Monthly Archives: September 2012
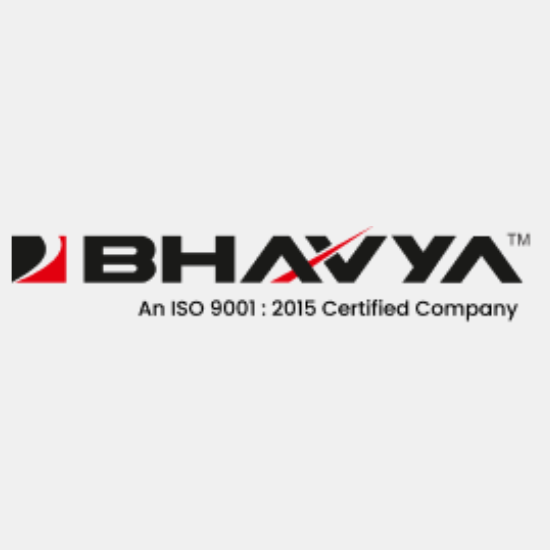
Range of Turret Milling Machine for Machining Solid Objects in Workshop
The constant development in technology and the introduction of modern machines; helps us to produce better products, optimize costs and increase productivity. All industrial units utilize a variety of machine tools; that typically include the milling machine. It is one…
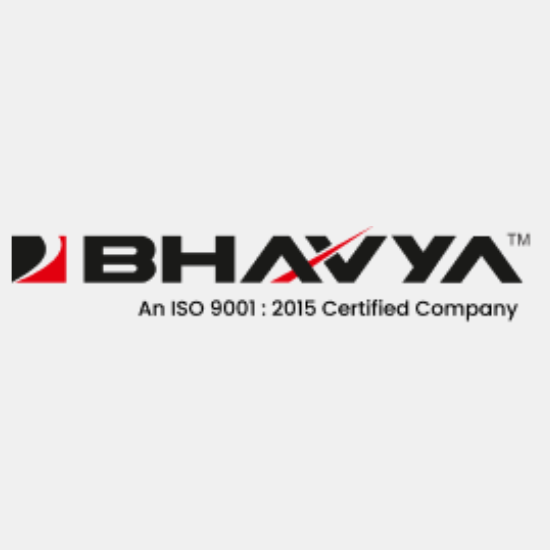
CNC Lathe Machine Range for Multipurpose Machining
The lathe is a multipurpose machine tool; that rapidly rotates the work piece along its axis to perform various tasks like cutting, shaping, drilling, turning, sanding etc.; in order to create a symmetrical object. Nowadays, the latest manufacturing machines use…
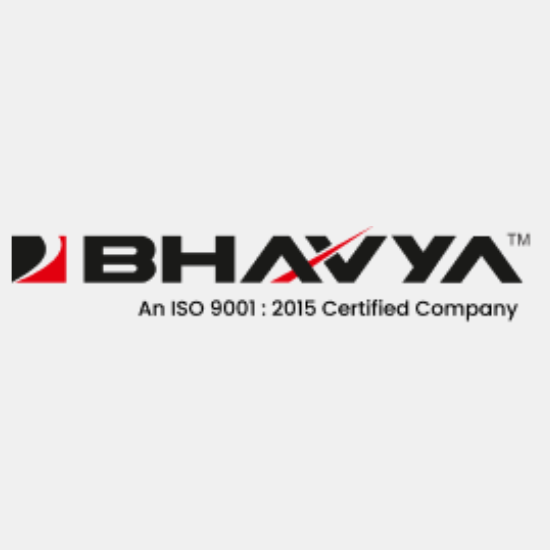
Types of Drilling Machine – Radial Drill Machine for Construction, Woodworking & Metalworking
The drilling machine is one of the most vital tools. It has transformed a lot of complex manufacturing processes into very simple tasks. It is an important tool that is used in several industrial and commercial operations; such as construction,…
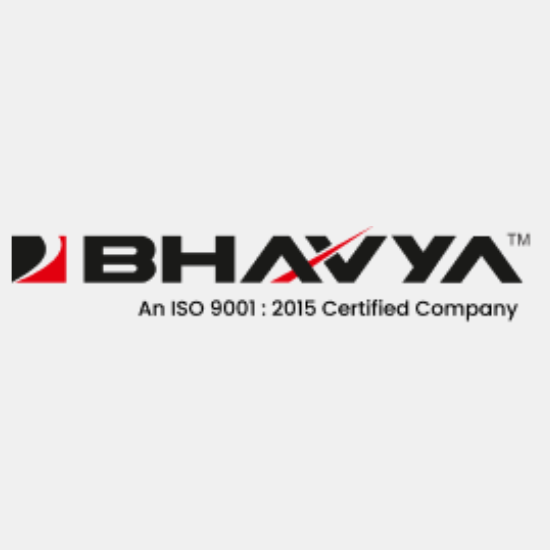
Lathe Machine Operations
Nowadays, the tool room work and workshop machine activities; are done by repairers or through suitable lathe tools. A lathe is a tool utilized to perform various functions like turning, cutting, drilling, grooving, knurling, parting, threading etc. They are used to produce accurate products made from…
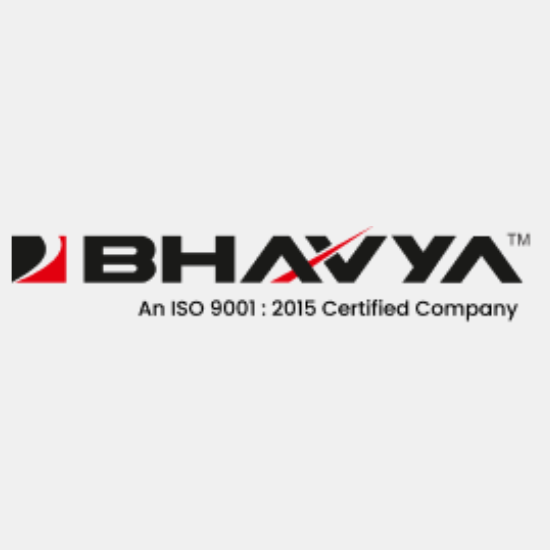
Conventional Lathe Machine
The invention of machines has resulted in saving our time, money and energy. Additionally it even helps us to produce better quality goods. The lathe is one of the oldest and most important machine tools. The earliest types of lathes…