Monthly Archives: February 2022
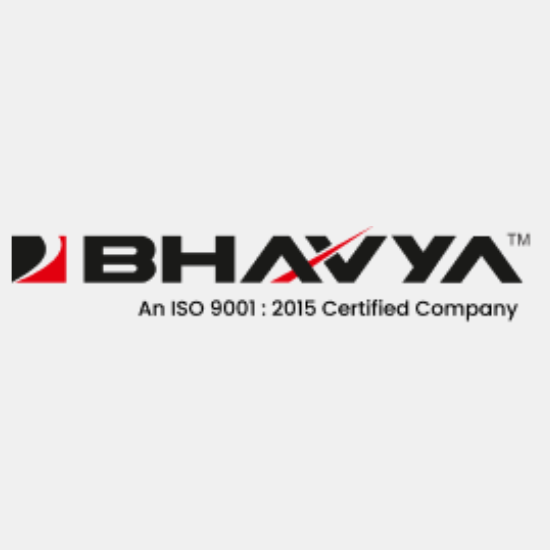
How to Install a Bandsaw Machine – User Guide
A bandsaw machine is a machine that shaves wood using a blade that is continuously rotating. It is powered by steam, electricity, or wind power. The process for removing the blade involves turning off the power, opening the cabinets, and…
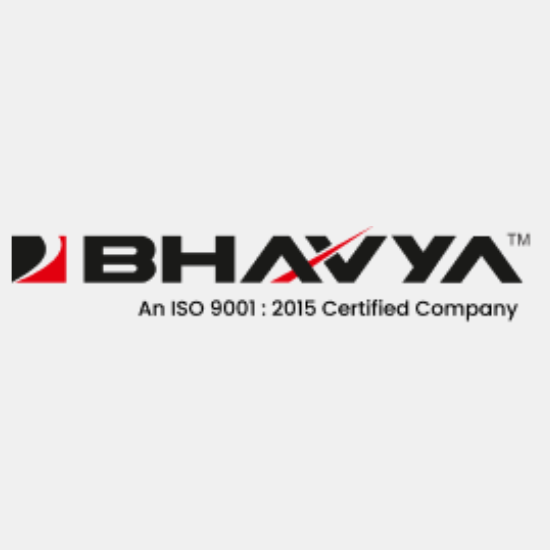
What Is a Turning Machine?
A Turning Machine is a machine that turns workpieces into various shapes. This process involves rotating a part while a single-point cutting tool moves parallel to the axis of rotation. The process can be performed on the external or internal…
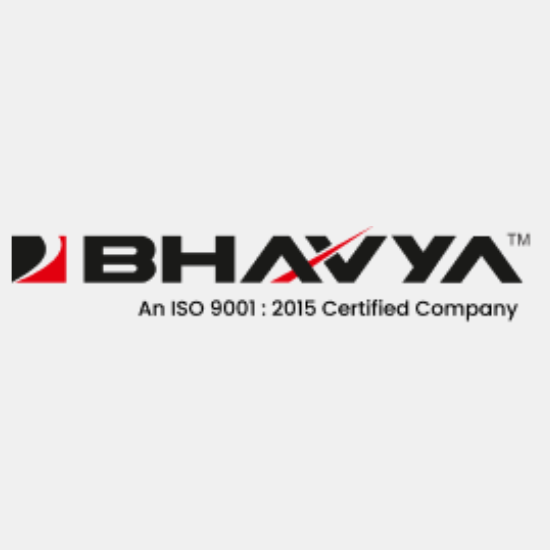
Radial Drilling Machine – An Overview
A radial drilling machine is a powerful drilling tool that performs heavy-duty operations on thick metals. These machines are used by thousands of global manufacturing companies to make holes up to 75mm in nearly any material. They are extremely versatile…
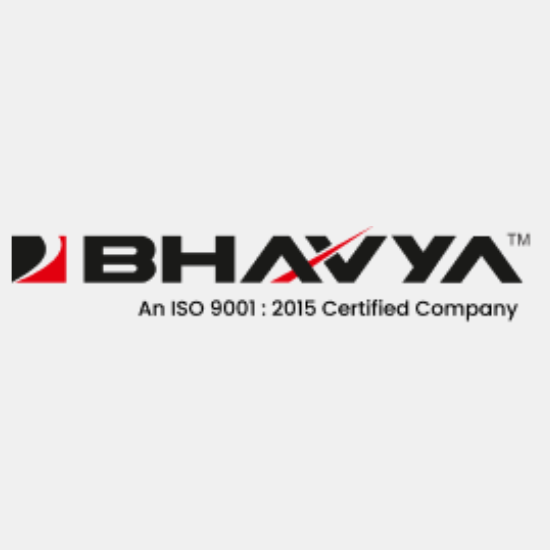
A Beginner’s Guide to Buying a CNC Lathe Machine
Before you buy a CNC Lathe Machine, it is important to learn about the different kinds. Different machines have different axes, and using different axes allows you to make parts of different sizes and shapes. You will also need to…
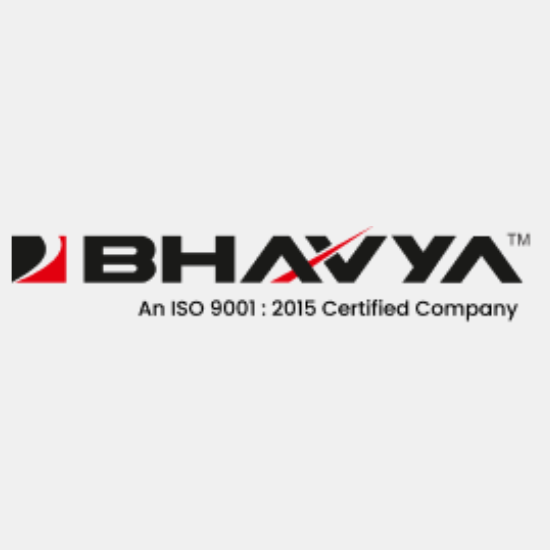
Purchasing a Pipe Bending Machine
Purchasing a Pipe Bending machine is an essential part of installing piping in the home. The right pipe bender can ensure a perfect fitting of your pipes. There are several factors to consider when purchasing a pipe bending machine. The…
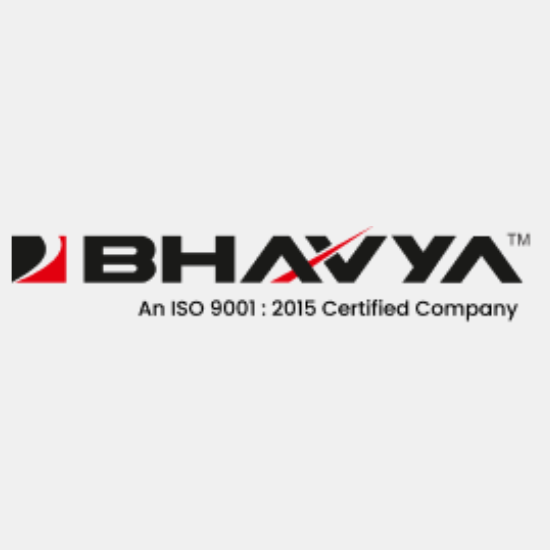
Choosing a Sheet Metal Bending Machine
When choosing a sheet metal bending machine, it is important to choose the one that can handle the materials you plan to bend. Each type has specific requirements for the materials that can be bent. The inner radius of the…
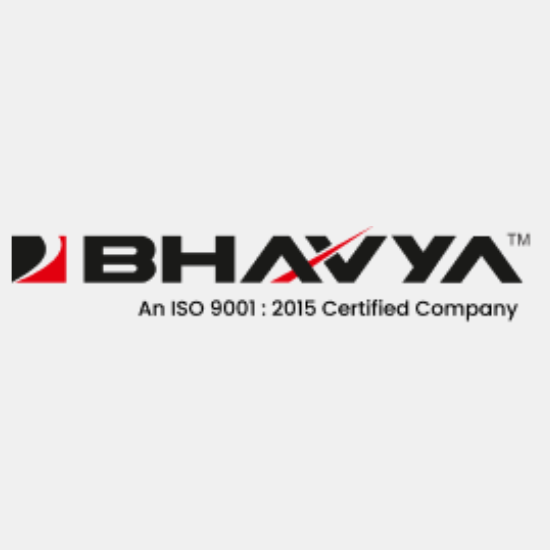
Features of a Spot Welding Machine
A Spot Welding Machine is used to permanently weld two pieces of metal together. The electrodes remain on the metal spots after the weld is finished and the controller is turned off. The welding process completes the fabrication of the…
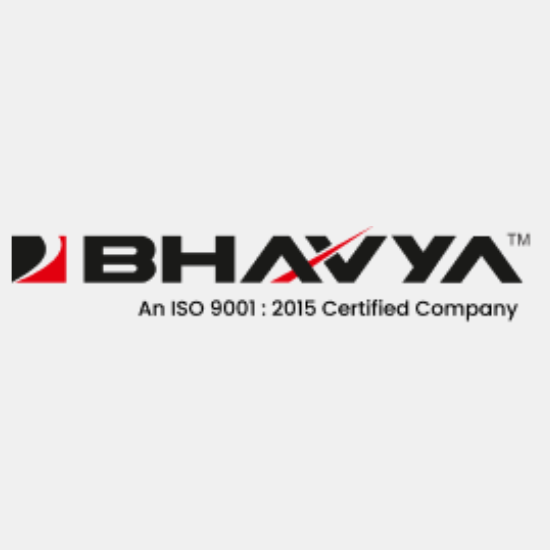
Pillar Drill Machine – Features & Applications
A pillar drill machine is an ideal choice for any project. Its large power capacity and large drilling speed make it suitable for heavy load situations. Usually, it is fitted with a quality chuck key and a separate work table…