Category Archives: Surface Grinding Machine
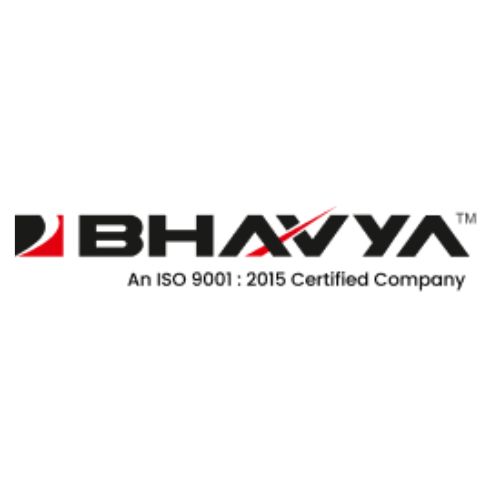
Surface Grinding Machines: Precision and Efficiency in Machining
Introduction Surface grinding machines are indispensable tools used for achieving precise and smooth surfaces. With the ability to remove any surface irregularities, they play a vital role in various industries, including automotive, aerospace, metalworking, and construction. The surface grinder works…
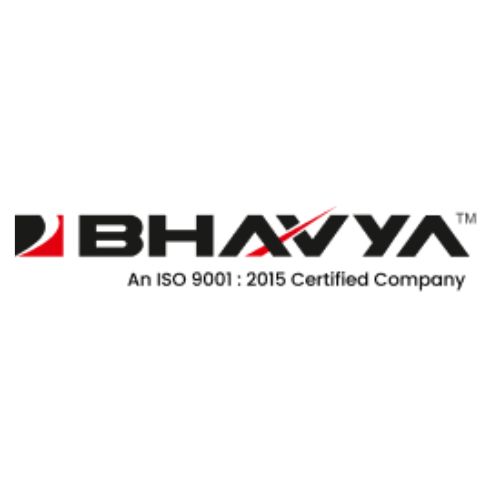
The Surface Grinding Machine Market in Bahrain
Currently, the surface grinding machine market in Bahrain is experiencing a high level of growth due to the increase in demand for grinding machines in the automotive industry. This is because automotive manufacturers are looking to improve production processes and…
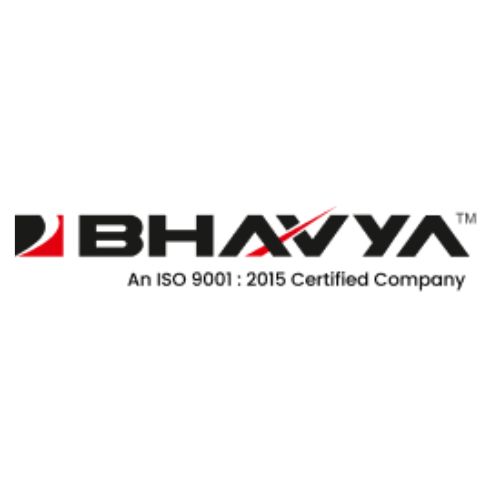
Surface Grinding Machine Demand and Supply in Oman Market
Considering the growing demand for surface grinding machines in the Oman market, the companies are offering a wide range of machines that can cater to the need of various industries. These machines include CNC grinding machines, which have a major…
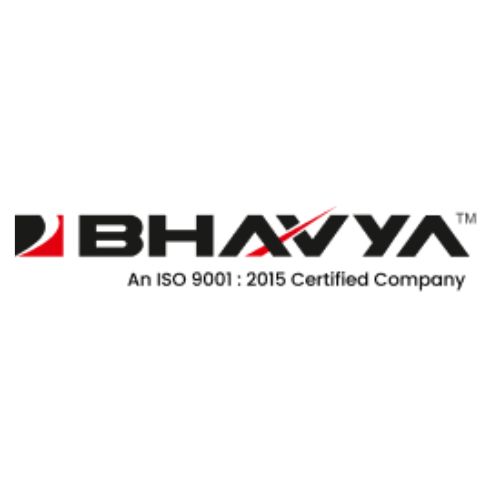
Surface Grinding Machine Demand and Supply in Qatar
Various industries in Qatar are in need of surface grinding machines. They need them to manufacture parts that are more accurate and precise. These machines are used in several industries, such as construction, automotive, manufacturing and engineering. Which Surface Grinding…
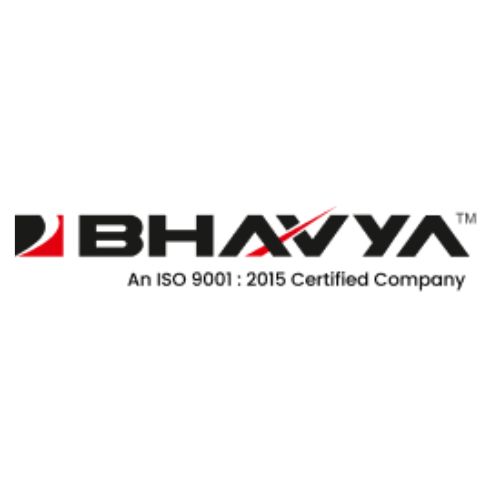
Pros and Cons of Welding and Drilling Machine Carts
A surface grinder is an excellent tool for diminishing hardened bent shafting on a metal surface. The material used for surface grinding, which is generally 0.25 - 0.5 mm, is well suited for rough cutting. However, the surface grinder can…
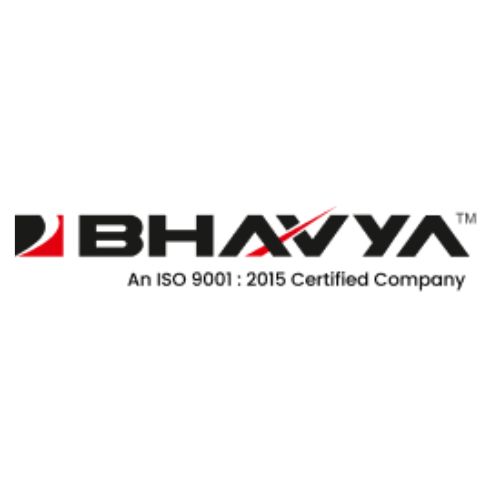
Learn about the Multipurpose Machining Advantages with Grinding Equipment
As far as the concept of grinding in machining industry is concerned, it refers to the milling device. It is applied to design wood, metal and many solid work piece materials. In most of the industries milling machines are identified…
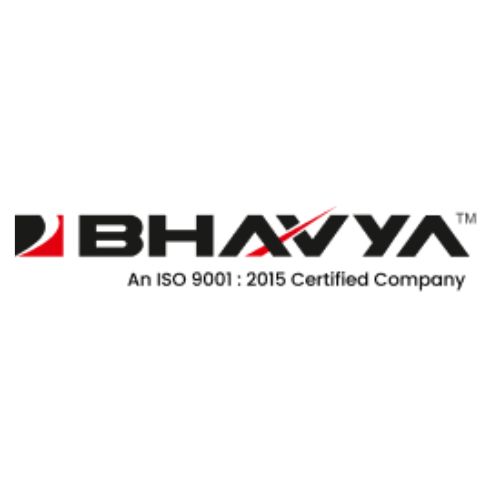
Facts About a Surface Grinding Machine
To give a meticulous smooth finish to the surface, as regards the level, size or finish of the surface of a flat metallic or non-metallic object, surface grinding tools are used. In order to make the surface flat and smooth…