Monthly Archives: November 2022
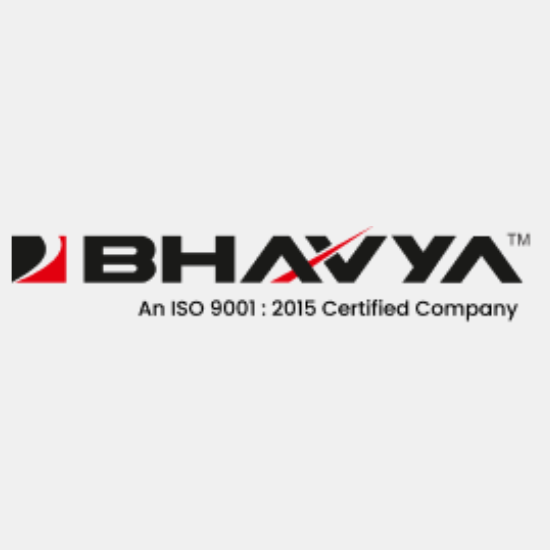
Different Types of Milling Machine and their Market in Kuwait
Bhavya Machine Tools are one of the best milling machine manufacturers for the Kuwait market, and we offer several types of milling machines, such as the horizontal milling machine, vertical milling machine, and CNC milling machine. Bhavya Machine Tools being…
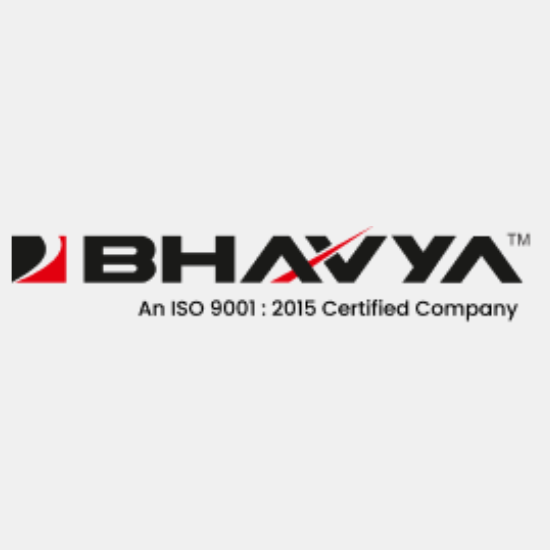
How to Choose Milling Machine in Bahrain?
We, at Bhavya Machine Tools one of the leading suppliers of milling machine to Bahrain, and other countries knows understand the need of choosing the right milling machine for your work is a key decision. The speed at which a…
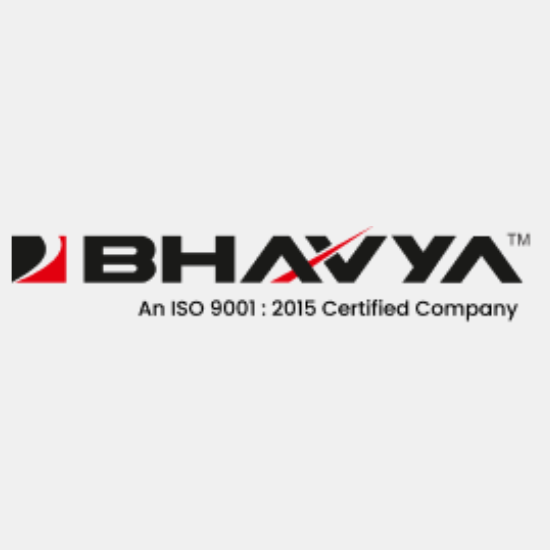
The Machine Tools Industry in Bahrain
Currently, the Machine Tools industry in Bahrain is dominated by the Automotive segment and the Metal cutting segment. According to the reliable sources, the Metal cutting segment is expected to grow at the highest CAGR during the forecast period. The…
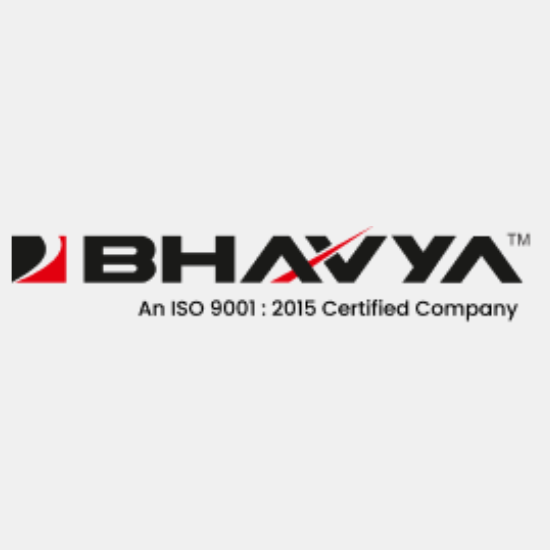
Milling Machine Demand and Supply in Oman Market
The demand for Milling Machines has increased in Oman. The Milling Machines are used in various industrial sectors such as Automobile, Construction, Aerospace, and Defense. The demand for Vertical and Horizontal Milling Machines has increased significantly. Demand of Milling Machine…
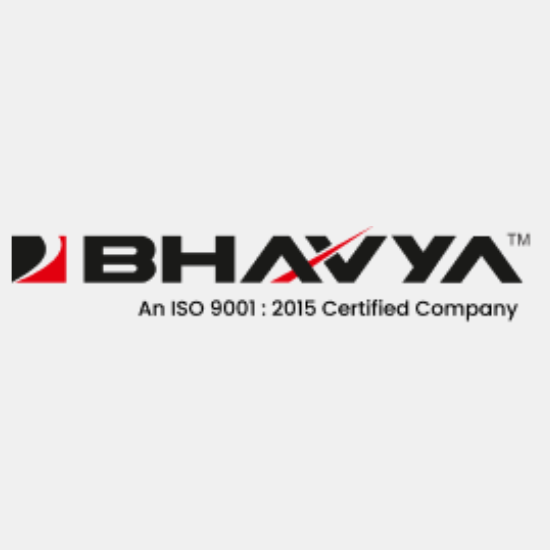
Radial Drilling Machine for Bahrain – Different Application, and Benefits
Despite the fact that the radial drilling machine market in Bahrain is quite small, it has a high potential of growing into a significant market. This market is driven by the increase in construction activities in the country. In addition,…
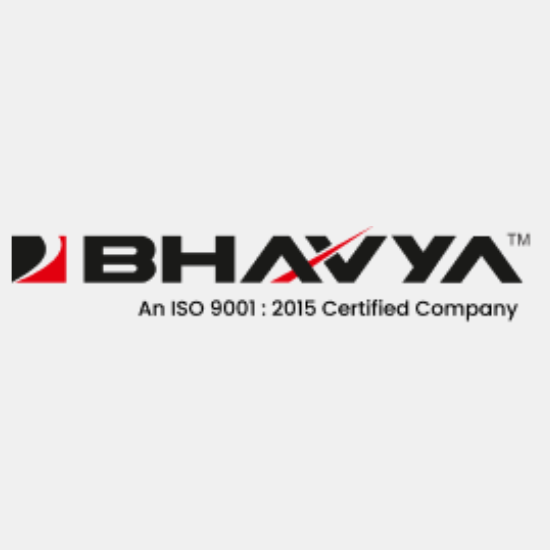
Buying Lathe Machines in Oman
Bhavya Machine Tools is lathe machine supplier to Oman, offers best lathe machine of different types and configurations to its wide customer base all over the world. So, whether you are planning to buy a lathe or are merely thinking…
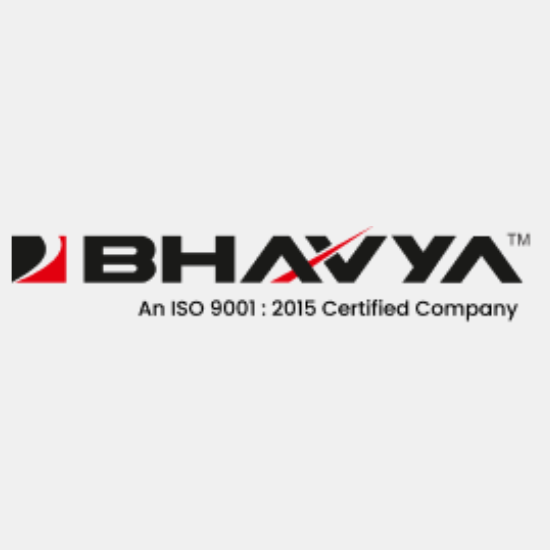
Radial Drill Machine Market in Qatar – What you Need to Know?
Among the most widely used drilling machines is the radial drill. This type of drilling machine is primarily used in oil and gas drilling. However, this machine is also used in drilling other materials such as concrete, stone, and metal.…
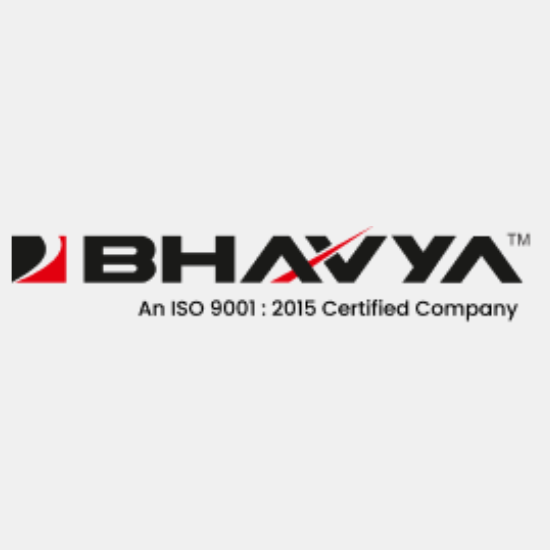
Lathe Machine and Machine Tools Market in Kuwait
During the past five years, the Lathe Machine and Machine Tools market in Kuwait has witnessed a remarkable growth rate. The growth rate of the market is attributed to the growth of the construction and automotive industries. This market has…
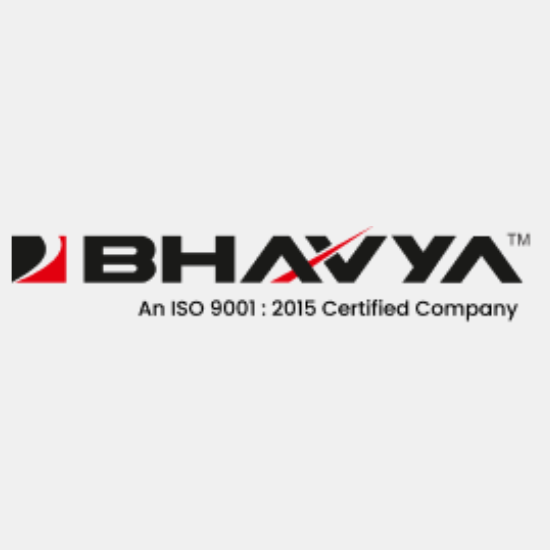
Lathe Machine Market in Bahrain – An Overview
Currently, the Lathe Machine market in Bahrain is experiencing a good growth. This is due to a number of factors, including the increasing demand for machine tools, as well as the growing population of industrial users and the growing construction…
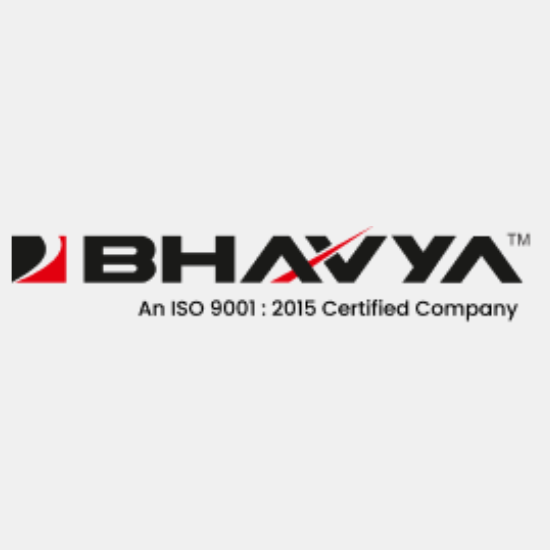
Lathe Machine Demand and Supply in Qatar
Various factors have affected the demand and supply of lathe machines in Qatar. These factors include recent innovations and major events. In addition, there has been regional segmentation. Horizontal Lathe Global Market Currently, the global Horizontal Lathes market is largely…
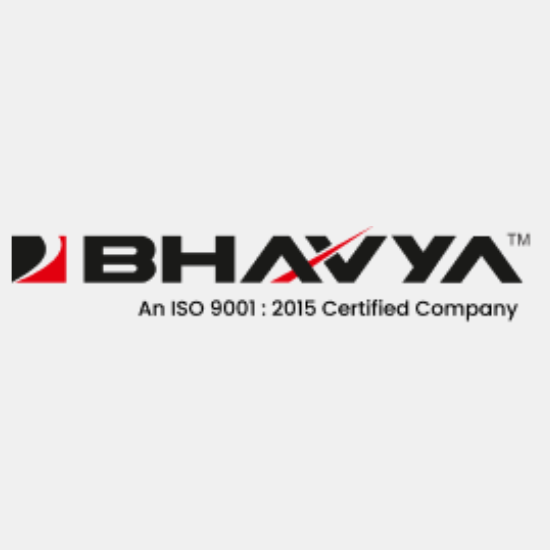
Know about Milling Machine Market in Bahrain
During the last few years, the milling machine market in Bahrain has witnessed an increase in demand for the machines. This is primarily due to the increasing demand for the machines from the construction industry. However, there are other factors…
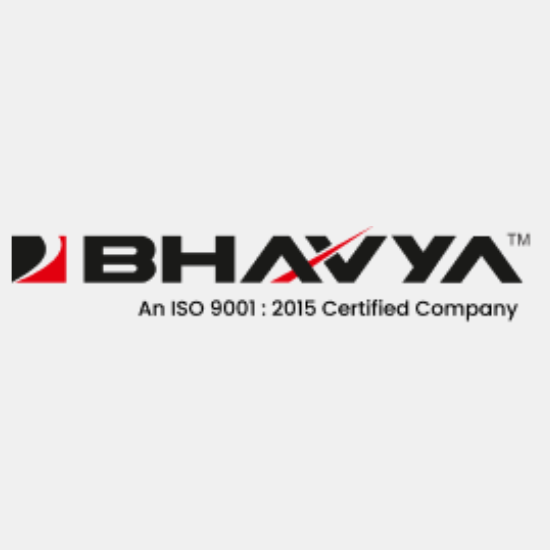
Purchasing a Pipe Bending Machine
There are a number of factors to consider when purchasing a Steel Pipe Bending Machine. Specifically, its output capacity, or the number of parts per hour produced, is of critical importance. This will vary depending on the type of tube,…
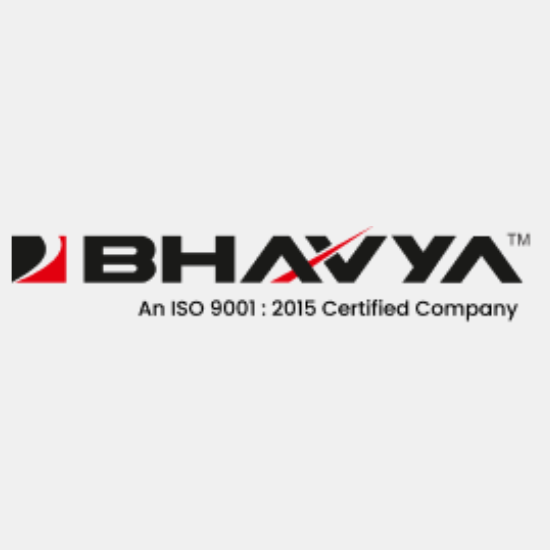
What to Look for in a CNC Bending Machine?
CNC Bending Machines are a great way to create a variety of products. They can be very simple to use and are very fast and accurate. They are also extremely versatile, meaning you can use them for a variety of…
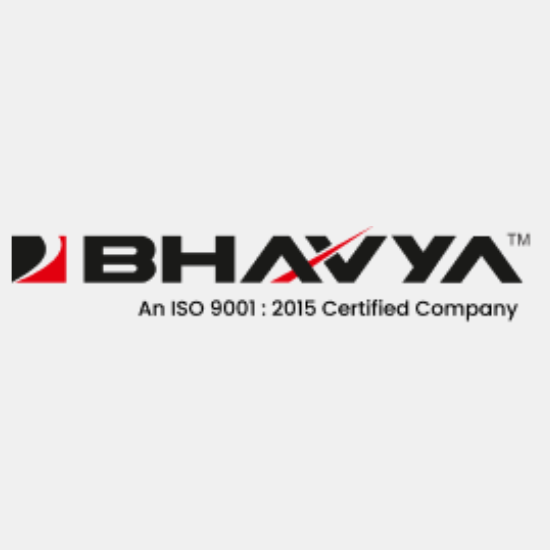
Different Power Press Machine Tools
Power presses are a common type of machine tools. They can be a great benefit in many different industries, including metalworking and woodworking. Safety is an important concern when operating these machines. A good way to protect your staff is…
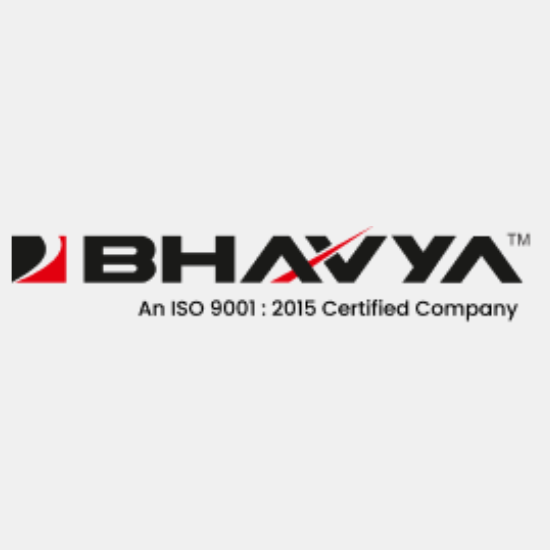
Saves Money, Time, and Materials with Flexible Arm Tapping Machine
Flexible Arm Tapping Machine is a tool that is used for making thread holes on a surface. It has an articulated arm that is adjustable. The machine can drill holes in steel or aluminium. It can save time and material.…
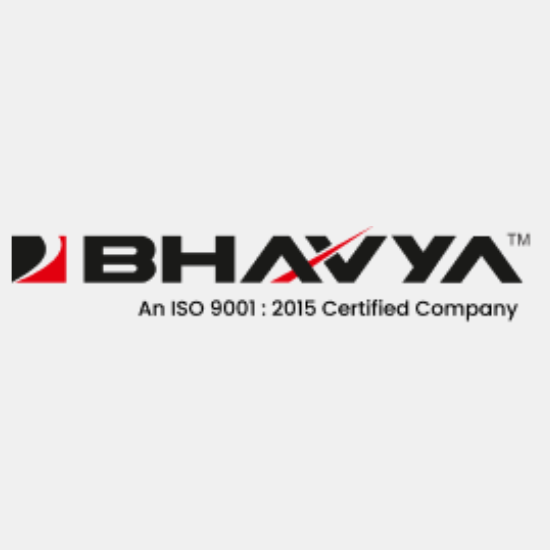
CNC Lathe Machine – Global Demand and Supply
The global CNC lathe machine market is highly fragmented with a large number of regional and local players. The key players in this market like Bhavya Machine Tools are continuously developing new products to meet the needs of the rapidly…
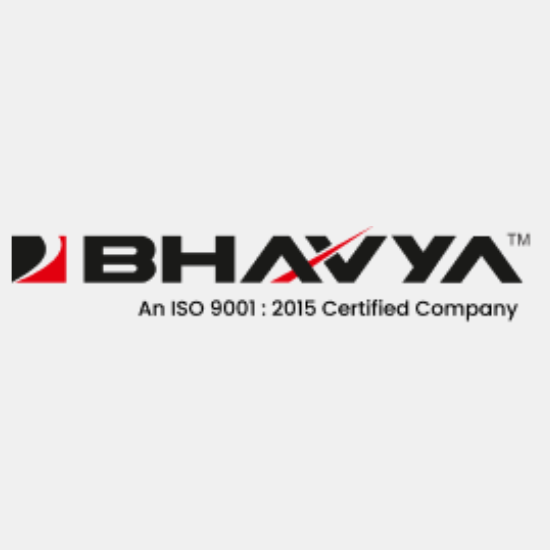
Fiber Laser Cutting Machine Global Demand and Supply
This article focuses on the high-power fiber laser and its applications in micro-cutting and thin-sheet applications. It also discusses the initial costs and operating costs of this machine. This article will help you to make an informed decision. We will…