Monthly Archives: April 2012
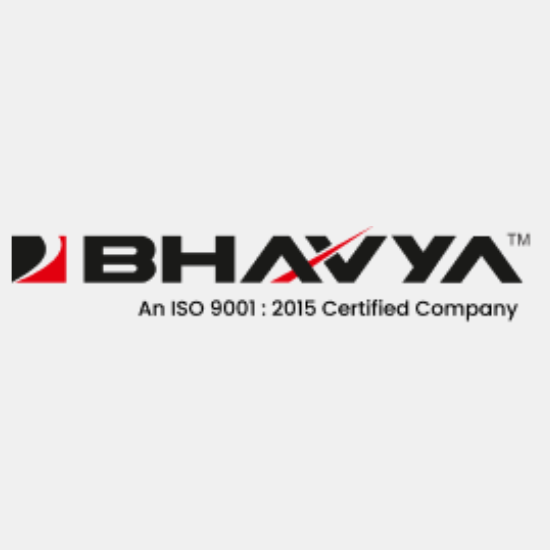
Drill FAQ – What is Drill, Types of Drills, Drill Bits, Safety Measures of Drill Machine
DRILL FAQ Drill FAQ will give you idea about the types of drill machines and their various industrial applications. Here it is tried to describe the common queries and needful information for drilling machine. For further query about the tools…
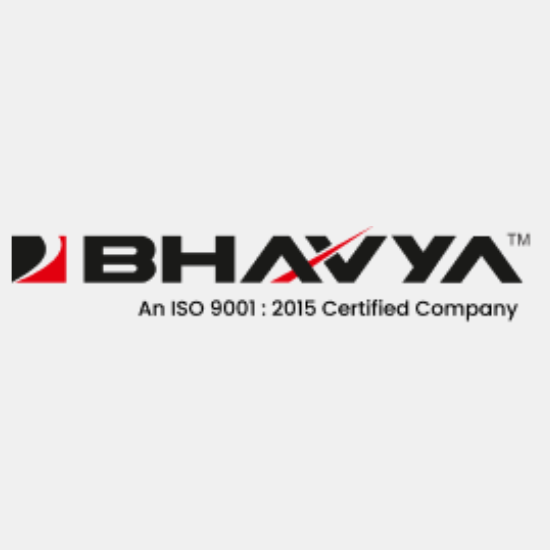
Drill Machine – Types of Drills, Applications of Drill Machines
Drill Machine Drill is a machine tool used for drilling the holes in solid materials like metal and wood with drill bit or driver bit. Drills are used in wide range of applications in metalworking, constructions and woodworking industries. The…
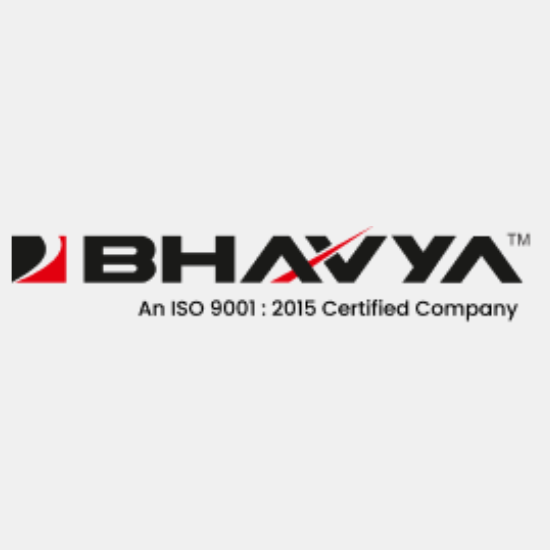
Tool Room – Types of Tool Room Machines, Toolroom Setup
Tool room Tool room is the room where the tools are kept for storage, prepare, repairing and machining. The space area can be varied based on the types of the tool room machines and applications. It may include high end…
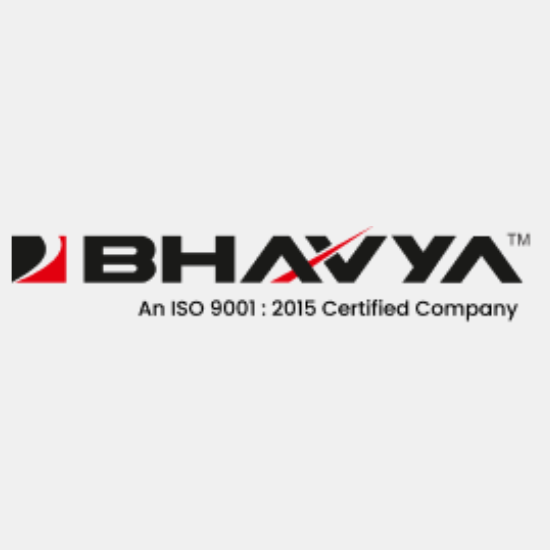
Uses of Lathe Machine, Press Brake and Grinding Machines in Metal Forming
Metals are casted into different shapes and sizes and used for various applications. This shaping and metal forming process is usually carried out with the help of various kinds of machinery in industries like automobile, engineering, electronics etc. Some of…
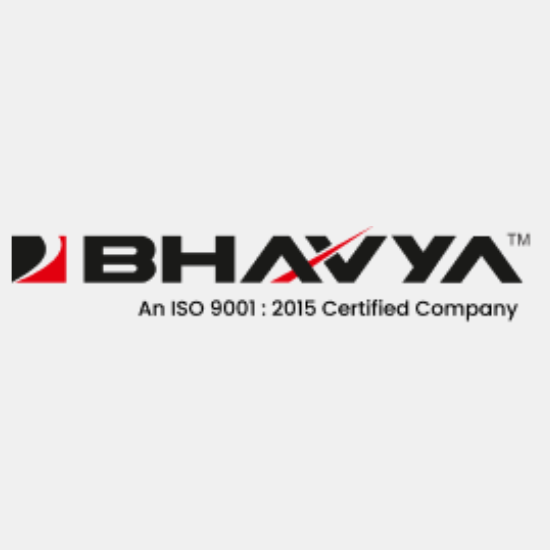
How to Select Power Press for Metal Forming Applications?
Press machines or press brakes are the most important metal shaping tools. With these one can easily bend, cut and form the shapes of various kinds of metals. Different kinds of press machines are available in the market today. There…
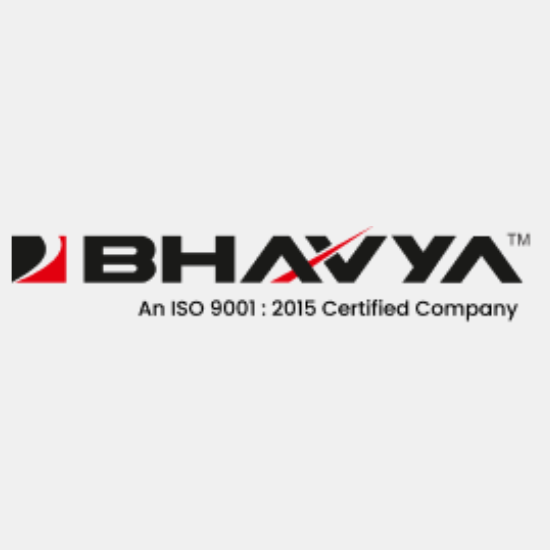
Machine Tools – Grinding Machine, Shaping Machine, Milling Machine
Grinding Machine Grinding machine is one of the important tools for industrial usage. It is also referred as Grinder. It has two abrasive wheels for grinding the work piece. Grinder can be used to cut and grinding the work piece…
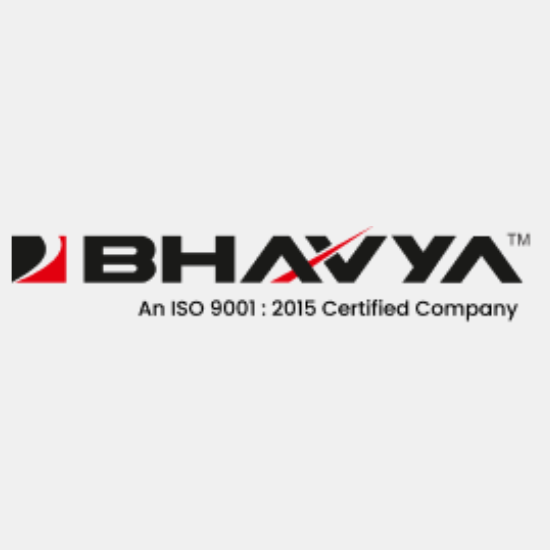
Metal Shaping, Sizing, Slotting & Bending with Machine Tools
Metal shaping and sizing is a big industries which needs heavy machine tools to differently shaping a cutting of the metals. Handling with tools are totally mechanical works with electrical integration. In this process metal work piece is carved by…
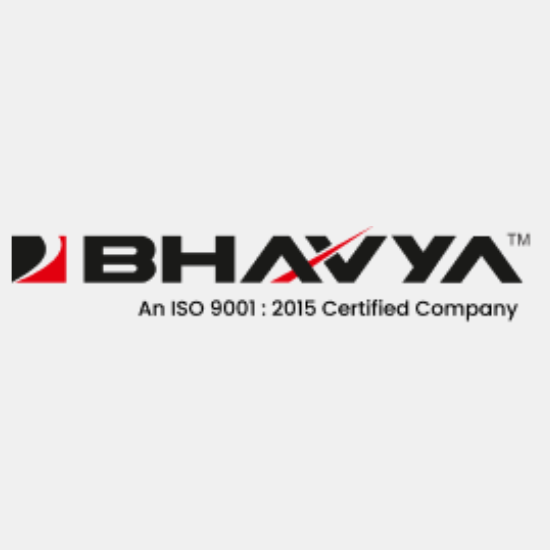
Types of Machines Used for Shaping and Cutting Metals
Types of Machines Used for Shaping and Cutting Metals The use of metal has become essential in many industries like automobiles, construction, electrical, furniture etc. Thus, there are many equipments used for shaping and cutting metals for the faster production.…