Monthly Archives: July 2023
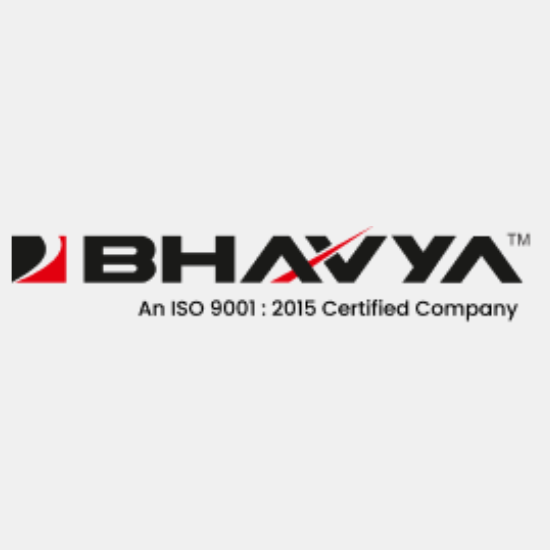
The Future of CNC Lathe Machines
In recent years, the manufacturing industry has witnessed significant advancements in technology, leading to increased efficiency and productivity. One such technological marvel that has transformed the manufacturing landscape is the Computer Numerical Control (CNC) lathe machine. With the ability to…
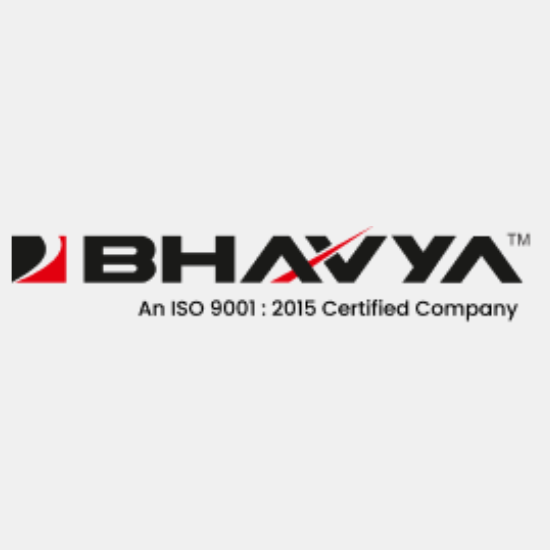
Power of Chamfering Machines in Manufacturing Industries
Chamfering machines are essential tools used in various industries for the purpose of creating bevelled edges or chamfers on work pieces. These machines play a crucial role in achieving precision and efficiency in the manufacturing process. Chamfering machines are specialized…
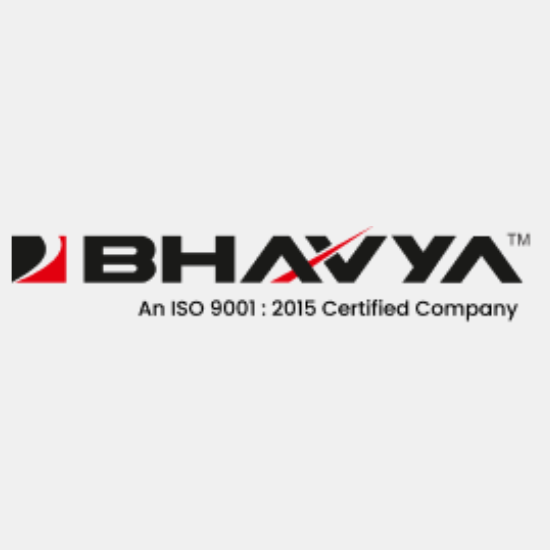
Maintaining and Troubleshooting Chamfering Machines
Chamfering machines are essential tools used in various industries for creating bevelled edges and chamfers on different materials such as metal, wood, and plastic. These machines provide precision and efficiency in shaping and finishing work pieces but like any mechanical…
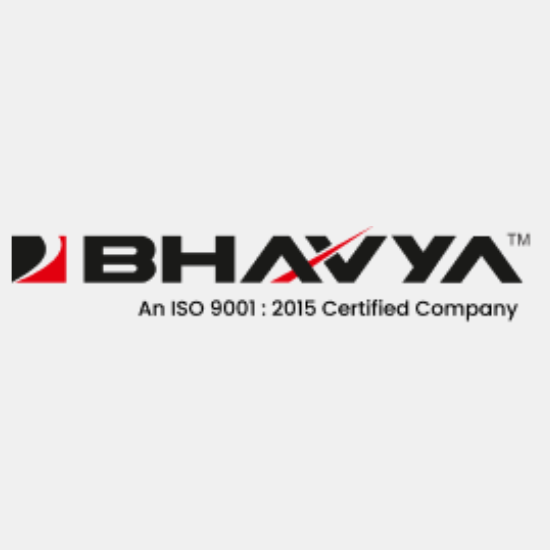
Applications of Chamfering Machines in Different Industries
Chamfering machines are versatile tools that are widely used in various industries for different applications. These machines are designed to create beveled edges, or chamfers, on a workpiece, providing a smooth and finished look. With their ability to perform precise…
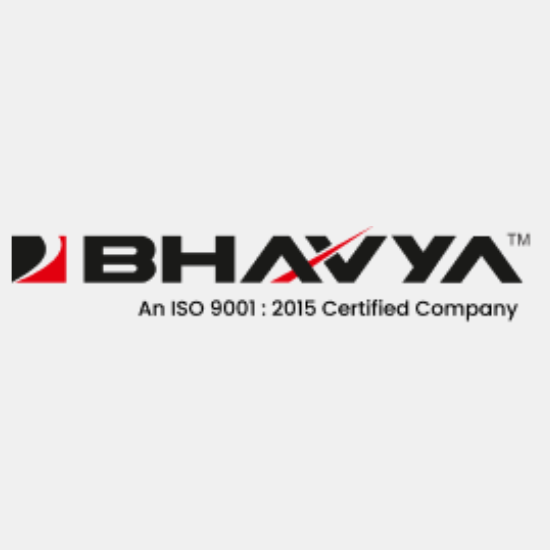
Future Trends in Chamfering Machine Technology
Chamfering machines have been an integral part of manufacturing processes for decades, providing precise and uniform beveling to different materials such as metal, wood, and plastic. However, with advancements in technology, chamfering machines are undergoing significant transformations, enabling manufacturers to…
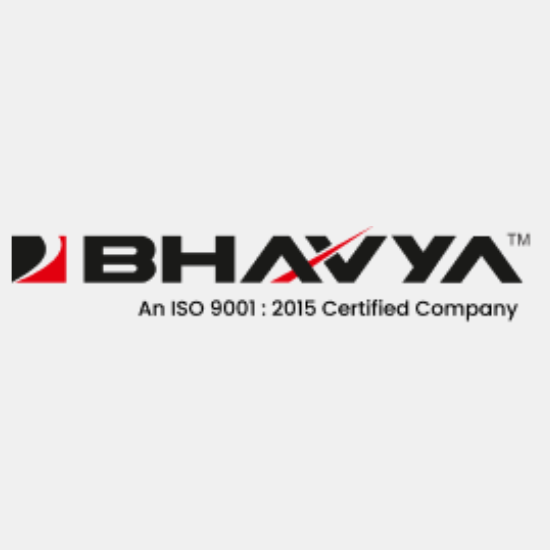
Universal Tool and Cutter Grinding Machine
The Universal Tool and Cutter Grinding Machine is a specialized piece of equipment designed for precision grinding and sharpening of cutting tools. It offers a wide range of capabilities, allowing manufacturers to produce tools with exceptional accuracy and consistency. This…
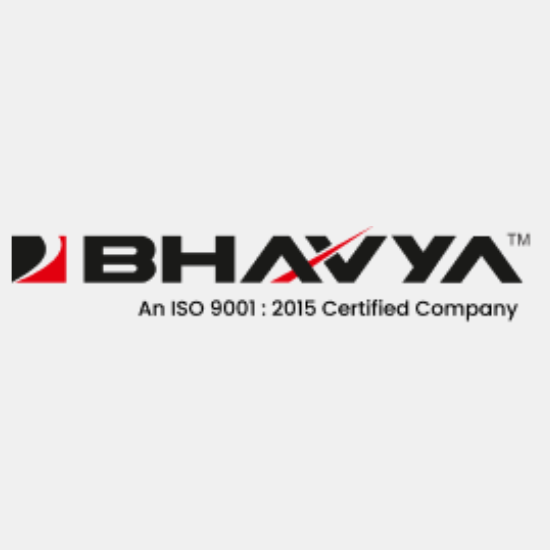
How Lathe Machines Revolutionize Manufacturing Processes?
Lathe machines are mechanical devices used to rotate a workpiece while various cutting tools are applied to shape, cut, or drill it. The workpiece is clamped securely and rotated on its axis, allowing the cutting tools to remove material and…
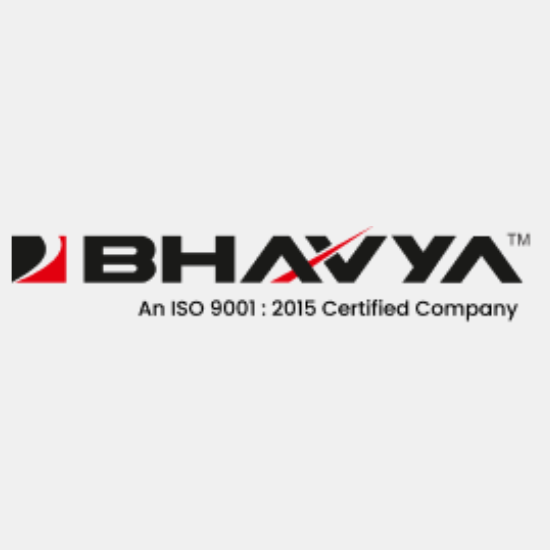
Lathe Machines – The Backbone of Machining Processess – The Backbone of Machining Processes
Lathe machines are mechanical tools used for shaping workpieces by rotating them against a cutting tool. They have been a fundamental part of machining processes for centuries and continue to be widely used in industries such as automotive, aerospace, and…