Monthly Archives: September 2022
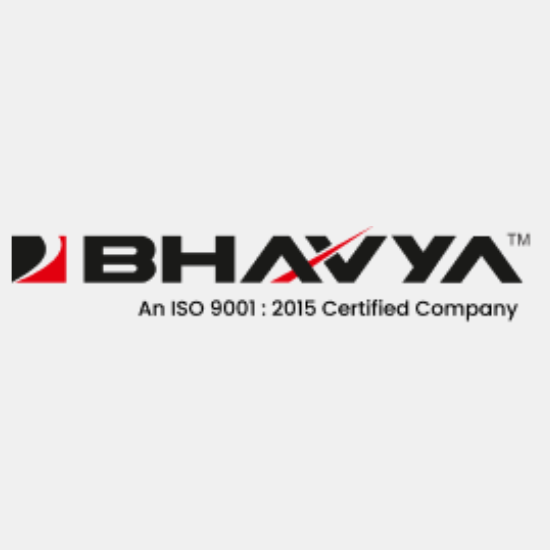
Choosing the Right Chamfering Machine
A Chamfering Machine is used to produce chamfers on pieces of metal. There are several different types. Choosing the right machine depends on the type of chamfer you want to make. This article will provide you with some information on…
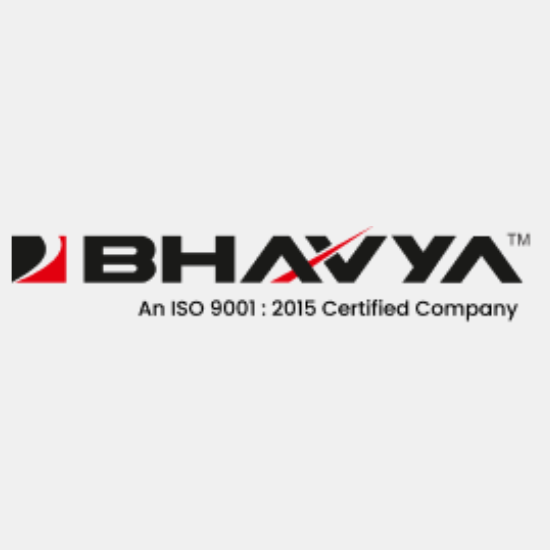
An Overview of DRO Lathe Machines
DRO (Digital Readout) lathe machines are used to measure and record the diameter and radius of workpieces. They are especially useful when cutting slots and features and can serve as a calculator for users. In addition to being useful calculators,…
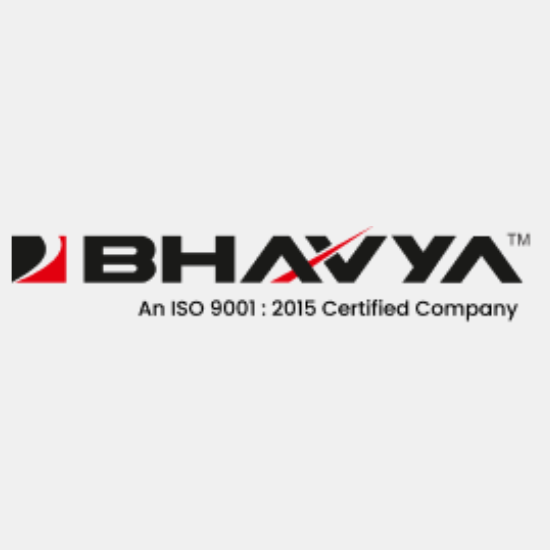
Types of Metal Forming Machines
There are several types of metal forming machines: press braking, wire bending, roll forming, and forging. The three types are discussed in this article. Which one is best for you? Here are some tips to help you choose the right…
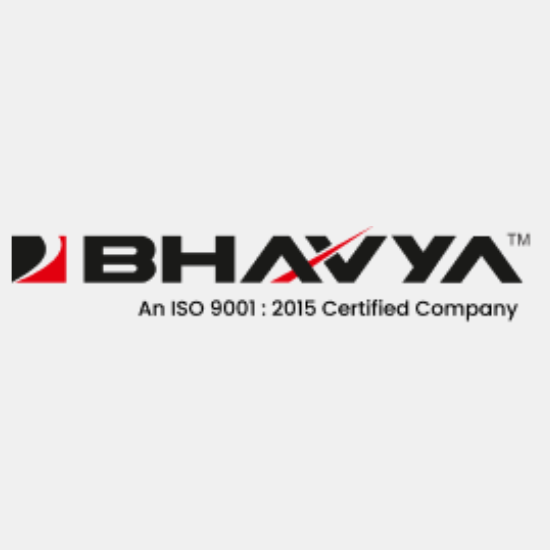
Benefits, Features & Applications for a Sheet Folding Machine
The fundamental bending process involves deforming a sheet of metal in one axis. A sheet metal folding machine bends the sheet through tension and compression. Tension bends the outer part, while compression bends the inner part. This process does not…
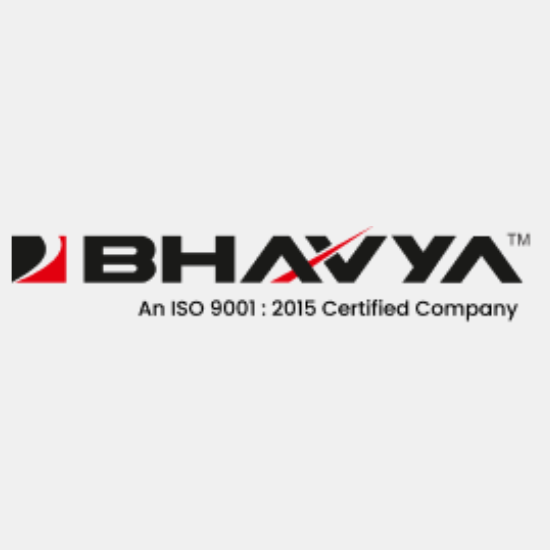
The Benefits of Using a Slip Roll Machine with its Working
Listed here are some of the benefits of using a Slip Roll Machine. First and foremost, the machine is durable and able to form a metal plate. Its large handle crank and hardened gearing make it a sturdy choice for…
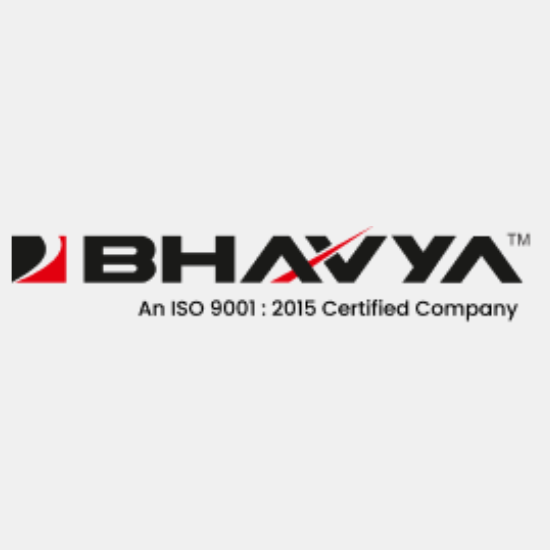
Hydraulic Press Brake – What You Should Know Before Purchasing?
There are several things you should know before purchasing a Hydraulic Press Brake. This article explains some of the key features of these machines and their benefits. In addition, this article will explain how deflection compensation works, Adjustable gauge, and…
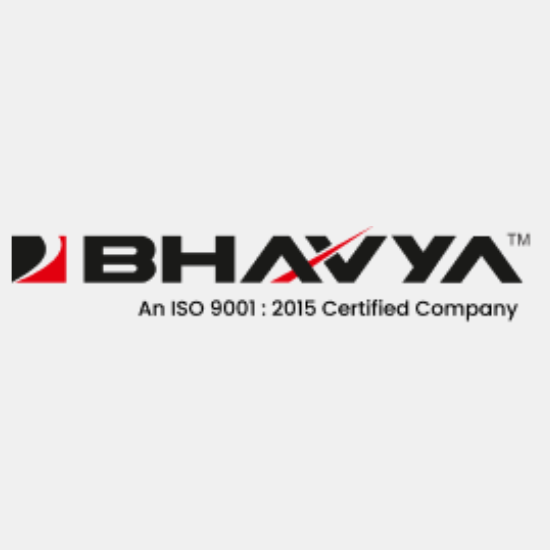
Benefits of an Angle Cutting Machine
If you are considering purchasing a new machine for your manufacturing operation, you may want to consider the benefits of an Angle Cutting Machine. This machine allows you to reduce human resources and energy expenditure while cutting products of high…
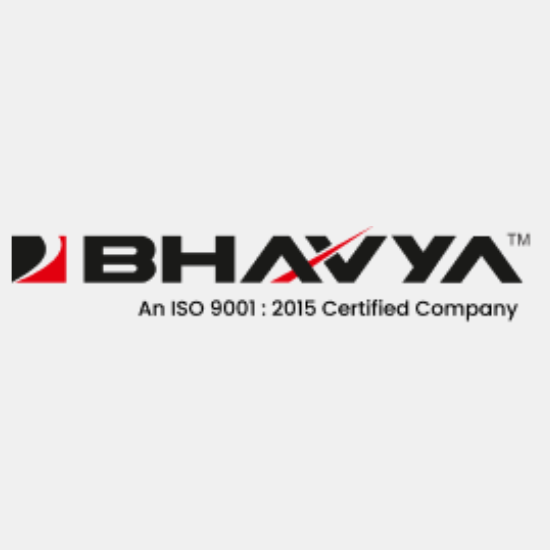
Keyway Milling with CNC Milling Machine
If you are a manufacturer of a variety of different types of products, you may want to consider using a Milling Machine to perform the necessary operations. This type of machine is used to create complex shapes using different kinds…
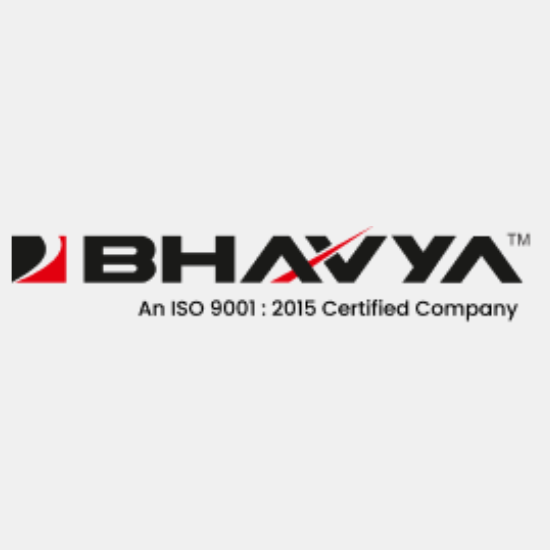
High-Speed Precision Lathe Machine – Features, Functions, & Specification
In this article, we will look at the features, functions, and specifications of the High-Speed Precision Lathe Machine. We will also discuss the price and the specifications. In the end, you will be able to buy the perfect machine for…
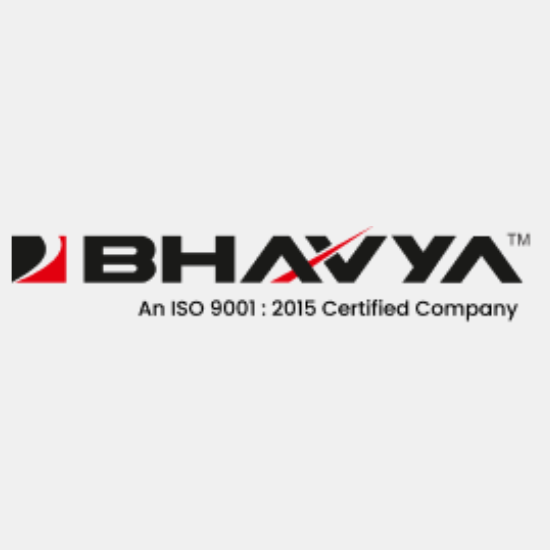
An Overview on Hydraulic Pipe Bending Machine, and Offset Bending Tool
In this article, we will look at the advantages and disadvantages of pipe bending machines. These machines are used to bend pipe and tubing into a variety of shapes. These machines are available in various sizes and can be used…
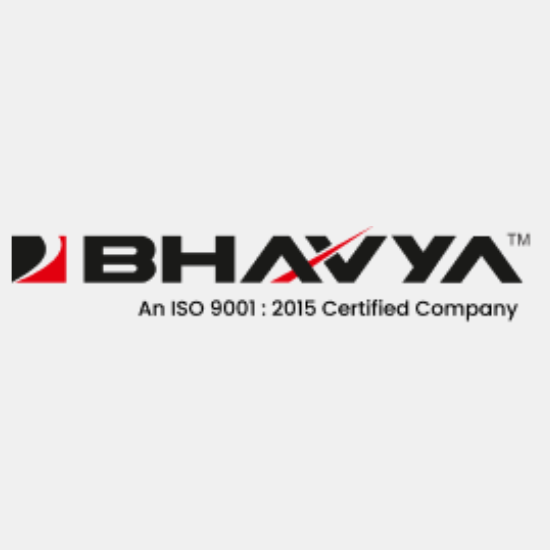
Press Brake Demand in UAE
What is driving the Press brake demand in the UAE? What are the opportunities and threats in this market? How will you segment this market? Here are some of the key points to consider. In addition, we will discuss the…
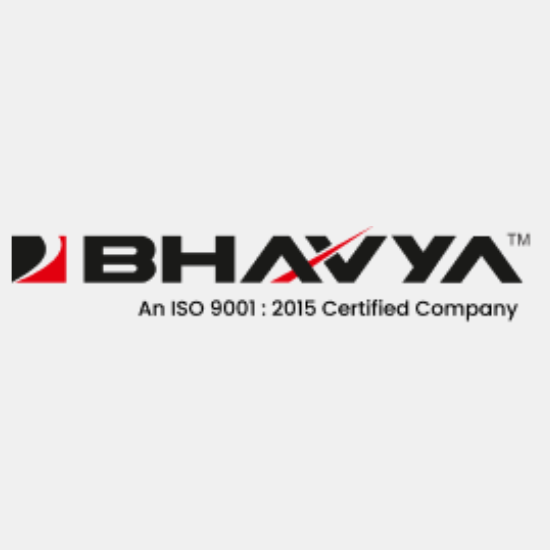
Benefits, Variability and Flexibility of an NC Bending Machine
If you've been considering an NC Bending Machine for your business, you've probably wondered about the benefits and limitations of these machines. In this article, we'll look at the cost, flexibility, and variable nature of NC bending machines. You'll also…
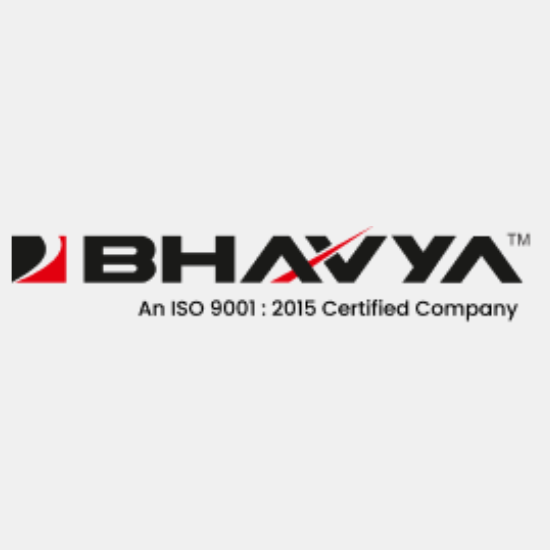
Salient Features, Working & Application Electric Tapping Machine
The electric tapping machine is a very useful machine that is used for threading holes in steel items. Its working capacity and precision are highly recommended by engineers. Moreover, this machine is very efficient and time-saving. It is also suitable…
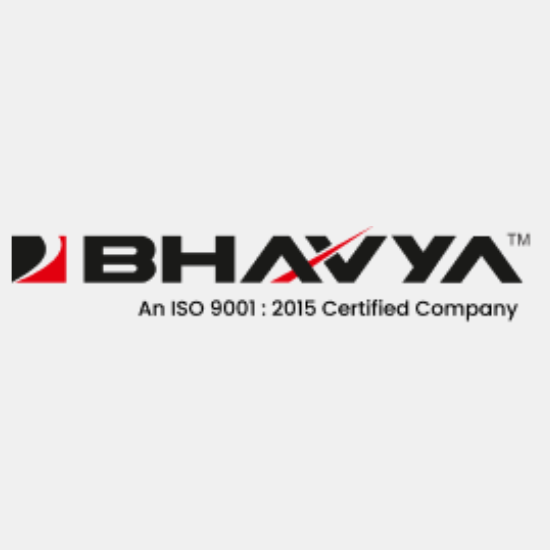
Features, Benefits & Applications of Pipe Cutting Machines
A Pipe Cutting Machine is a piece of plumbing equipment used to make a clean cut in pipes. It is more efficient than a traditional hacksaw, and can be faster and cleaner. The utility of a Pipe Cutting Machine depends…
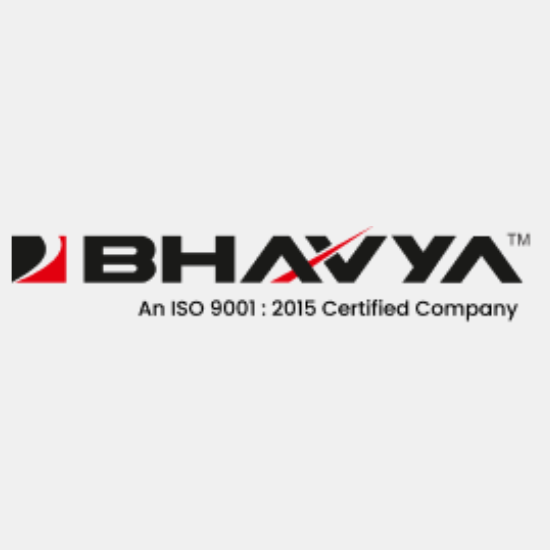
Hydraulic Press Brake Features
When shopping for a hydraulic press brake, you need to pay close attention to a few factors. These include accuracy of.0004", large strokes and daylights, and deep throat depth. In addition, you need to consider how much force it can…
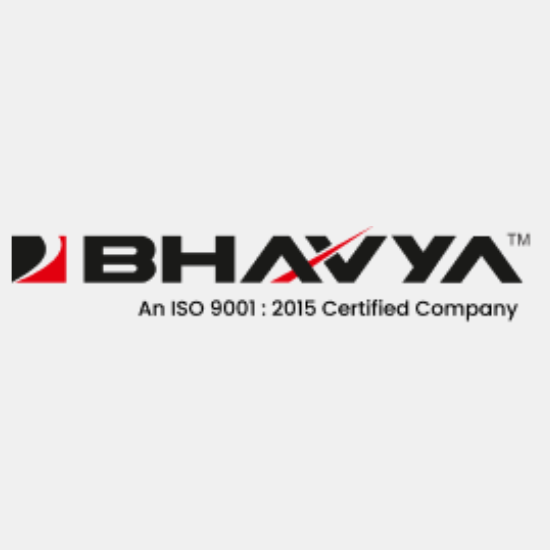
Tips for Choosing a CNC Press Brake
A CNC Press Brake machine is a great option for a company that produces large quantities of finished products. The main considerations for selecting a CNC Press Brake are the complexity of the designs to be created, how many axes…
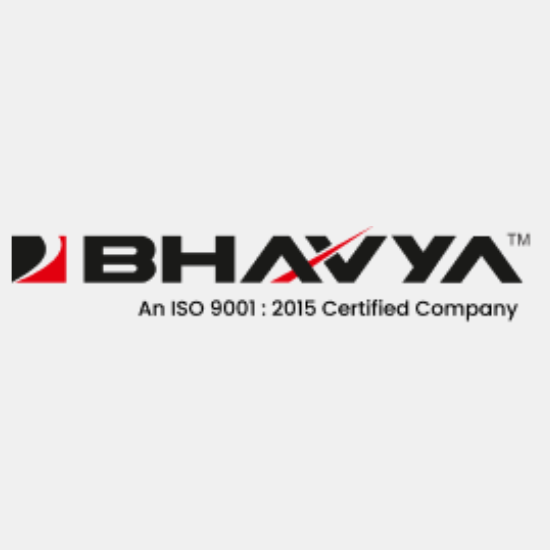
How to Adjust a CNC Bending Machine?
A CNC Bending Machine is a machine that automates bending metal tubes or wires. A single machine does the entire process, eliminating the need for a laborer or another machine to feed the metal tube or wire. This process reduces…
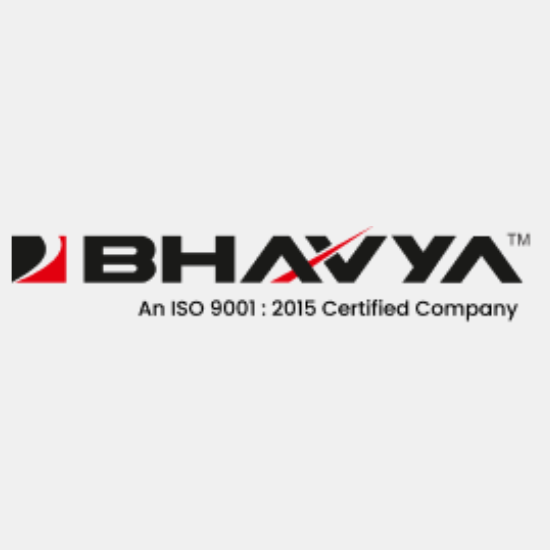
How to Use a Vertical Bandsaw Machine?
A Vertical Bandsaw Machine is an advanced single blade machining unit, capable of cutting timber of various thicknesses and producing high-class finish. A Vertical Bandsaw Machine consumes less electrical power. They are also built with a sturdy frame and machining…
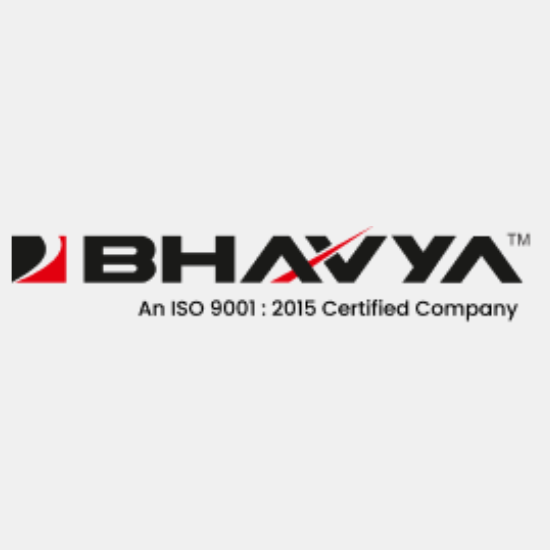
Advantages of a Fiber Laser Cutting Machine
A Fiber Laser Cutting Machine has many advantages over its other counterpart. The main benefits of this type of machine are its high accuracy, low heat input, and low operating costs. Here are some of its key benefits: High accuracy…
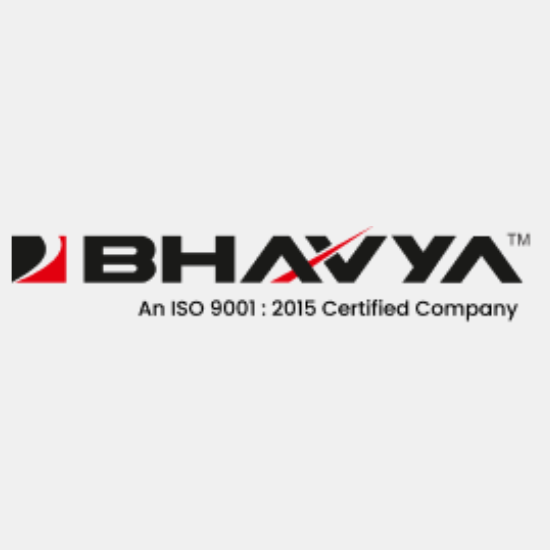
Benefits of a Hydraulic Shearing Machine
A Hydraulic Shearing Machine is a kind of shearing machine that applies a full shear force to the workpieces. These machines are very effective in cutting materials that are difficult to cut otherwise. These machines are highly versatile and have…
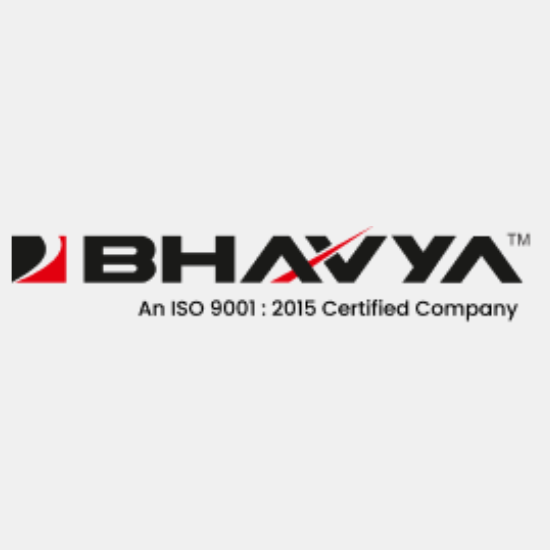
Get an Overview on Fiber Laser Marking Machine
You may be wondering if this new technology is worth the price tag. The answer is yes. Laser marking machines are incredibly versatile and can mark virtually any type of metal or non-metal item. And, a Fiber Laser Marking Machine…
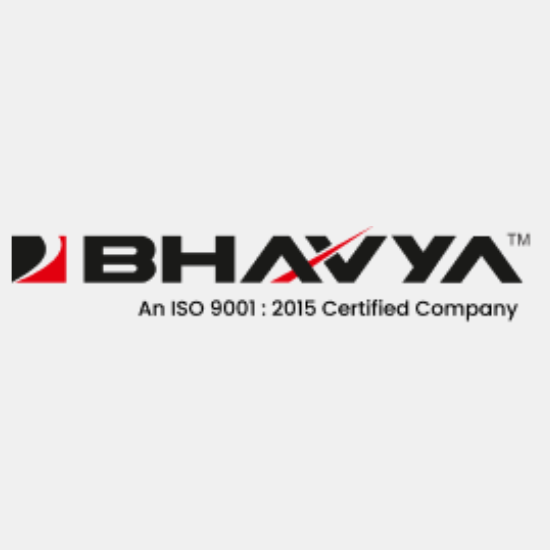
Factors to Consider When Choosing a Drilling and Milling Machine
A Drilling and Milling Machine is the most useful tool for cutting metal parts, such as drill bits and bolts. These machines offer different features, such as cutting horizontally and vertically. Although drills are an ideal choice for beginners, milling…