Monthly Archives: May 2012
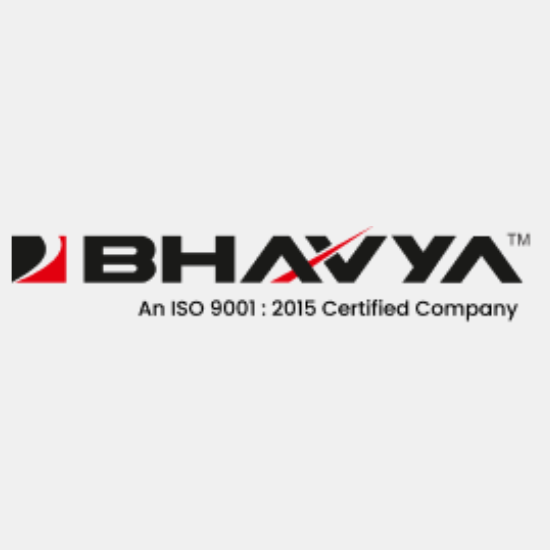
History of Milling Machine
Rotary filling was the first in base of invention of the first milling machine that reduced the efforts need to put on hand filling and save the time. The development history is still unclear as the variety of custom machines…
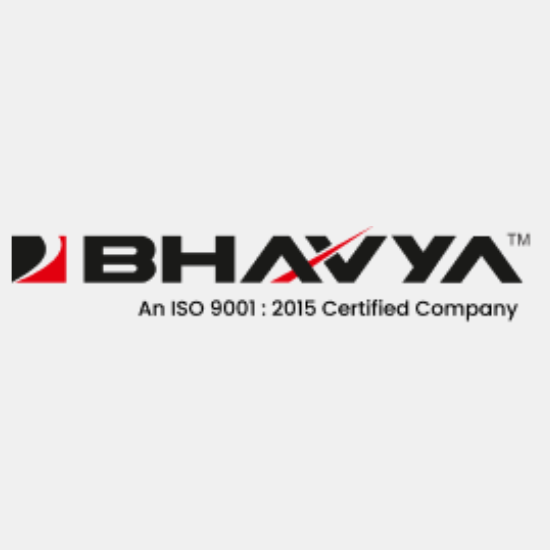
All About Slotting Machine
A slotting machine is a machine which is used to slot materials made of metal and wood. It can make slots on heads of screws, bolts and other automobile components as well as other similar parts. The main purpose of…
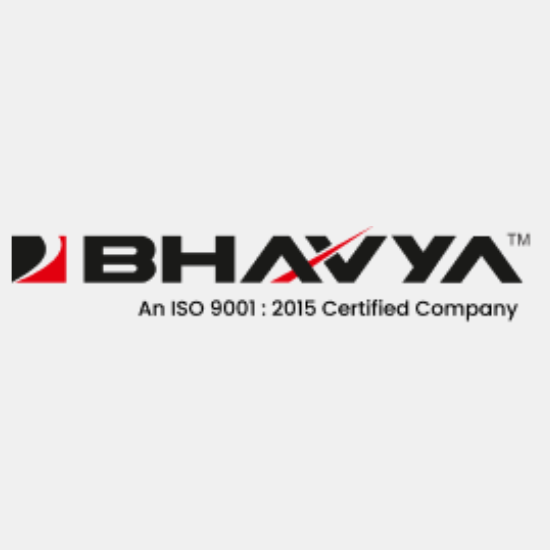
How to Install a Milling Machine?
A milling machine is a workshop tool used to shape solid materials like metal, wood, plastics etc. It is different than a lathe machine because in a lathe machine the material to be cut moves, whereas in the milling machine,…
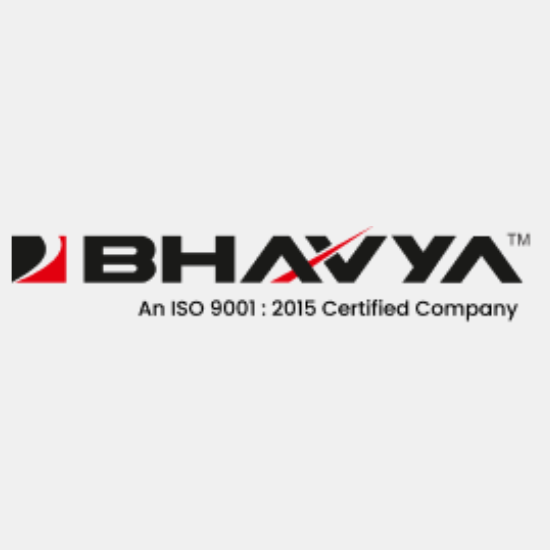
Types of Lathe Machines
A lathe machine is an important machine tool in a workshop as it is basically used to shape the metal articles. Initially the basic operation was to cut cylindrical metal stock which was then further developed to produce screw threads,…
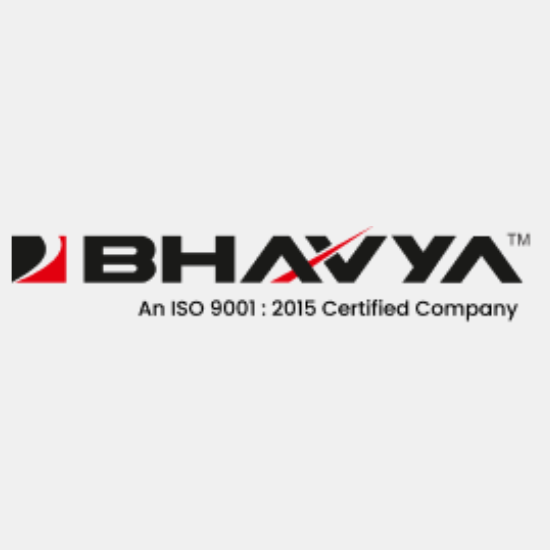
How to Use Lathe Machine?
Basically, a lathe machine is a tool used to shape metals.The material is rotated in the cylindrical motion and then touches a cutting tool to it which cuts the material. The metal sheet is fixed on the chuck of the…
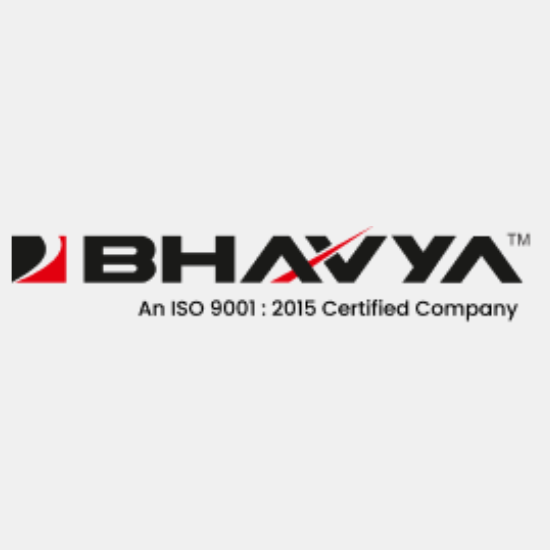
What is Press Brake?
Press brake is an important tool which is widely used in cutting metals in various shapes and sizes. It helps in forming predetermined bends in metal sheets by clamping the material between matching punch and a die. Thus, it uses…
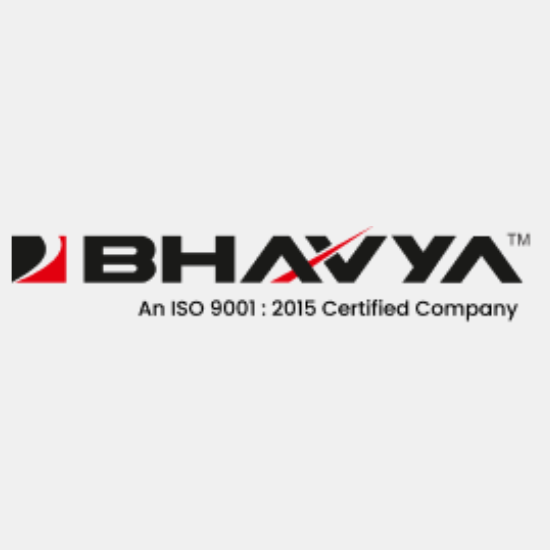
Machine Tools – Grinding Machine
Machine tools are used for various processing work on different metals. Machining works like cutting, grinding, shaping machine to shape the metal workpiece, boring, slotting on metal through slotting machine, shearing and others are carried out by mechanical and electronic…