Monthly Archives: December 2022
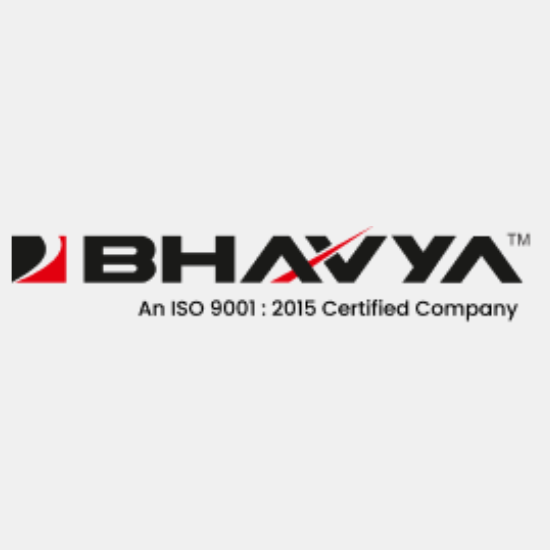
Press Brake Machine Market in United Arab Emirates
In this article, we will explore the Press Brake Machine Market in United Arab Emirates (UAE) and analyze the key market players, their key strategies, and future prospects. We will also explore the growth trends of the metal fabrication equipment…
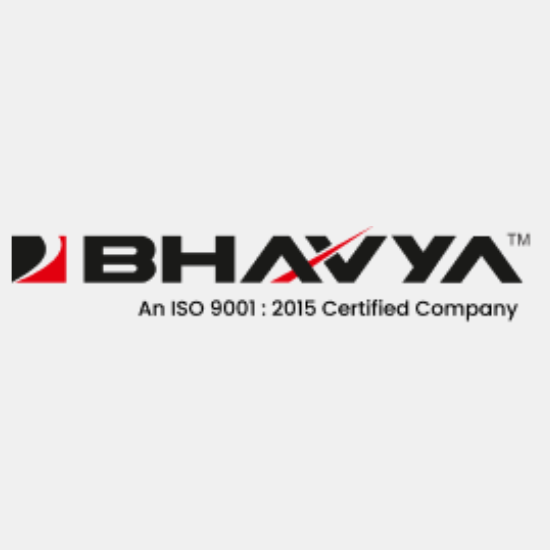
Shearing Machine Demand and Supply in United Arab Emirates Market
The demand for shearing machines is increasing in the United Arab Emirates market. As a result, more and more companies are investing in the sector. This is because the industry offers a wide variety of products that are manufactured using…
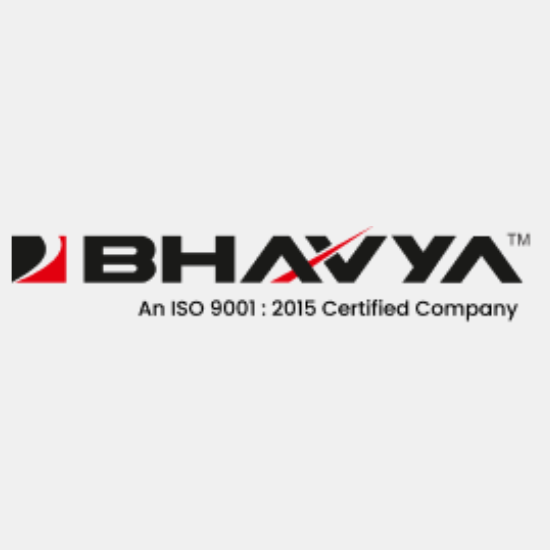
Lathe Machine Market in United Arab Emirates
If you are looking for information on the Lathe Machine Market in the United Arab Emirates, you are in the right place. This article will help you determine the market size and potential opportunities for CNC lathes in the UAE.…
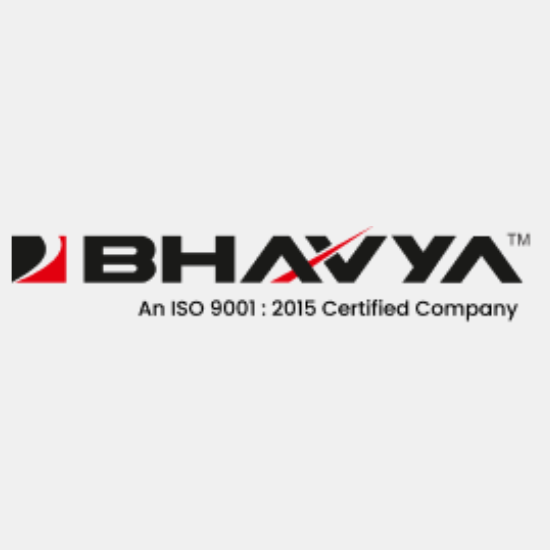
Radial Drilling Machine Demand and Supply in United Arab Emirates Market
The radia drilling machine demand and supply in United Arab Emirates market has been witnessing a rapid growth. This is attributed to the increased demand for the drilling machines in the construction sector. However, the increased manufacturing costs may hamper…
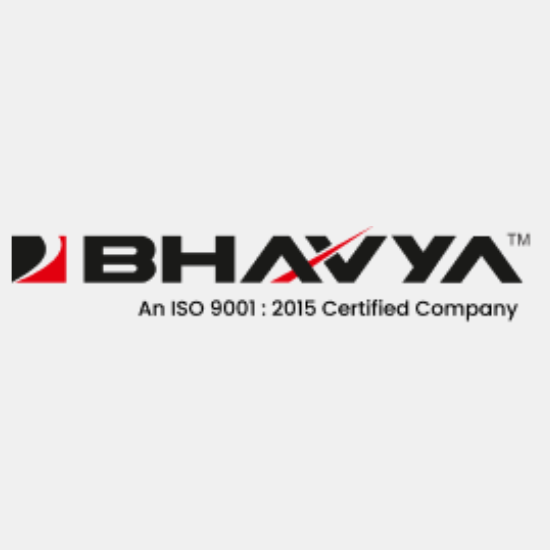
Milling Machine Tools Market in United Arab Emirates
The United Arab Emirates is a major market for the milling machine tools industry. This market is mainly fueled by the increased demand for automobile parts in the region, as well as the growing manufacturing sector in the region. The…
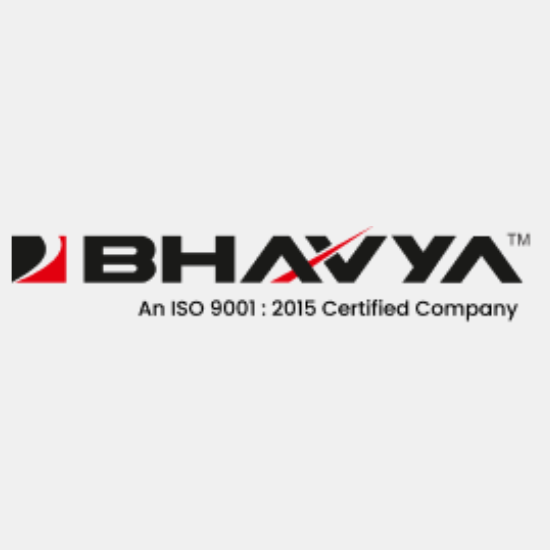
Shaping Machine Tools Demand and Supply in United Arab Emirates Market
There is a great demand for Machine Tools in the UAE market owing to the booming metal cutting segment and the increasing demand for machine mounts in various industrial sectors. Moreover, the growing popularity of additive manufacturing is also driving…
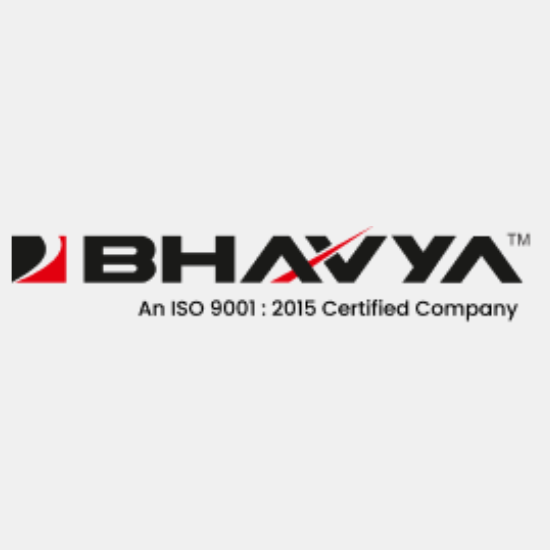
The Lathe Machine Industry in Dubai
In the Middle East and North Africa region, the lathe machine industry is booming. The demand for lathe machines is increasing as more and more companies in these regions need lathes to produce a wide variety of products. A job…
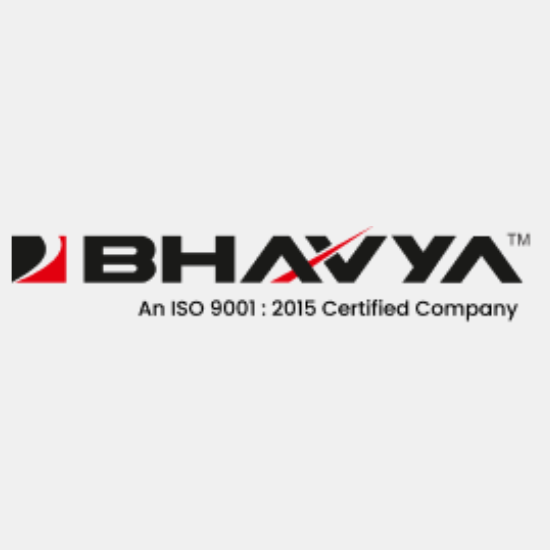
Shearing Machine Industry in Dubai
If you are in the market for a new shearing machine, you might want to take a look at the different types of machines available. These include block cutting machines, straight knife shearing machines, hand operated shearing machines, and more.…
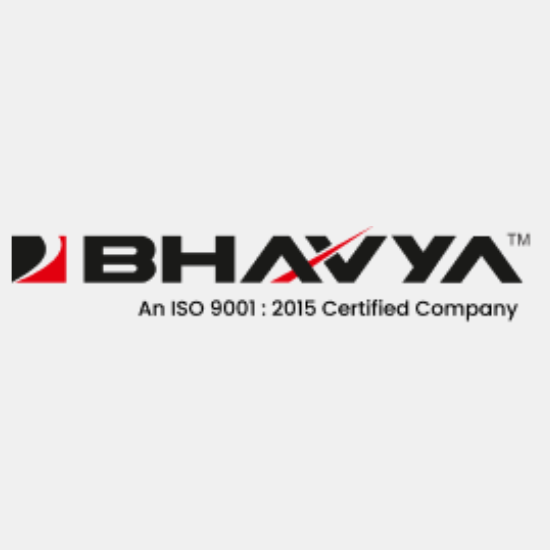
Press Brake Machine Industry in Dubai
A press brake machine is a type of mechanical device which helps to prevent a part from being bent, which means the machine can be used for pressing the end of a piece of material. There are several types of…
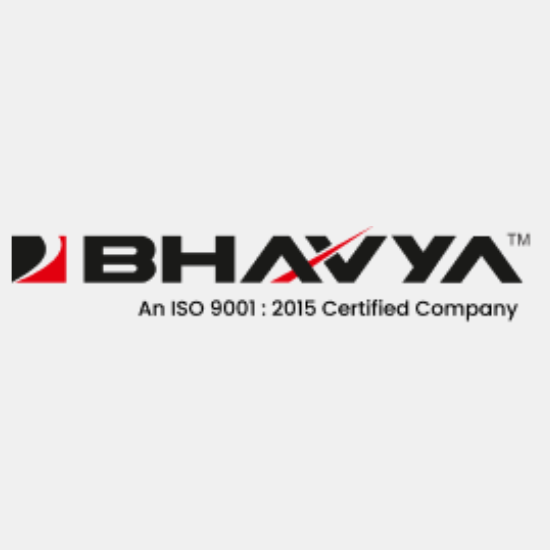
Radial Drill Machine Industry in Dubai
The radial drill machine industry in Dubai is booming in a big way. With increasing industrial output in the region, companies are investing in this equipment and a wide range of new products are being launched in the market. With…
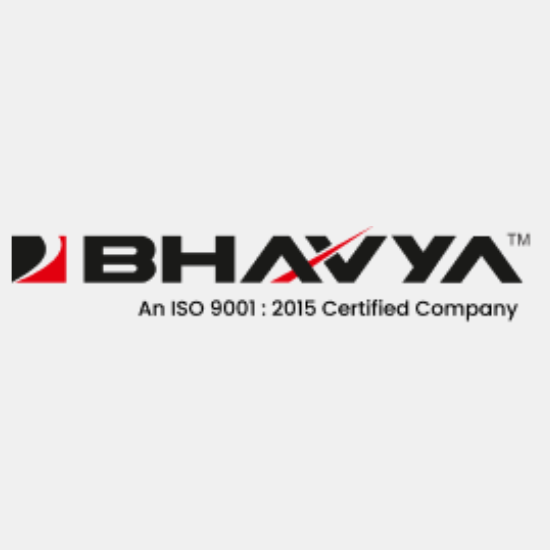
The Milling Machine Tools Industry in Dubai
The Milling Machine Tools Industry in Dubai is one of the most vibrant and growing industries in the Middle East. The industry's growth is fueled by an expanding manufacturing sector and the increasing demand for machinery. A variety of different…
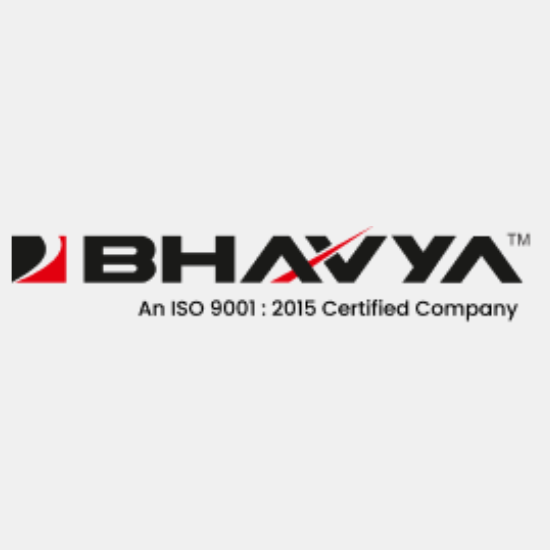
Shaping Machine Industry in Dubai
The shaping machine industry in Dubai is a booming industry that offers many opportunities for both employers and job seekers. The industry has been experiencing a renaissance in the last few years as more people have begun to realize the…
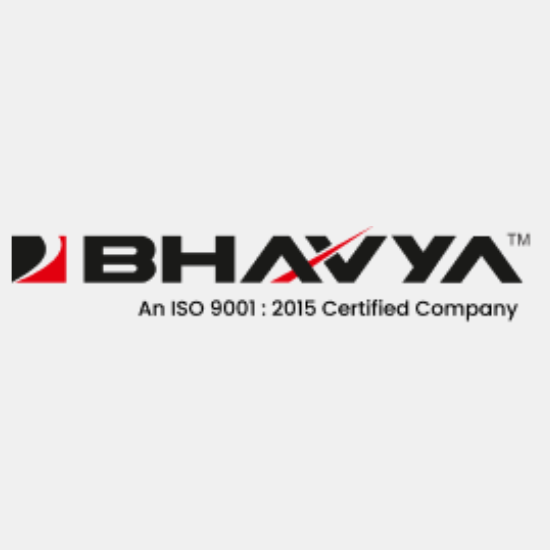
Radial Drilling Machine Market in Kuwait
Currently, the Radial Drilling Machine market in Kuwait is witnessing the growth in the construction industry. This growth has mainly been attributed to the increasing demand for the construction equipment in the country. As a result, the market is expected…
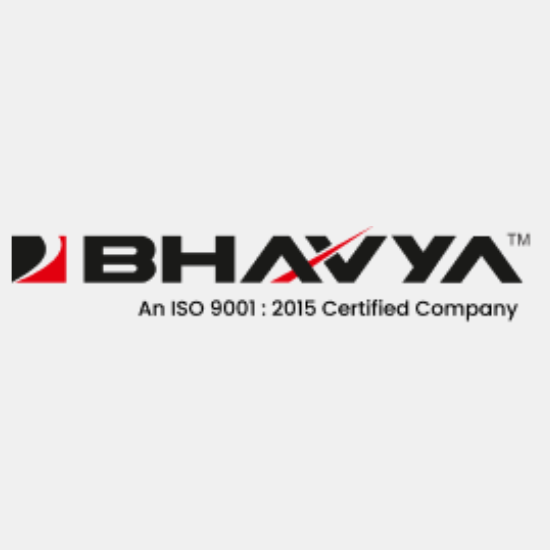
Surface Grinding Machine Market in Kuwait
Currently, the market for Surface Grinding Machine in Kuwait is undergoing rapid growth as non-residential buildings and other construction projects are booming in the country. This is because the demand for the surface grinders is rising owing to the increasing…
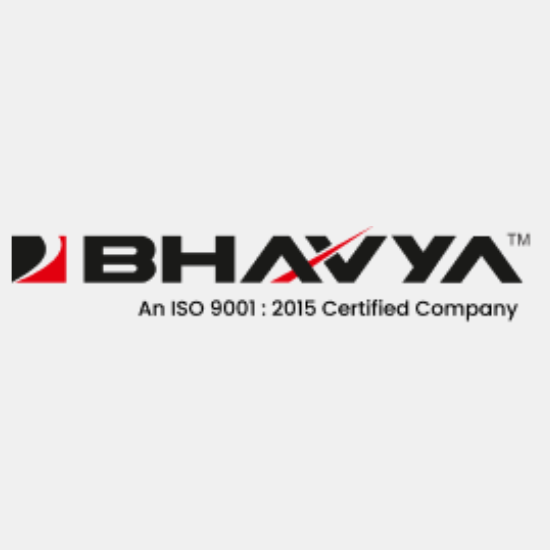
Different Types of Bandsaw Machine in India
Whether you're a seasoned woodworker or just starting out, choosing the right Bandsaw Machine in India for your woodworking needs can be a daunting task. But with a little research, you can rest assured you're buying the best tool for…