Category Archives: Light Duty Lathe Machine
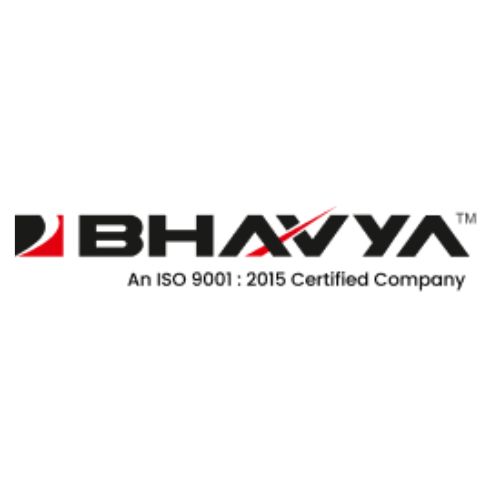
The Rising Demand for Lathe Machines in Bangladesh’s Construction and Infrastructure Sector
Bangladesh is undergoing rapid industrial and infrastructural growth. From bridges to high-rise buildings, the country is investing heavily in development. Lathe machines play a key role in shaping and machining metal parts for these projects. Cities like Bogra, Jessore, Tangail and…
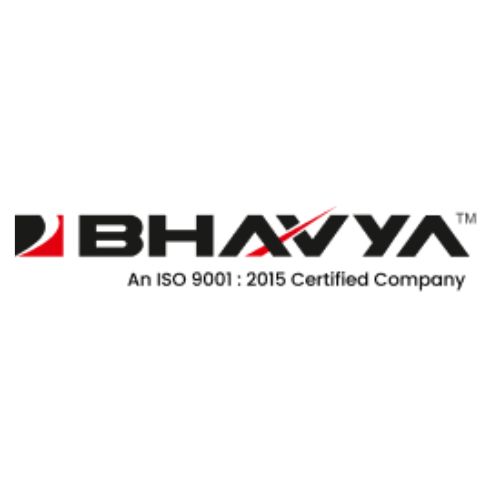
The Role of Lathe Machines in Iran’s Growing Aerospace Industry
Iran’s aerospace industry is undergoing rapid transformation, with increasing investments in aircraft production, space exploration and defense aviation. As the country strengthens its domestic aerospace capabilities, Lathe Machines in Nigeria, including Universal All Geared Lathe Machines, are playing a vital role…
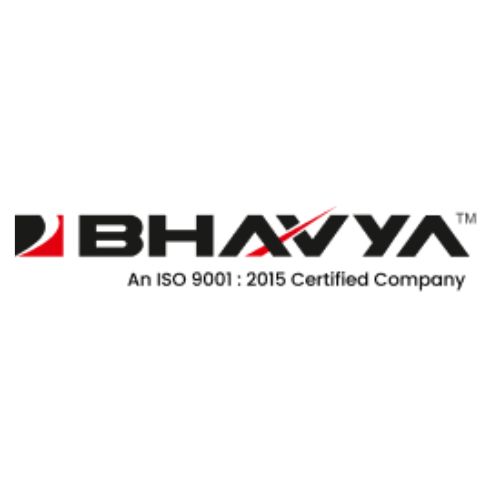
How Lathe Machines are Supporting Ethiopia’s Road Construction and Infrastructure Projects?
Lathe machines play a key role in Ethiopia’s infrastructure development. From shaping metal components for bridges to fabricating precision parts for road construction, these machines are essential in manufacturing durable and efficient construction materials. Cities like Asella, Nekemte, Woldia, Gambela,…
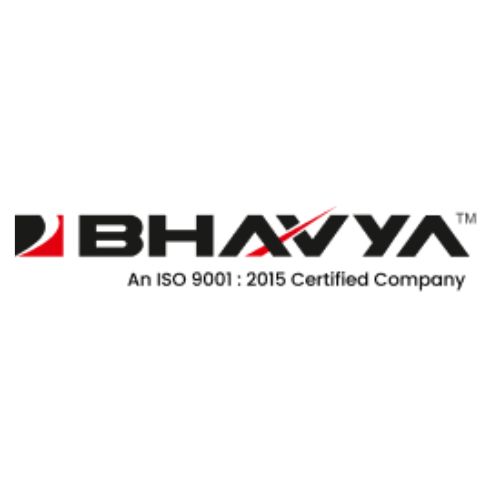
Top Nigerian Industries Adopting Lathe Machines for Advanced Manufacturing
Nigeria’s manufacturing sector is undergoing a significant transformation, with industries rapidly adopting lathe machines to enhance production efficiency and precision. In cities like Lagos, Abuja, Kano, Port Harcourt, Ibadan and Benin City, various industries are integrating CNC lathe machines, capstan lathe…
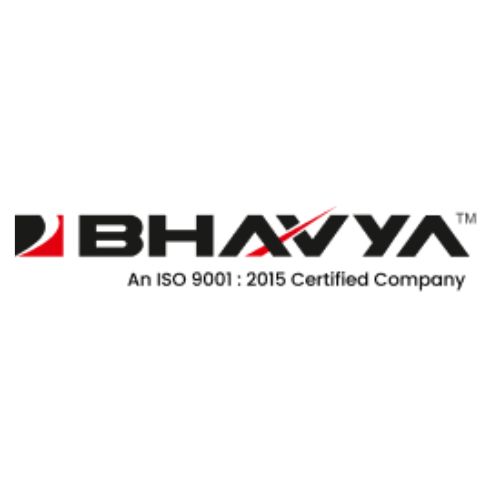
Light Duty All Geared Lathe Machine: Precision Engineering for Light Materials
Introduction Light-duty all geared lathe machines are an essential tool for industries that require precision machining of light materials such as metal sheets, wood sheets, and other lightweight workpieces. Bhavya Machine Tools offers a versatile and reliable light-duty all geared…
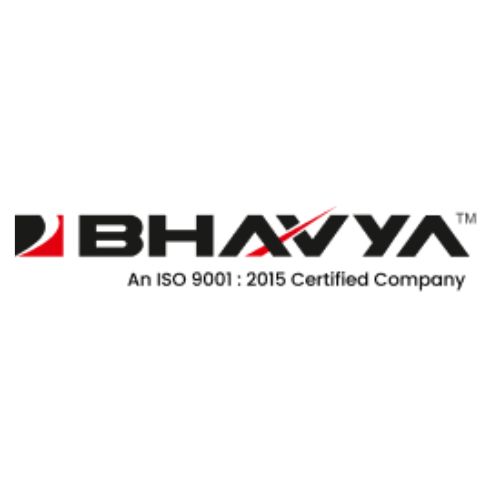
Produce Top Quality Rings and Other Jewelry Using Light duty Lathes
Introduction Jewels have been used from time memorial for beautification and as precious gifts passed from one person to another. They are common among celebrities, famous people and even the ordinary folks as they bring a sense of class, elegance,…
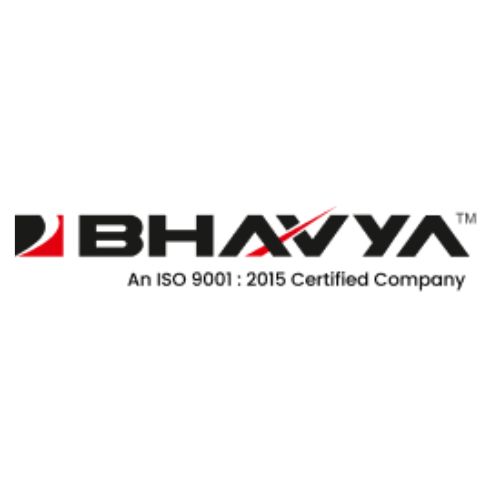
How Glass Work Pieces are transformed into Employable Materials with Lathe?
Features of Lather which make us Wonder A lathe apparatus is a workshop friendly device with which a range of machining processes can be done such as cutting, drilling, turning, deformation, etc This device can be purchase based on the…
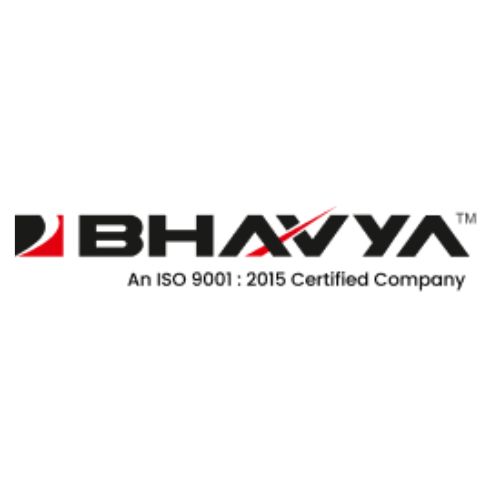
Lathe Machine Operations
Nowadays, the tool room work and workshop machine activities; are done by repairers or through suitable lathe tools. A lathe is a tool utilized to perform various functions like turning, cutting, drilling, grooving, knurling, parting, threading etc. They are used to produce accurate products made from…
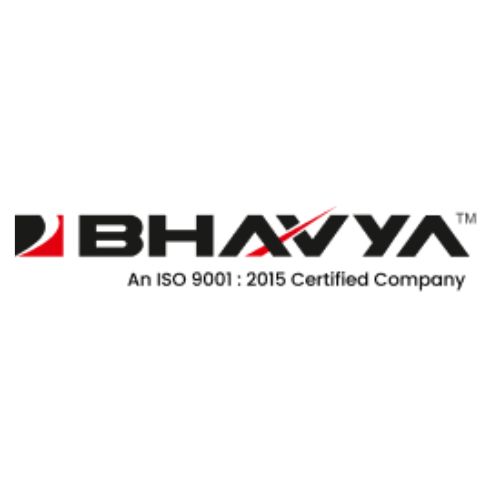
Lathe Machines – How They Make a Real Difference in Shaping Industries
The lathe is indeed a great invention and a very helpful machine, used for numerous purposes since the ancient times. The earliest type of lathe was the potter’s wheel, which is being utilized to shape clay pots and earthen objects…