Category Archives: Hydraulic Surface Grinder
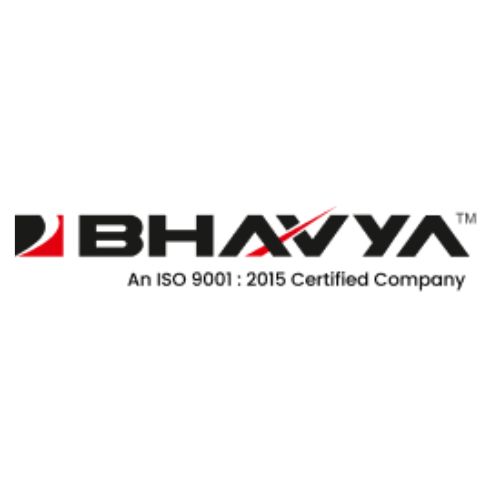
Tips For Selecting the Right Centerless Grinder
A centerless grinder is a precision machine that produces a wide variety of parts, with superior accuracy and ease of operation. The ability to hold extremely close tolerances is a distinct advantage of this technology. Compared to conventional grinding machines,…
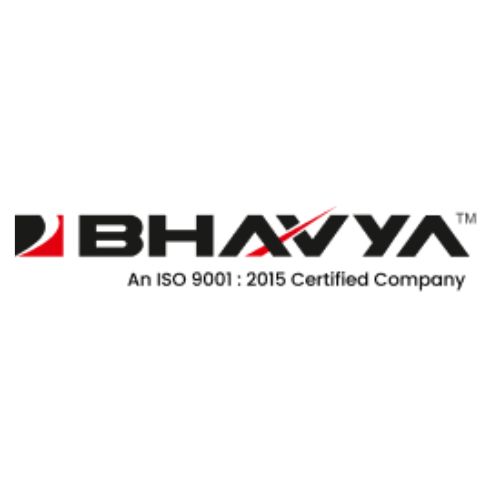
All About Hydraulic Surface Grinder
A surface grinder as the name suggests is meant for grinding operations. This is one of the most common machines for grinding operations. The main purpose is to ensure a smooth finish on a flat surface. There are a several…