Category Archives: Chamfer Machine
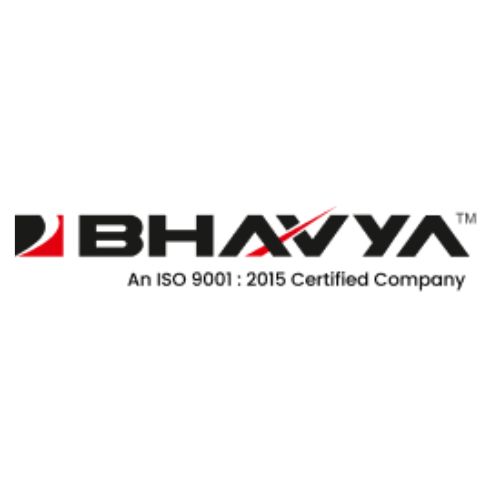
The Uses of Chamfer Machines in Bahrain’s Oil and Gas Industry
Bahrain’s oil and gas industry is the backbone of its economy, contributing significantly and fostering industrial growth. This sector, characterized by its demand for precision and durability, relies on advanced machinery to ensure safety and efficiency in operations. Among these…
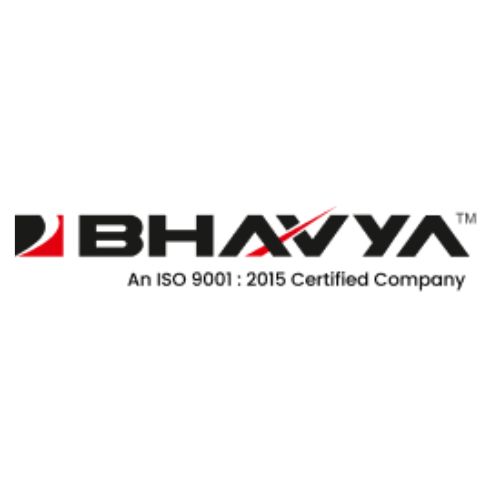
Demand and Supply of Industrial Machine Tools in Bahrain
Introduction Bahrain, a growing industrial hub in the Gulf region, relies heavily on advanced machine tools to meet its manufacturing, construction, and electrical fabrication demands. Machine tools like Universal Tool Grinders, Busbar Punching Machines, Hydraulic Iron Worker Machines, and Blade…
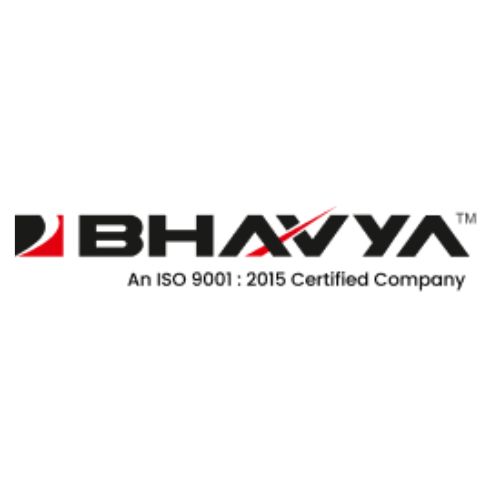
Demand and Supply of Machine Tools in Kuwait for Various Industries
Kuwait’s industrial sector is expanding rapidly, driven by advancements in construction, manufacturing, and metalworking industries. At the core of this growth lies the increasing demand for machine tools. Tools like Hydraulic Iron Workers, Grinding Machines, and Blade Sharpeners are essential…
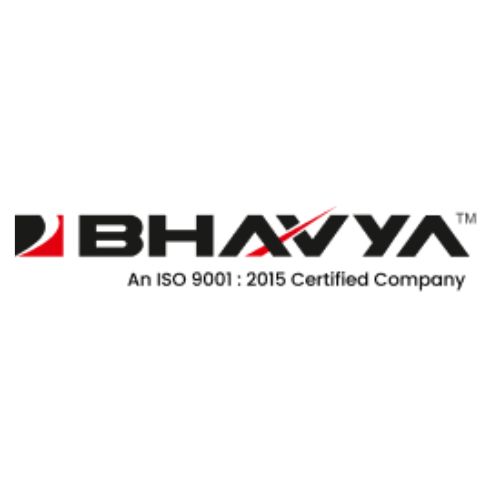
Power of Chamfering Machines in Manufacturing Industries
Chamfering machines are essential tools used in various industries for the purpose of creating bevelled edges or chamfers on work pieces. These machines play a crucial role in achieving precision and efficiency in the manufacturing process. Chamfering machines are specialized…
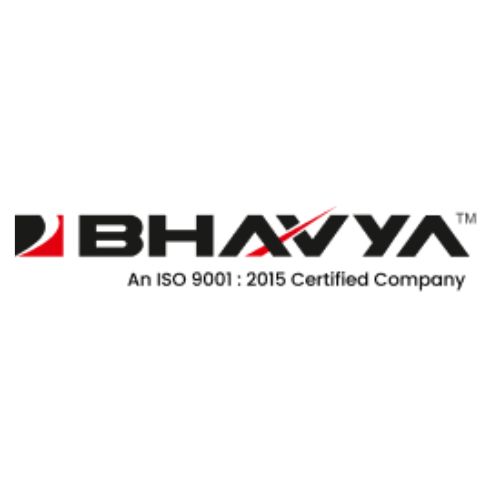
Maintaining and Troubleshooting Chamfering Machines
Chamfering machines are essential tools used in various industries for creating bevelled edges and chamfers on different materials such as metal, wood, and plastic. These machines provide precision and efficiency in shaping and finishing work pieces but like any mechanical…
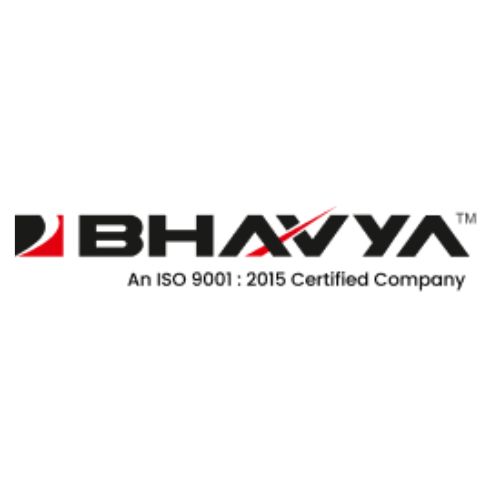
Applications of Chamfering Machines in Different Industries
Chamfering machines are versatile tools that are widely used in various industries for different applications. These machines are designed to create beveled edges, or chamfers, on a workpiece, providing a smooth and finished look. With their ability to perform precise…
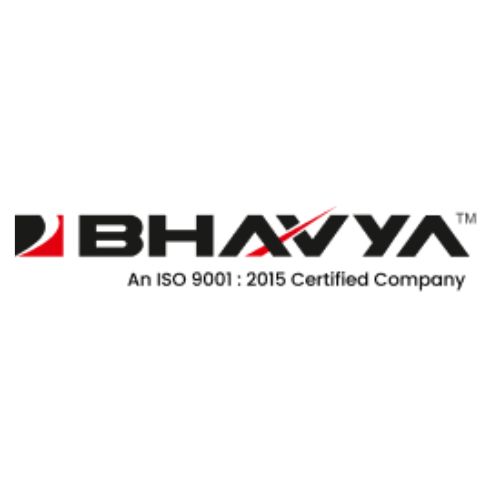
Future Trends in Chamfering Machine Technology
Chamfering machines have been an integral part of manufacturing processes for decades, providing precise and uniform beveling to different materials such as metal, wood, and plastic. However, with advancements in technology, chamfering machines are undergoing significant transformations, enabling manufacturers to…
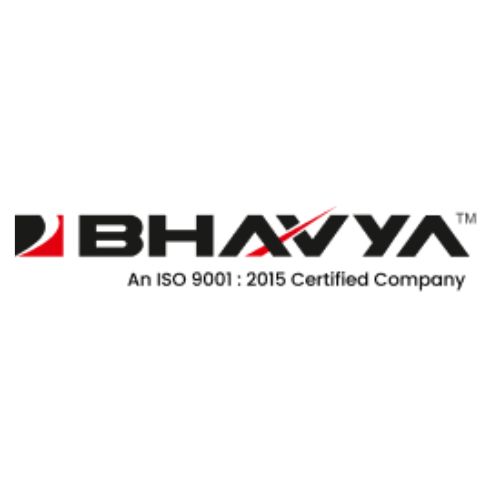
All About Chamfer Machine
A chamfer machine is a machine tool that is used to create a chamfer, which is a beveled edge on a workpiece. The chamfer machine can be used to create chamfers on a range of materials, including metal, plastic, and…
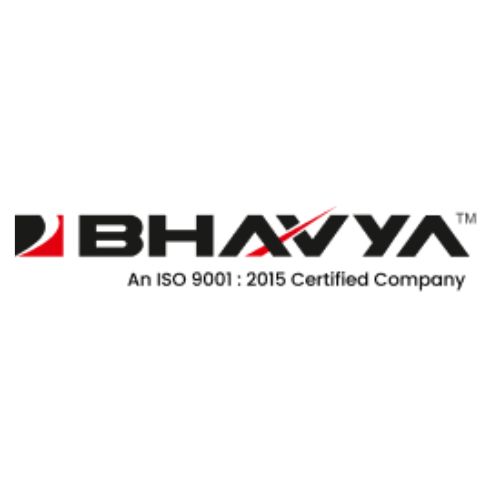
Choosing the Right Chamfering Machine
A Chamfering Machine is used to produce chamfers on pieces of metal. There are several different types. Choosing the right machine depends on the type of chamfer you want to make. This article will provide you with some information on…
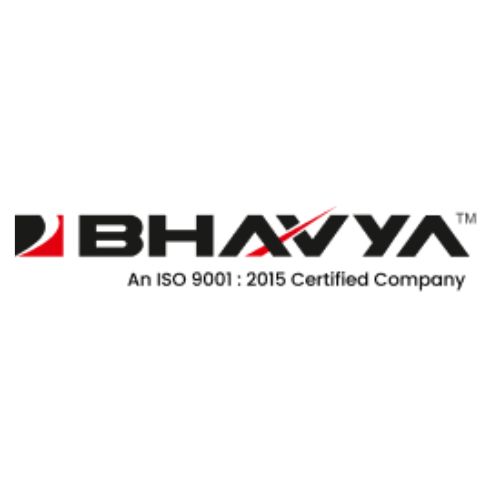
The Advantages of a Chamfer Machine
If you are looking to buy a Chamfer Machine, you have a few options to choose from. There are several advantages of this type of machine and some are more appropriate than others. This article will cover the most important…