Monthly Archives: November 2013
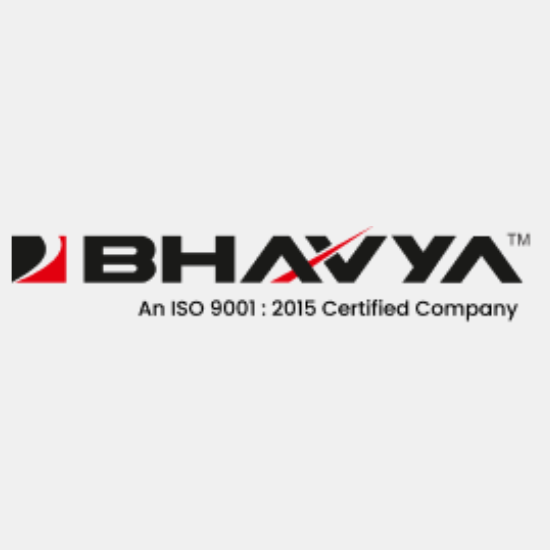
A CAD Directed Milling Device-The Ultimate Solution to Work with Multiple Tool Heads
Working with Multiple Tool Heads-The Interesting Aspect of Milling Milling device is a special component designed to shape different solid work materials such as metals, wood, etc. While machining solid work pieces the equipment helps to bring out the desired…
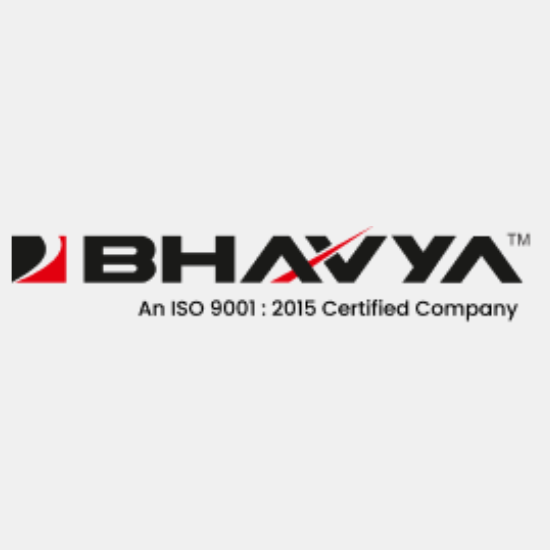
Learning The Art of Utilizing Cutting Principles with Turret Milling Apparatus
The Art of Cutting and the Different Requisites of Milling Workshop machinery is of different types and they are designed to meet various machining works such as bending, drilling, shearing and many more. Every equipments has a specific purpose and…
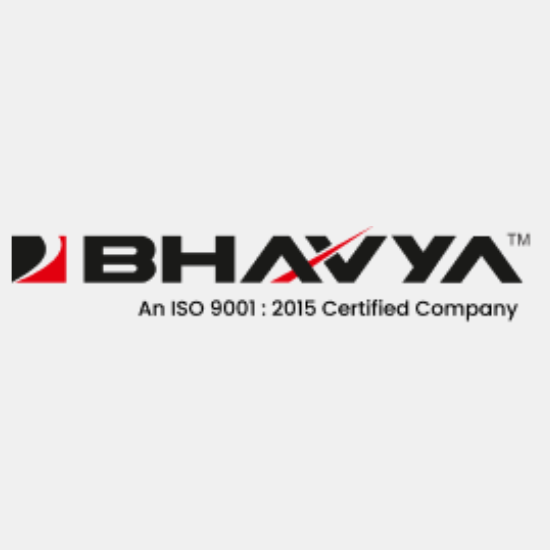
How Bending Process Influence The Work Piece to Obtain Stiffness
Facts behind Bending Work Piece Metals Metal work piece and subsequent machining process done over them had been very tough as most of the times the shaping of metal work piece was completed with manual assistant. However, the rate of…
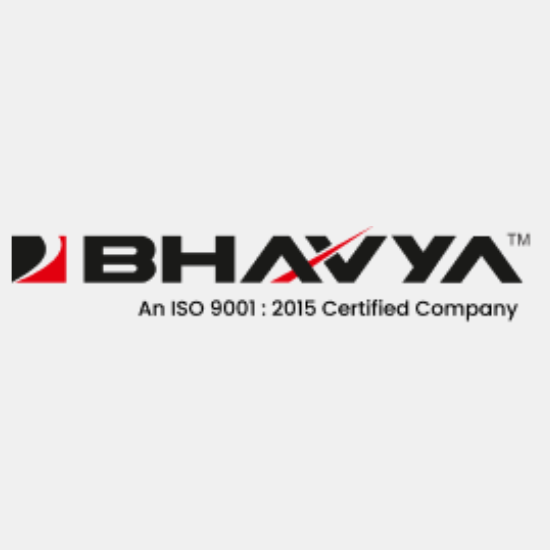
The Magic of Different Shaping Methods with Single Point Tool-A Multipurpose Solution for Flat Surface Machining
The Increasing Industrial Demand for Different Shapes Shaping of materials stays a prime requirement in the metal industry as every process is done in accordance with the expectations from different industries. Metals such as steel, cast iron, aluminium, etc are…
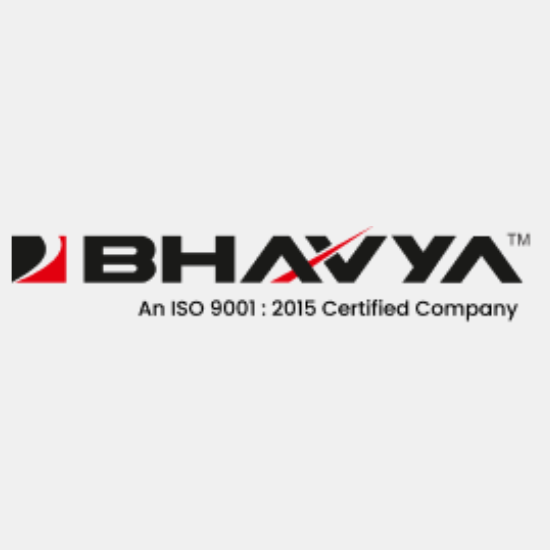
Resolving the Complexities of Delicate Machining with Slotting Device
What are the Types of Delicate Machining Jobs? A Machining job confirms the perfectness of work pieces which are then applied for various ranges of industrial requirements. Every machining work is customized in accordance with the industrial demands. Hence, workshop…
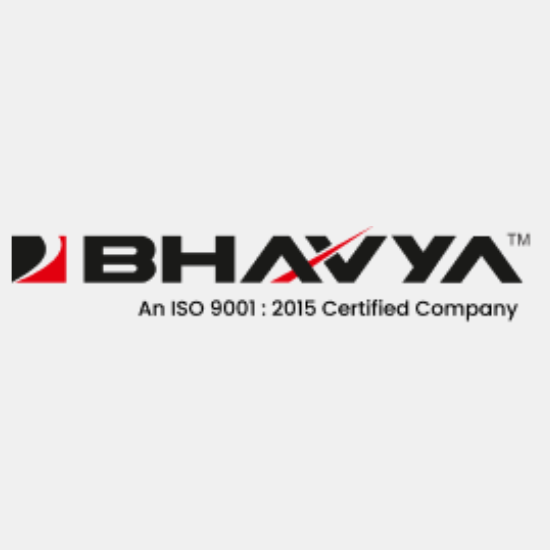
The Bandsaw machine; No more Quality losses
It used for cutting metal, wood or even meat in food processing. It is made up of a continuous band of metal with cutting teeth similar to a wood work saw. The construction of the saw blade is such that…