Monthly Archives: December 2012
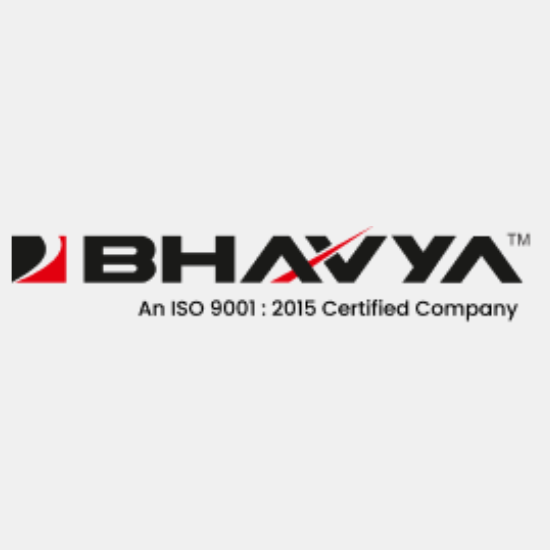
Application of Workshop Machinery
These days, a wide range of workshop machinery is manufactured to fulfill the diverse requirements of various industrial segments. Moreover, each of these has distinct features, and every is used for a specific purpose. The commonly used workshop machines include…
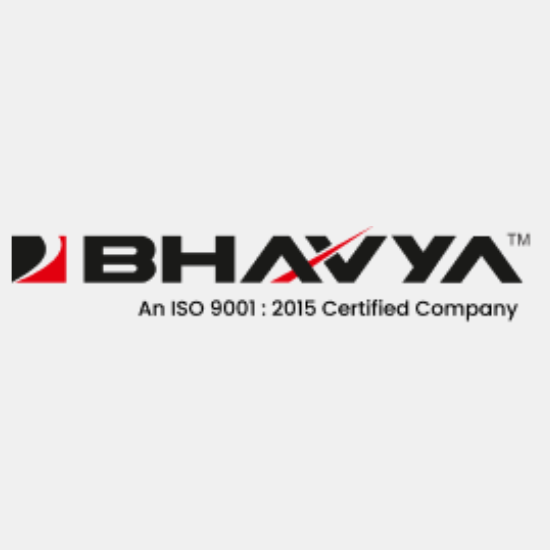
Types of Milling Machines and Selection Guide for Workshop
A milling machine is a versatile tool that is widely used in the metal industry for performing several tasks such as milling, cutting, threading, carving, drilling, planing, contouring, die-sinking, etc. These milling tool have a cutter that can move at…
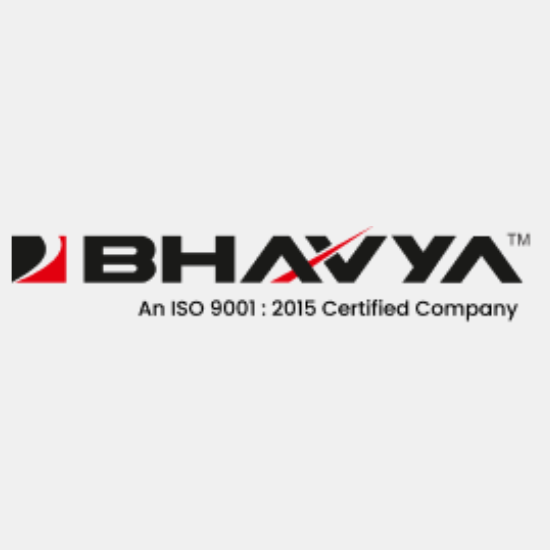
All You Should Know About Machine Tools
A machine tool which is used for machining or shaping metal or any other solid material, by various methods such as cutting, grinding, milling, shearing, boring; or other suitable ways of deforming the related work piece. All unit generally use a…
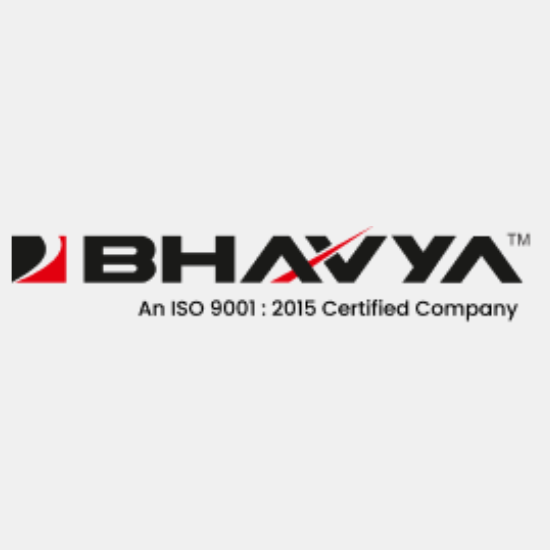
Why Quality Workshop Machinery is Very Important?
The research and development activities have resulted in manufacturing a variety of new products including several types of workshop machinery. In fact equipment play an important role everywhere and affect almost every person, in any part of the world. Today…
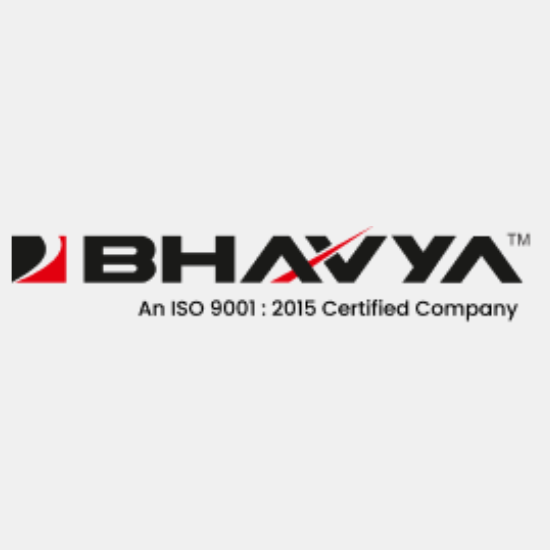
Selecting Right Type of Press Brake for Your Workshop
A press brake is also referred to as a brake press. It is basically a powerful machine tool that is commonly used for bending sheets and plates; particularly for bending sheet metal. It forms preset bends by holding the work piece in between the suitable punch…