Monthly Archives: September 2021
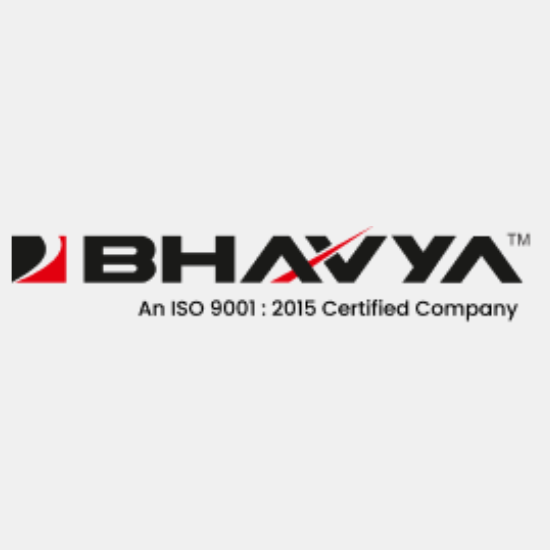
African Market for Lathe Machine
Lathe Machines are widely known as the "Mother of all machine tools". Their uses are spread over a wide range of Industries present all over the world. These applications are applied in almost every sector like food, mining, refineries, power…
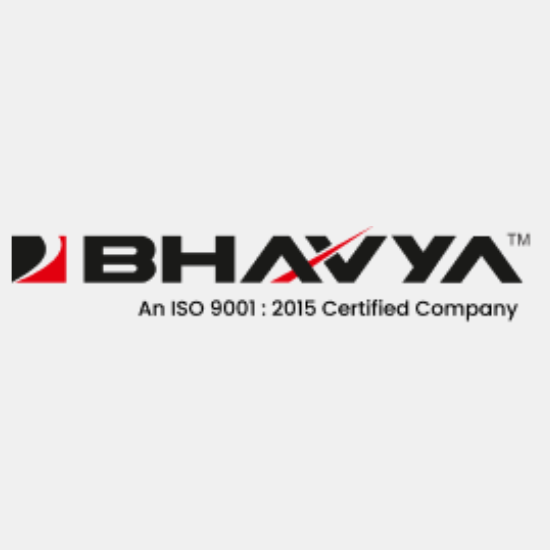
All About Threading Machine
Threading machines are tools that are used to cut and form threads, inside or outside a cone or a cylinder. Threading Machines are working towards the highest productivity and optimum performance even under the most extreme conditions, to provide the…
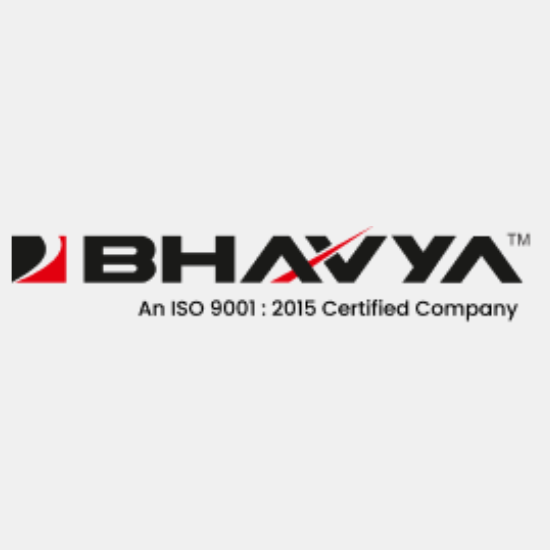
Why Precision Lathe Process is Important for Modern Industrial Needs?
The precision lathe machine is a machinery for precision operation, that is used to create an object by shaping, cutting, and removing its unwanted parts, from a block of material which can be either metal or wood. Purpose of Precision…
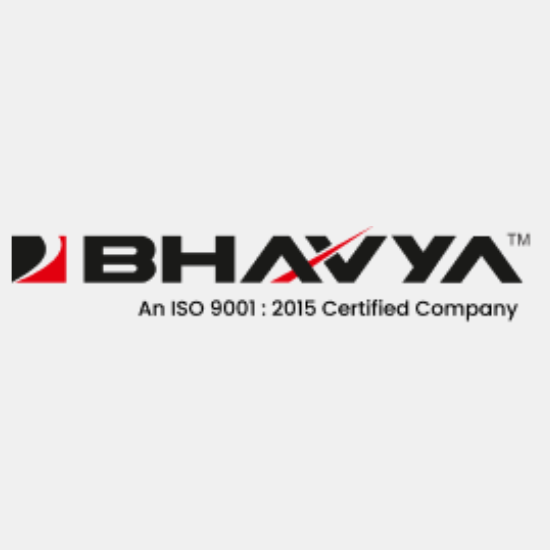
How to Use a Block Boring Machine?
Block boring machines, also called boring machines, are special machines that are used to make hollow metal cavities by compressing or expanding the metal into a specific shape. Block boring is used for many applications including cutting and forming. They…