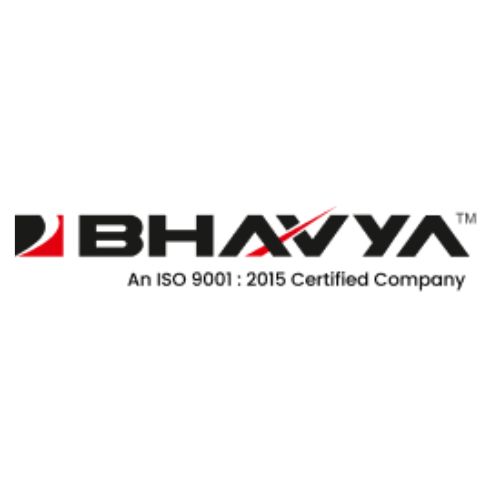
Environment Friendly Features of Press Brake
Machineries, Industry and Environment Industries that depend on machineries remain hindrance to environment in terms of the noise emitted from the industrial premises and the wastes removed. These factors certainly pollute the atmosphere in some way or other. Common Hindrance…
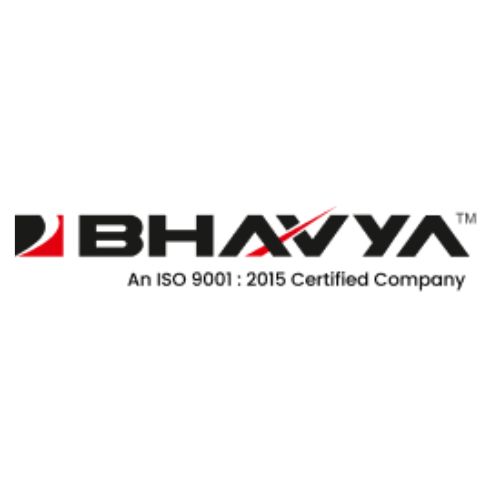
What makes Mechanical Press Brake Special?
Press brakes are depended on in engineering industries for sheet bending requirements. It shows higher performance and speed production for large engineering requirements. However, buying a press from a reputed manufacturer is more important than just investing for the sort…
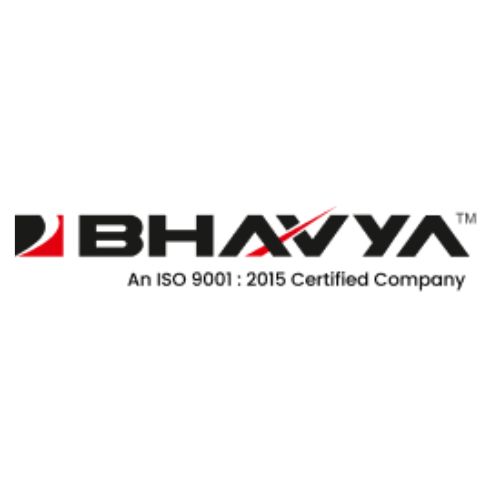
All About Mechanical Press Brake
Importance of Press Brake A press brake is a machining component applied for easy way of bending metal sheets. It is possible to make pre-determined bends and there stays the importance of this workshop device. What make Mechanical Press Brake…
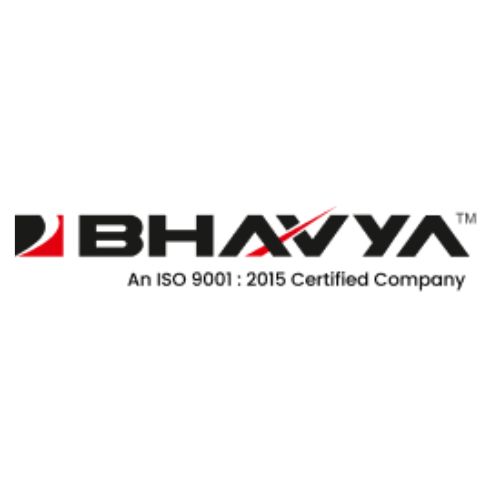
Does the Hydraulic Principle Support for Energy Saving?
What is Hydraulic Principle? A hydraulic fluid helps to run the machinery hence, that works with hydraulic system offers great value. Large force can be generated with hydraulic fluids and can stay a power saving option too. How Hydraulic Principle…
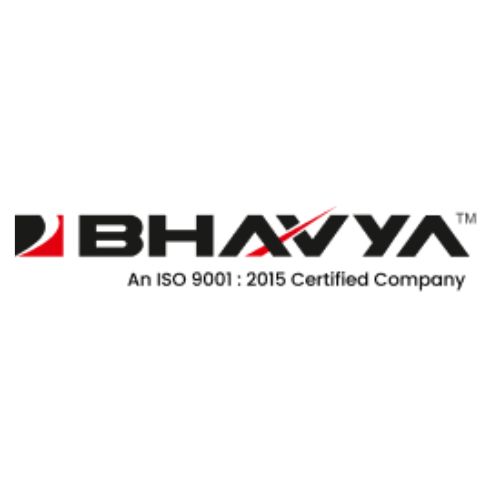
Contribution of the Press Brake in the Machine Tools Industry
This is a machine tool used for bending and forming of sheet metal and plate material. Markings are made on the material to be bent and pressed by the machine using a matching die. Press Brake for General Industrial Applications…
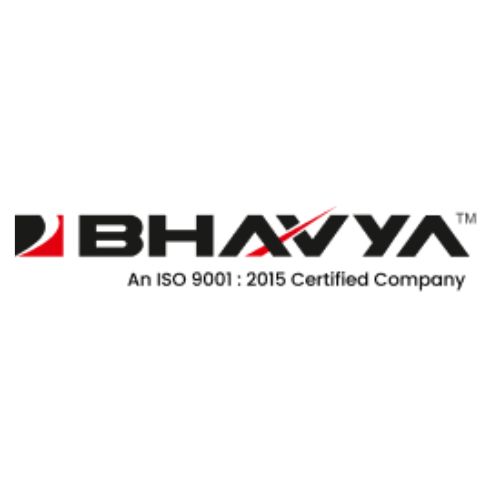
How to Improve the Production Capacity with Industrial Press Brake?
How industrial press brake applications help for industrial growth? Press brakes are an important machining device that is applied for bending different types of metal sheets wherein the bending shape and dimension required can be obtained by selecting the right…
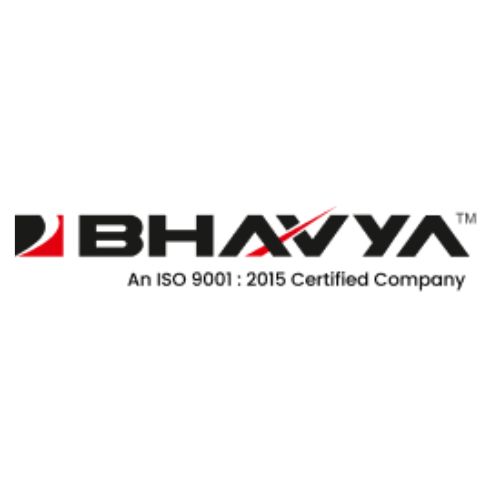
Possible Bending Variations with Press Brake
The Purpose of Press Brake A press brake is workshop equipment that is mainly used for bending metals and metal sheets. Wherein, it can be done either in V shape or U shape in accordance with the industrial requirement. It…
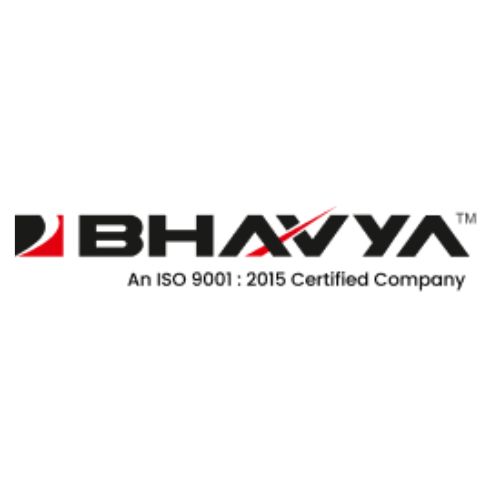
How are mechanical and hydraulic press brakes employed for sheet metal bending?
Press brake or break press is a equipments used for bending sheets of metals, or other materials. Prior to using a metal plate or a sheet it has to be shaped or formed. To do this a machine or a…
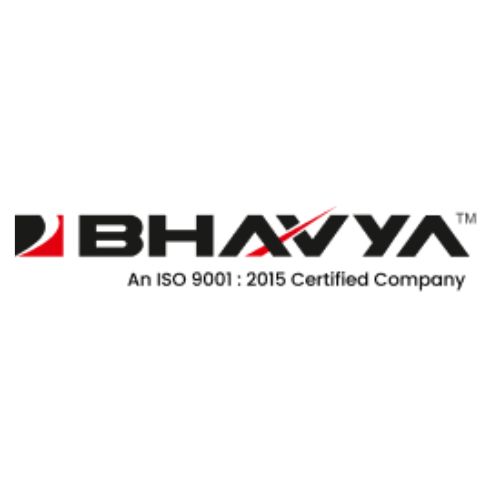
Set Up Procedure for Mechanical and Hydraulic Press Brake
Introduction - Press Brake It is a kind of bending machine used for bending sheet metal into a predetermined shape. The bending depends upon the shape of the punch and the die. These are being widely used in metallurgy, aircraft…
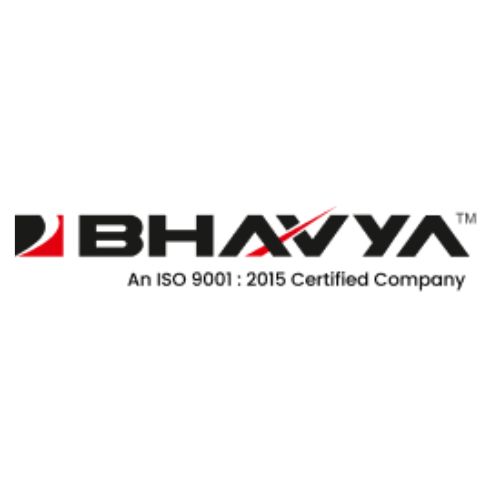
How does a Hydraulic Press Brake work to give a Customized Sheet Metal Bending Operation?
It is important equipment for the industries having jobs related to the metal shaping or bending. Two types are popular among metal fabricators – the manually operated press brakes and the press brakes which operate on the hydraulic power. The…
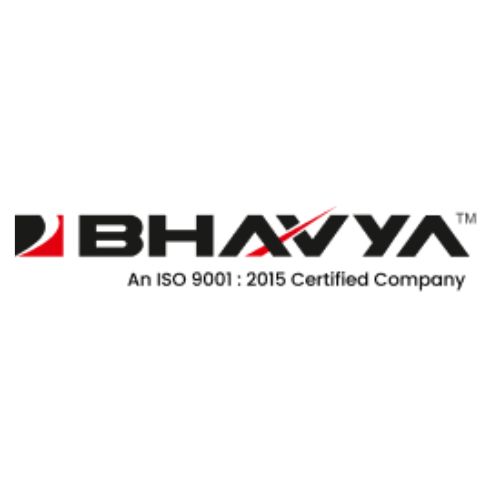
FAQs on Press Brake
A press brake is primarily used for accurately bending various types of metal sheets and plates. Some frequently asked questions are as follows: Q. What is camber? A. Camber is actually a small piece of cap which is placed on…
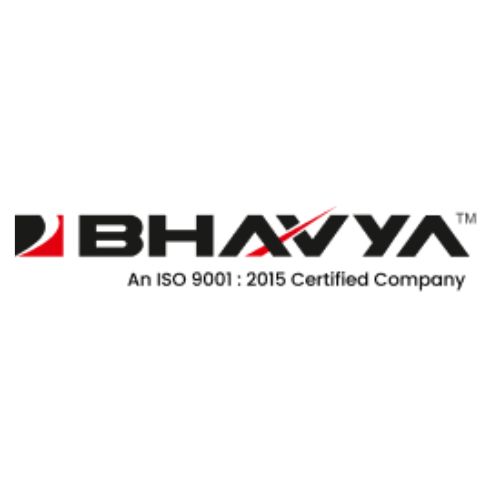
Sheet Metal Machineries for Shearing, Bending & Cutting
The various sheet metal machineries for shearing, bending and cutting are described below: Press Brake The mechanical press brake has a sturdy frame built from high grade steel. It also consists of steel plates with appropriate thickness and machined guide…
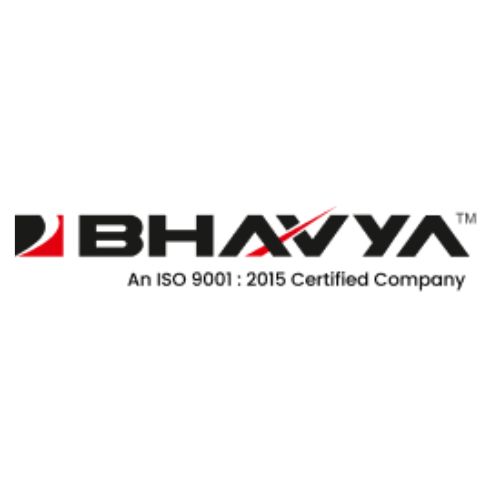
Significance of a Press Brake in Metal Cutting Applications
A number of machines are used in the process of fabrication of sheet metal parts. Fabrication is the process of collective operations which are used to give a shape to the metal sheet. This involves a number of equipments like…
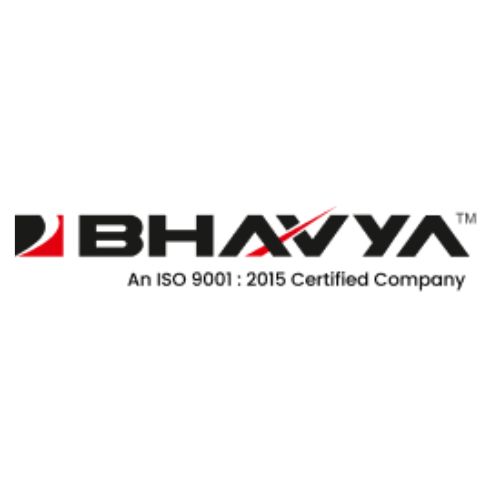
Press Brake, Slotting Machine – Machines used for Bending and Cutting Metals
Press Brake, Slotting Machine – It used for Bending and Cutting Metals Cutting and bending are the two primary functions performed on metals for casting the desired shape or dimensions. Therefore when it comes to metal working, the two most…
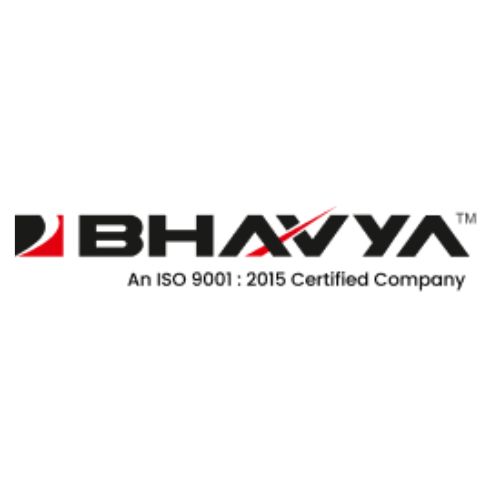
Applications of Different Types of Press Brakes – Mechanical & Hydraulic Press Brake
The press brake is primarily a machine tool that is utilized for bending a metal sheet or plate, into a shape which is determined by its die set. It forms preset bends by tightly holding the workpiece between the punch and die set.…
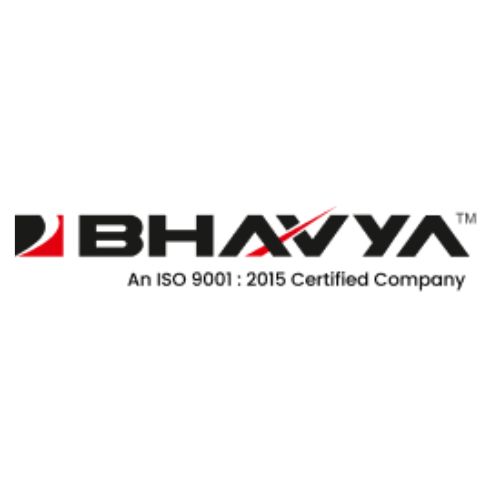
Selecting Right Type of Press Brake for Your Workshop
A press brake is also referred to as a brake press. It is basically a powerful machine tool that is commonly used for bending sheets and plates; particularly for bending sheet metal. It forms preset bends by holding the work piece in between the suitable punch…
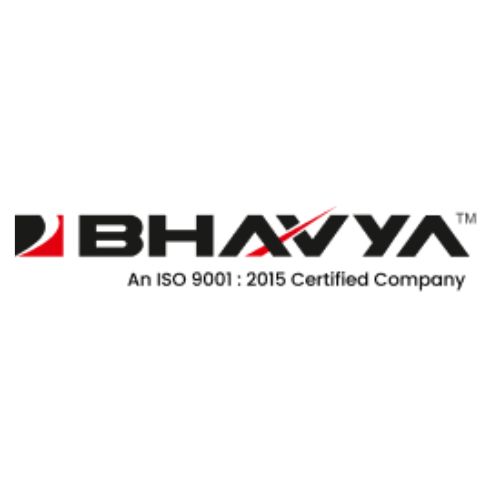
Mechanical Press Brake V/s. Hydraulic Press Brake – Which One is Better?
These days, various types of press brakes are available in the market, including mechanical and hydraulic. The main differences between a mechanical and a hydraulic is as follows. Hydraulic press brakes are simple to use and versatile for punching and…
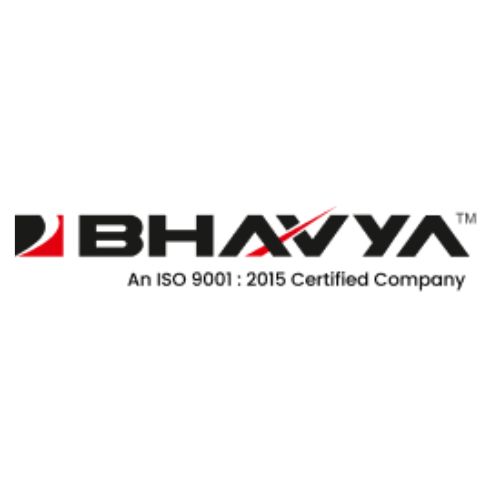
Important Tool Room Machines You Need to Buy for a Workshop
Improvement of processes in a workshop and automation doesn’t need to be an expensive affair. It needs to be a smarter choice of tool room machines required in a workshop. Various industrial applications require rigid material like wood and metal…
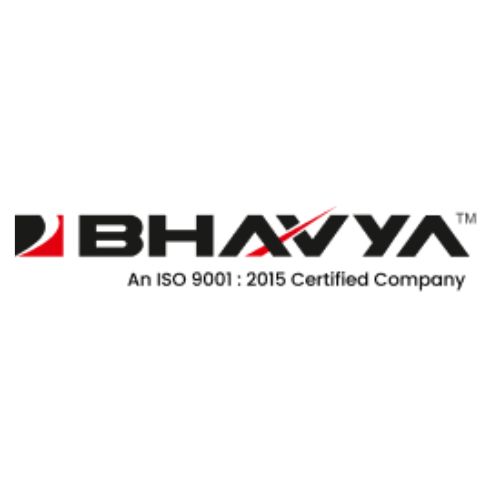
What is Press Brake?
Press brake is an important tool which is widely used in cutting metals in various shapes and sizes. It helps in forming predetermined bends in metal sheets by clamping the material between matching punch and a die. Thus, it uses…
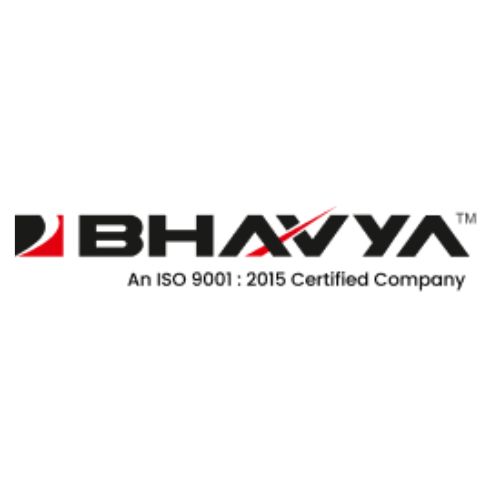
Uses of Lathe Machine, Press Brake and Grinding Machines in Metal Forming
Metals are casted into different shapes and sizes and used for various applications. This shaping and metal forming process is usually carried out with the help of various kinds of machinery in industries like automobile, engineering, electronics etc. Some of…
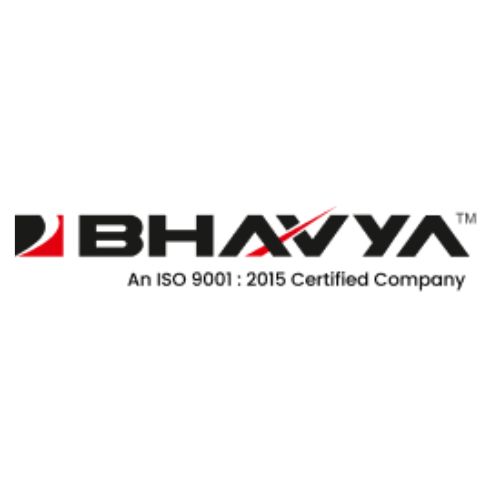
Metal Shaping, Sizing, Slotting & Bending with Machine Tools
Metal shaping and sizing is a big industries which needs heavy machine tools to differently shaping a cutting of the metals. Handling with tools are totally mechanical works with electrical integration. In this process metal work piece is carved by…
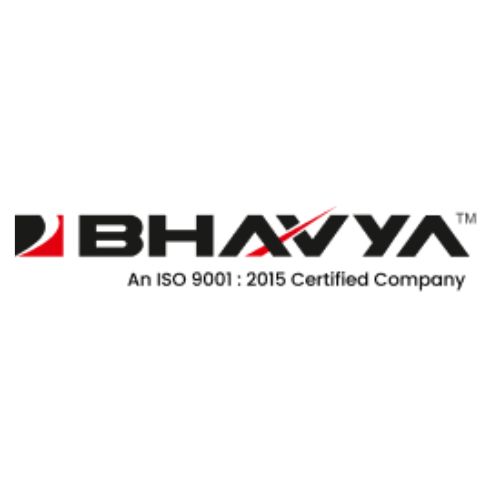
Sheet Bending – Press Brake, Power Press
Sheet Bending Process and Machines Sheet bending is a process of metal forming through which metals are bent into desired forms. In a sheet bending process the metals are casted into the required form by exerting a strong force on…
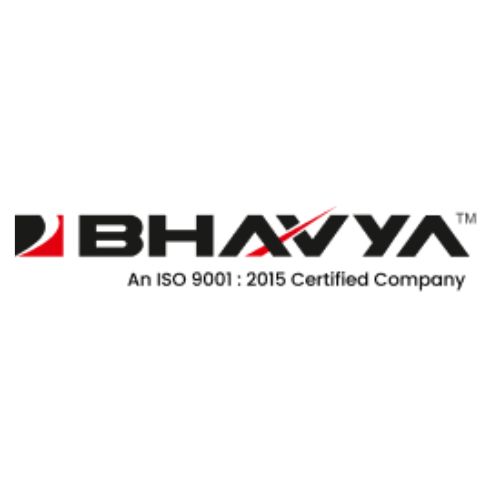
Machine Tools for Sheet Metal Industries for Slotting, Shaping & Bending
Slotting Machine for Sheet Metal Industry It is used to shape and cut metal, wood and other hard materials. It is a heavy duty machine with robust design and high speed equipment used in metal industries. Slot making applications are…
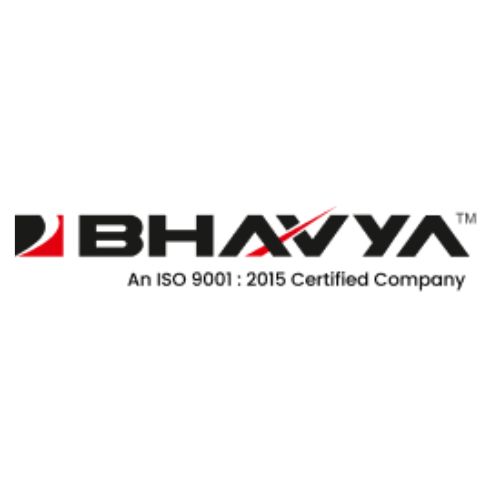
Metal Bending and Shaping Machines – Press Brake, Lathe Machine
Metal Bending and Shaping Machines – Press Brake, Lathe Machine Basically two types of equipments are widely used in metal forming industries. One is sheet bending and other is lathe. A sheet bending machine is the one that bends metal…
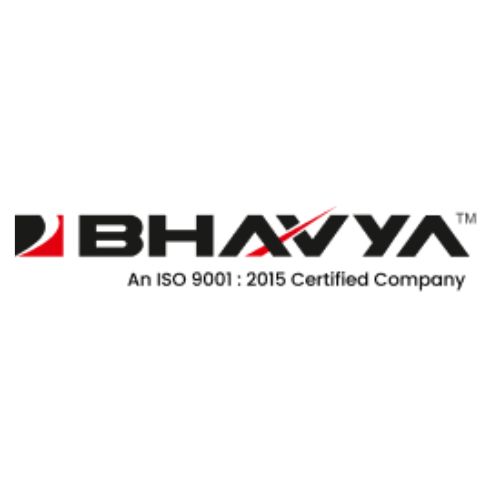
Sheet Bending with Press Brake
Sheet Bending with Press Brake Different kinds of machines are employed for sheet metal forming tasks in industries like lathe, sheet bending, power press, press brakes etc. It is a special kind of sheet bending machine that is designed to…
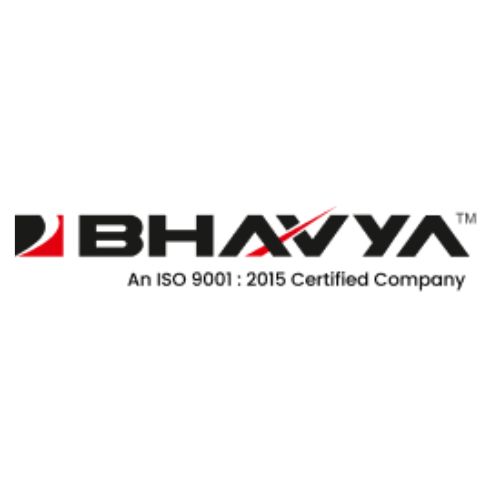
Press Brake – Types of Press Brakes, Applications of Press Brake
Press Brake Press brake is also known as “Brake press” or “Break” is a machine tool for bending sheet and plate material. It is described using two parameters – working length and force or tonnage. Who can operate the machine…