Category Archives: Sheet Metal Machinery
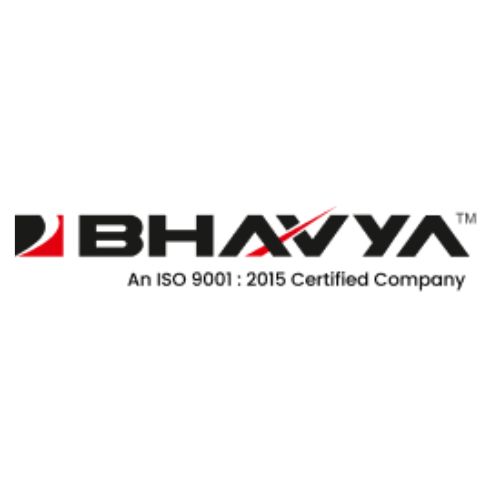
Application of Sheet Metal Machinery in the Aircraft Industry
In earlier times, the Wright brothers used 30-pound blocks of aluminum while making its engine. Aluminum has low density and high strength properties which makes it a very popular choice to make aircraft components. Sometimes aluminum alloys are also incorporated…
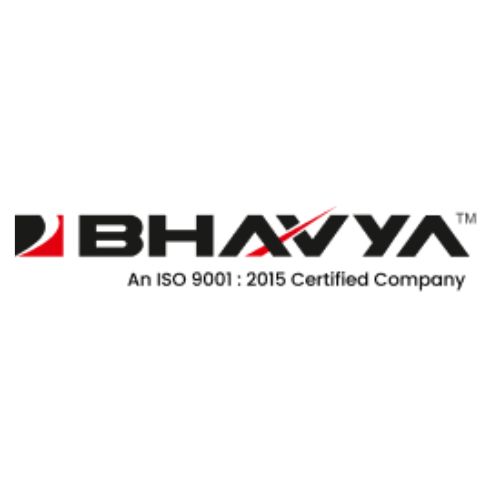
Evolution of Sheet Metal Machine
Today, Sheet Metal Machines are being widely used to perform cut, drill, press and shear on various hardened materials including aluminium, brass, copper, steel, tin, nickel, etc. These operations help reform the shape and size of the materials. Uses of…
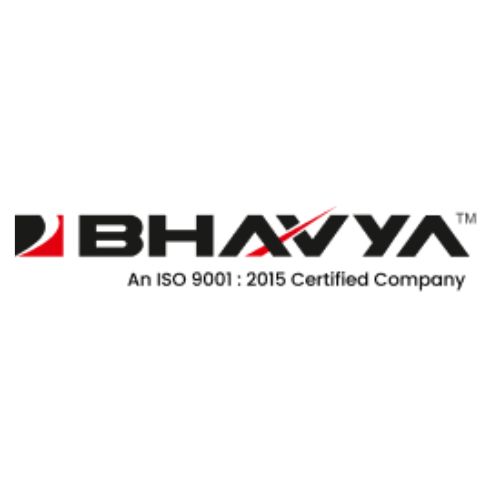
Importance of Sheet Metal Machinery in Containerization Process
Containerization in International Transport International and local transport has grown considerably due to globalization and internationalization. There has been a global increase in dependency on commodities manufactured from low wage countries such as China, India, Africa and Asian nations. This…
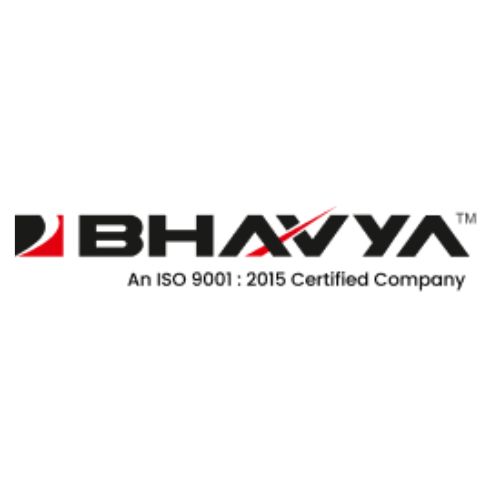
Requirements for Woodwork Machinery and Machinist for Interior Decoration
Demand for Modern Woodwork There has been a great difference seen in people’s outlook towards spending on modern furniture. On one hand, modernity caters to the different needs of consumers like space saving, compact, yet cost effective furniture and on…
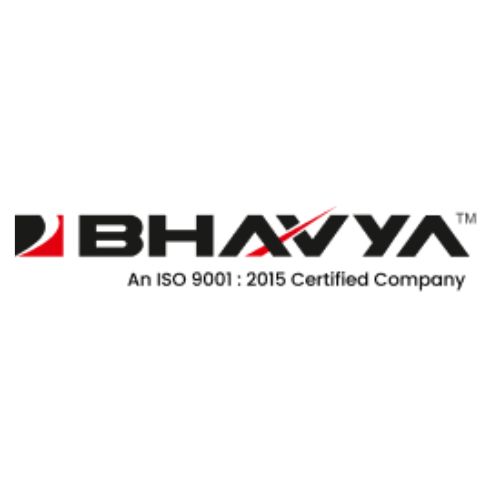
Perform Mechanical Operations on Sheet Metal Faster and Accurately Using Specially Designed Sheet Metal Forming Machines
Capitalize on your return and enhances production efficiency using sheet metal forming tools. These are well designed in ensuring efficiency accuracy and increases the mechanical performance in the metal forming industries. It is constructed with high quality materials enabling it…
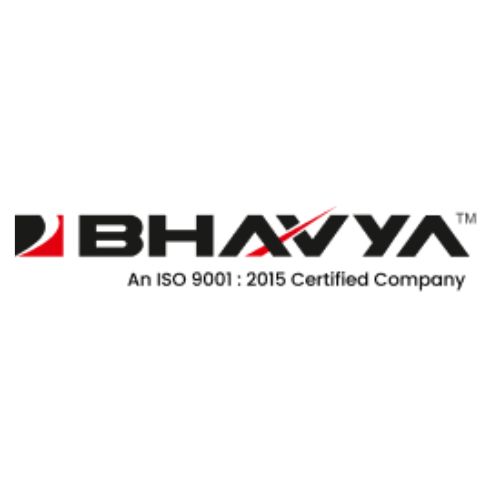
How Sheet Bending Machine is Customized by Manufacturers to Handle Variable Thicknesses of Sheet Metals?
The peculiarity of sheet bending machine Among the workshop devices, the aspect of bending metal sheets to the desired dimension can be done only with the help of specific equipment. A drilling or milling device cannot be depended on for…
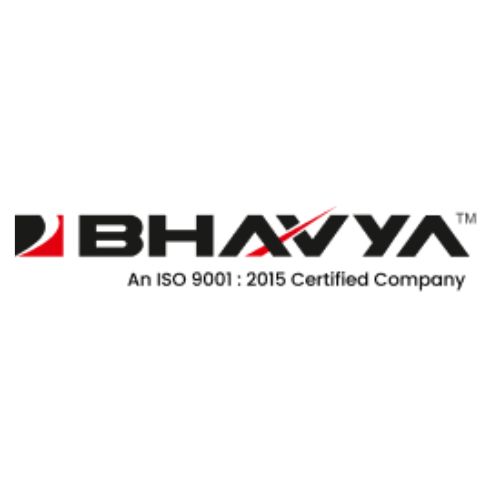
Sheet Metal Machineries for Shearing, Bending & Cutting
The various sheet metal machineries for shearing, bending and cutting are described below: Press Brake The mechanical press brake has a sturdy frame built from high grade steel. It also consists of steel plates with appropriate thickness and machined guide…
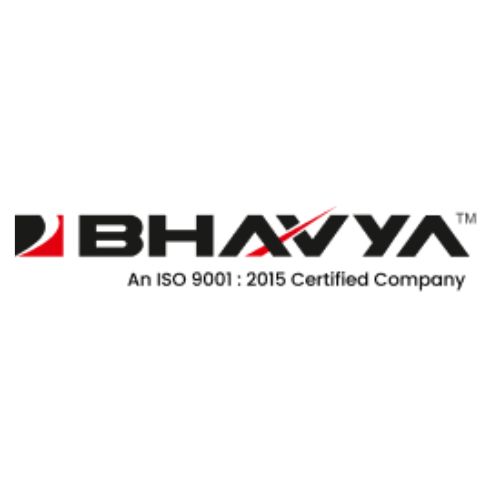
Industrial Applications of Different Sheet Metal Machineries
Metals play an important part in our lives today. Think of any object around us and either it is made of metal or some part of it is of metal. Metals are an integral part of our lives today. A…
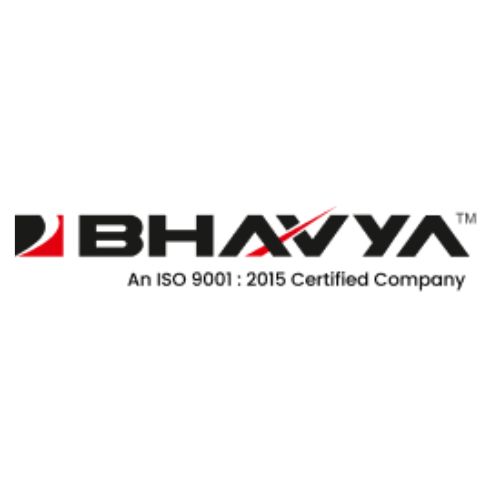
Guide to Various Kinds of Sheet Metal Machines Used in Workshops
Sheet metal machines are primarily utilized for cutting, shaping, pressing, and forming metal sheets into specific shapes and dimensions. Nowadays a number of sheet metal are available in the market. The various kinds of tools used in workshops are as…
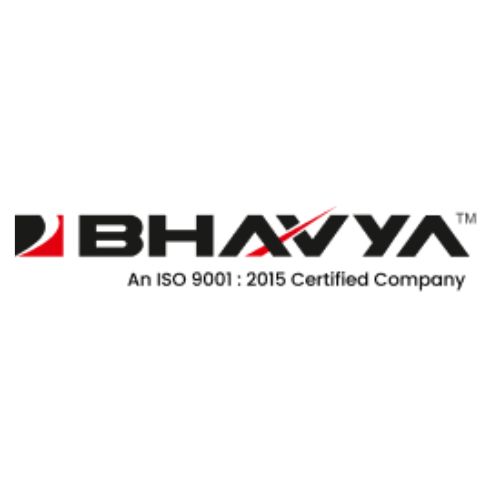
Understanding Some Facts About a Sheet Metal Machine
These days a broad range of sheet metal machinery is utilized for performing various functions such as metal cutting, bending, pressing, forming, perforating, spinning, roll forming, press brake forming, deep drawing, rolling, decambering, ironing, stamping, etc. Moreover, these machines are…
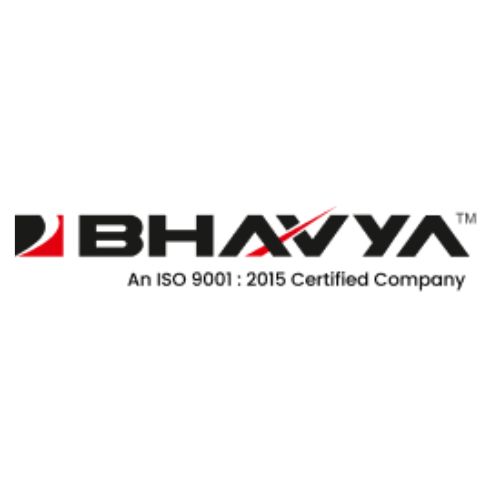
Things to Know Before Buying Sheet Metal Machinery
A sheet metal machine is used to cut, press, bend and form sheet metal into various shapes and sizes. These help to easily, quickly and effectively; perform a wide range of tasks, such as cutting, stamping, bending, perforating, ironing, spinning,…