Category Archives: Bending Machine
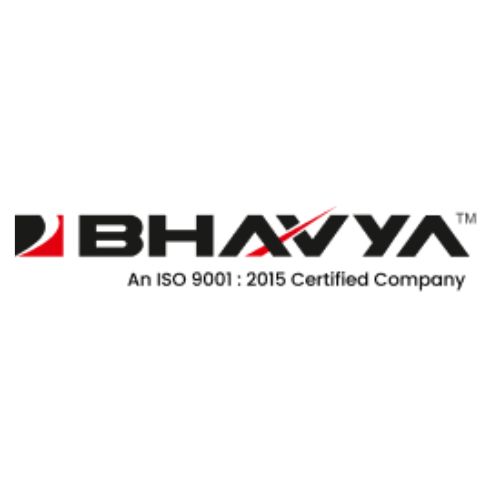
Purchasing a Pipe Bending Machine
There are a number of factors to consider when purchasing a Steel Pipe Bending Machine. Specifically, its output capacity, or the number of parts per hour produced, is of critical importance. This will vary depending on the type of tube,…
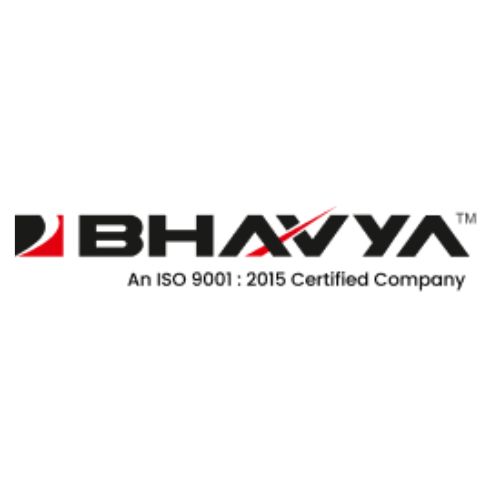
What to Look for in a CNC Bending Machine?
CNC Bending Machines are a great way to create a variety of products. They can be very simple to use and are very fast and accurate. They are also extremely versatile, meaning you can use them for a variety of…
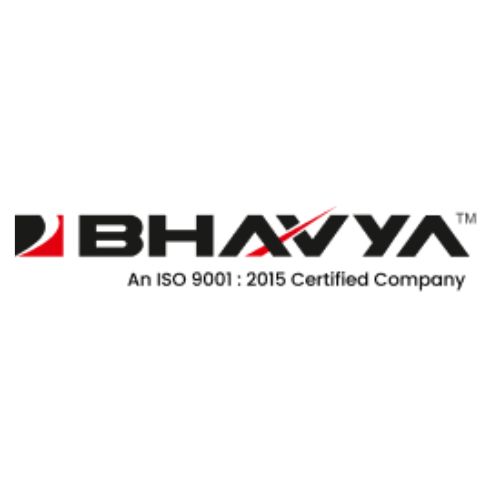
An Overview on Hydraulic Pipe Bending Machine, and Offset Bending Tool
In this article, we will look at the advantages and disadvantages of pipe bending machines. These machines are used to bend pipe and tubing into a variety of shapes. These machines are available in various sizes and can be used…
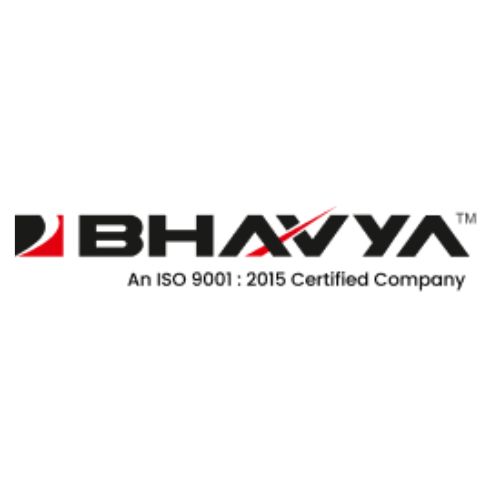
Benefits of a Hydraulic Busbar Bending Machine
In this article, we will talk about the benefits of a hydraulic busbar bending machine and its Edge bending mold. You will also learn how it works and how to choose a machine that will best suit your needs. After…
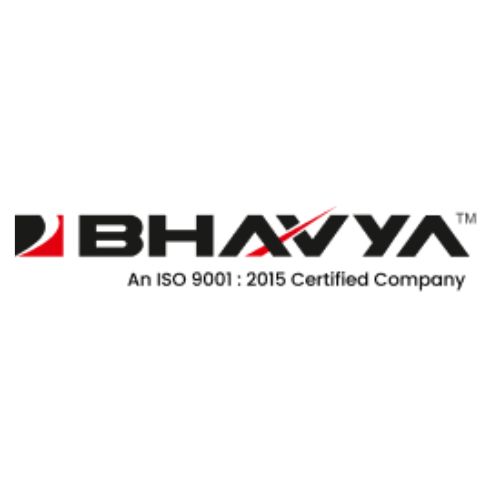
Features, & Functions of NC Bending Machines
When selecting an NC bending machine, you will want to consider the price, specifications, features and functionality of each one. In this article, we'll look at what to look for, as well as the pros and cons of each machine.…
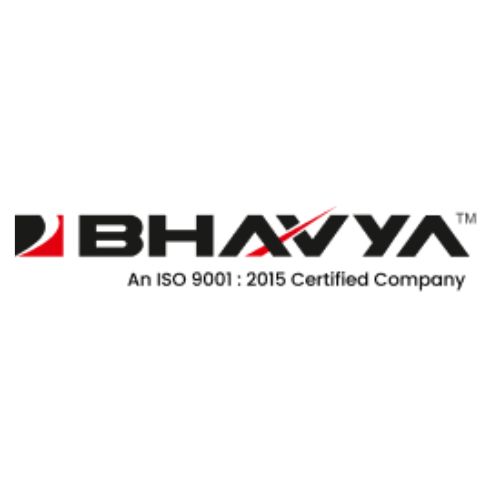
Different Types of Bending Machine & CNC Bending Machines
As the CNC bending machine becomes more popular, it plays a vital role in various industries. Compared with traditional bending machines, CNC bending machines play a more important role in various fields. Mechanical Bending Machine A Mechanical bending machine bends…
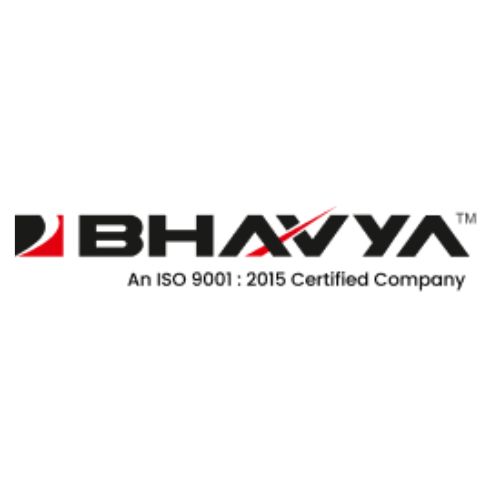
Purchasing a Pipe Bending Machine
Purchasing a Pipe Bending machine is an essential part of installing piping in the home. The right pipe bender can ensure a perfect fitting of your pipes. There are several factors to consider when purchasing a pipe bending machine. The…
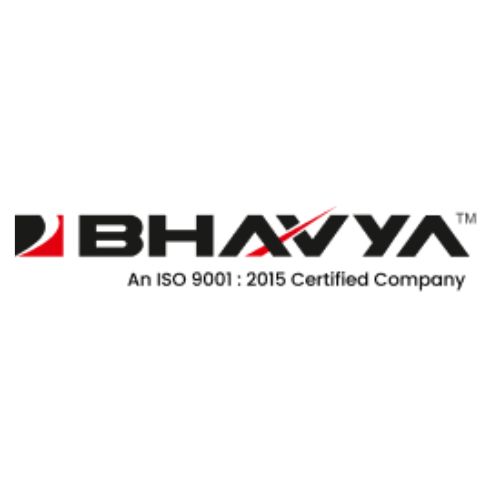
Choosing a Sheet Metal Bending Machine
When choosing a sheet metal bending machine, it is important to choose the one that can handle the materials you plan to bend. Each type has specific requirements for the materials that can be bent. The inner radius of the…
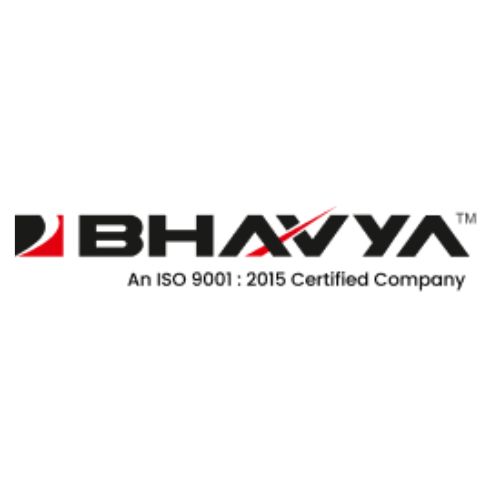
The Applications and Benefits of Using the Hydraulic Pipe Bending Machine
Pipe bending machines are utilized to bend pipes and tubes to create curved formed sections. This machinery is useful for many applications, such as pipe sealing, pipe bending, pipe assembly, and pipe breaking. Tubular pipes are generally made of bent…
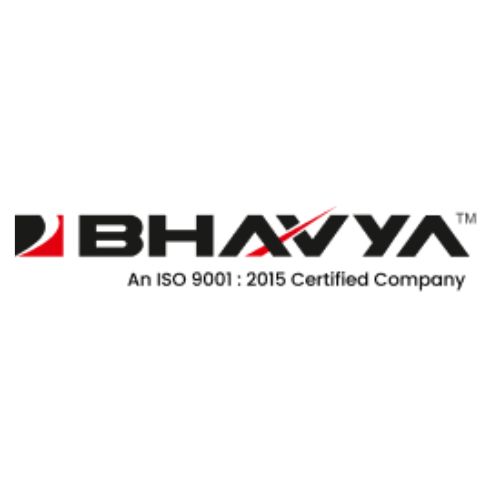
Understanding the Different Profile Bending Machines
A profile bending machine is also known as a primarily hand-held machine that is specifically utilized to form a nice bend on any working part. The machine is mainly utilized to execute the mechanical procedure required for proper bending of…
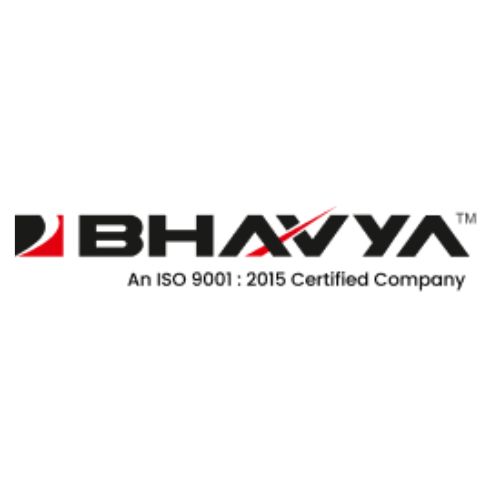
Bending machine – Application and Benefits
Bending machine - Application and Benefits A Bending machine is essentially a forming machine tool with the main purpose being to assemble a bend on a workpiece. It makes use of a linear and rotating move to manufacture a bend.…
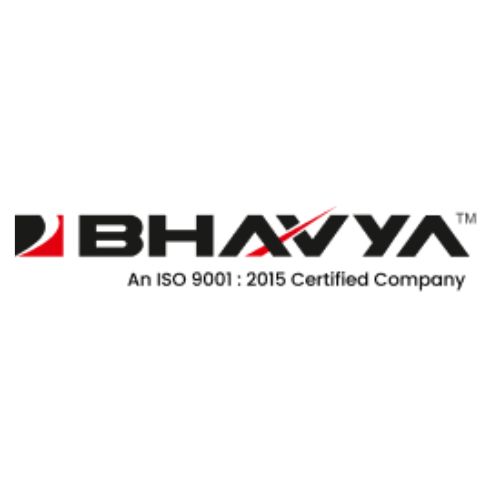
Working of Busbar Bending-Cutting-Punching Machine
A busbar is a metallic strip or bar that is used in electric power distribution. It is employed for local high current power distribution and is fitted inside the switchgear, panel boards, and busway enclosures. They are generally kept uninsulated…