Monthly Archives: February 2015
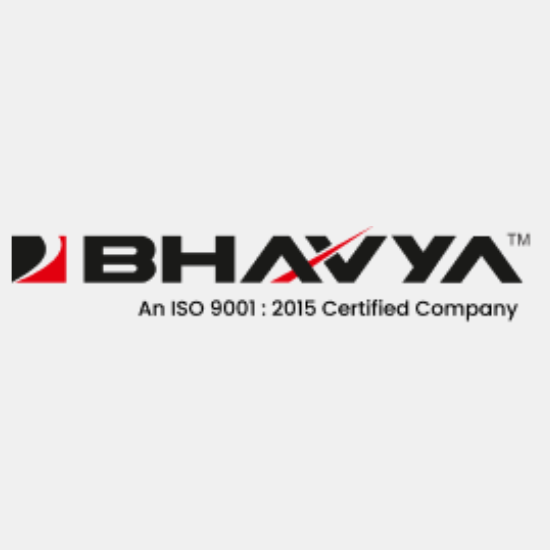
How to Manage Milling in Depth?
Growing Milling Requirements Mill is one of the priority equipments for metal industries and fabrication jobs. It helps it getting the toughest metal components ready to be composed for final produce. It is one of the main devices that prepare…
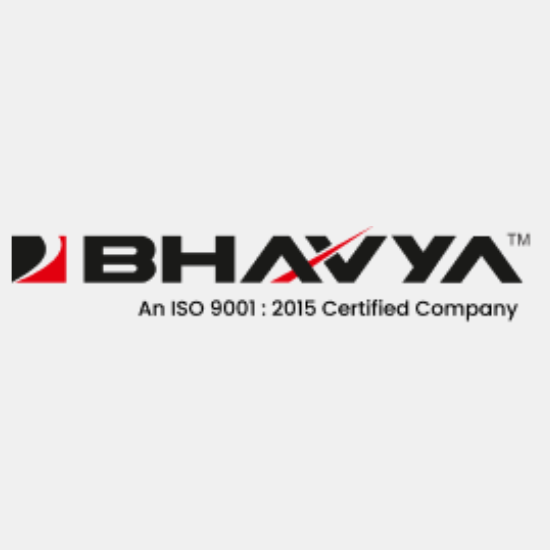
5 Important Revisions in Traditional set up of Press
Traditional Press Setup Traditional press brake setup was found to be with hydraulic principle and the usage can be traced back to ancient Mesopotamia and Egypt. Later as years went on Greeks introduced some changes into the provisions considering suitability…
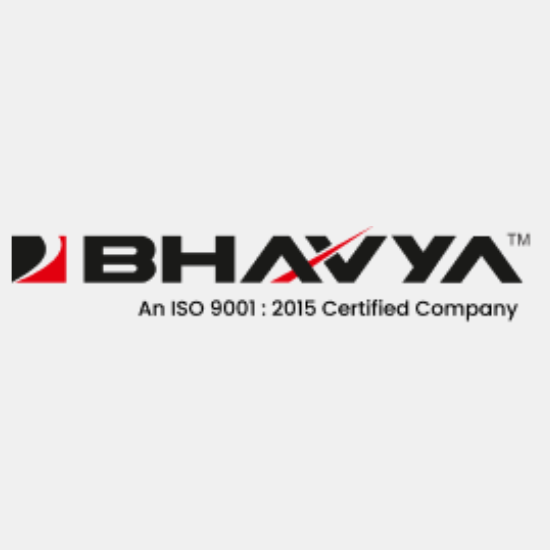
Blade Metallurgy – Why Industries Concerned Much about This?
Metals and Metallurgical Concern in Industries Metallurgical concern is more important when it comes to selection of machining components. If you are very particular about investing for long term and continuous production requirements, then selection of equipments which are designed…
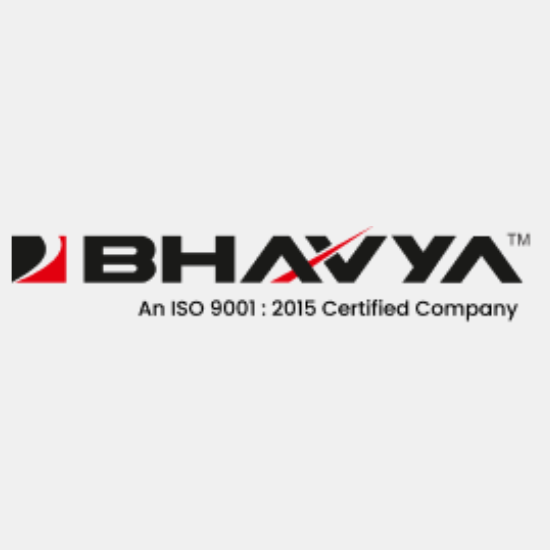
Metal Deformation Requirements in Manufacturing Sectors
Why a change in Geometry is required? Manufacturing of metal components involves application of metals as raw materials. When it comes to producing structural gadgets, a lot has to be done with work materials. Therefore, change in geometry of raw…
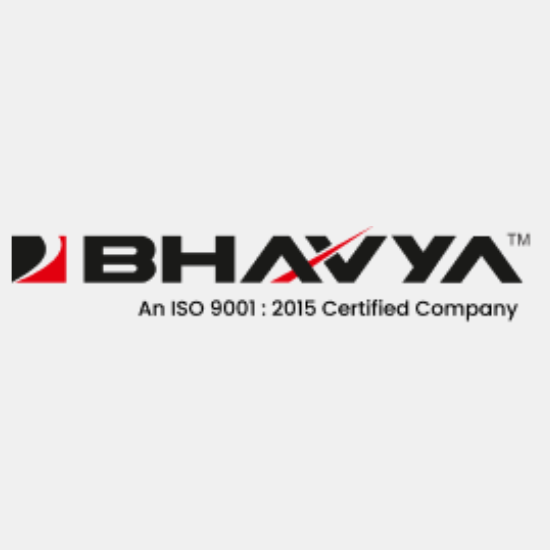
The Top Mandatory Aspects of Drilling in Industries
Common Forms of Piercing Piercing has different connotations when it comes to industrial process. It is applied in various ranges depending on the intensity required. In addition, this application is implemented over different materials and surfaces in accordance with the…