Monthly Archives: August 2013
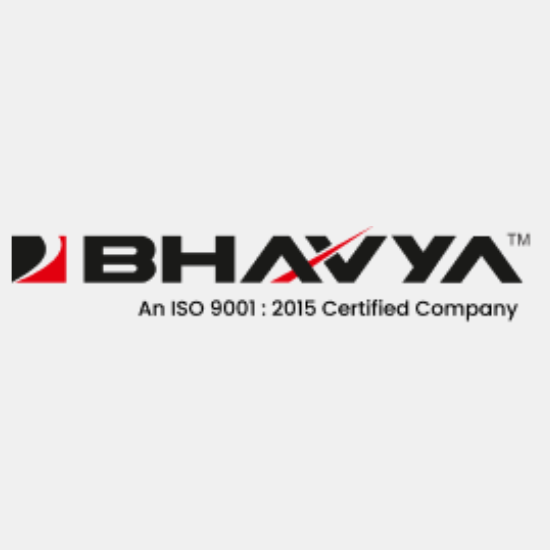
Features to Look For While Buying a V-Belt Driven Radial Drill Machine
All about V-Belt driven radial drilling machine V-Belt driven radial drilling machine is an innovative modern drilling which can be preferred for high accuracy in the process of drilling. Among the workshop equipments functionalities, drilling stays very important for the…
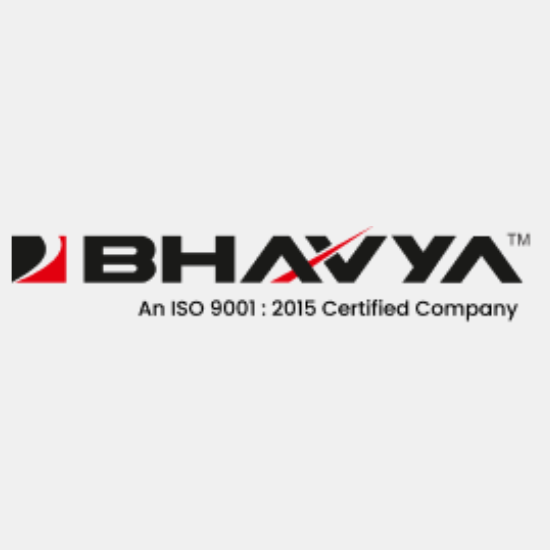
Differences between Slant Bed and Flat Bed CNC Lathe Machines
Introduction to CNC Lathes and significance of CNC Lathe equipment is one of the workshop machineries that can be used for a range of machining purposes such as shearing, sanding, turning, drilling, shaping, etc. A lathe works for different types…
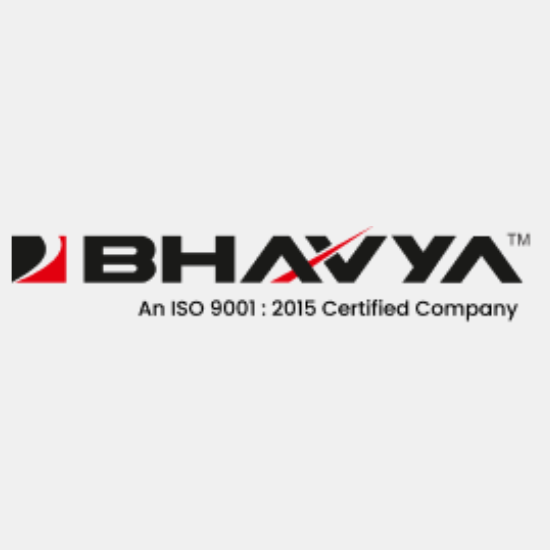
Possible Bending Variations with Press Brake
The Purpose of Press Brake A press brake is workshop equipment that is mainly used for bending metals and metal sheets. Wherein, it can be done either in V shape or U shape in accordance with the industrial requirement. It…
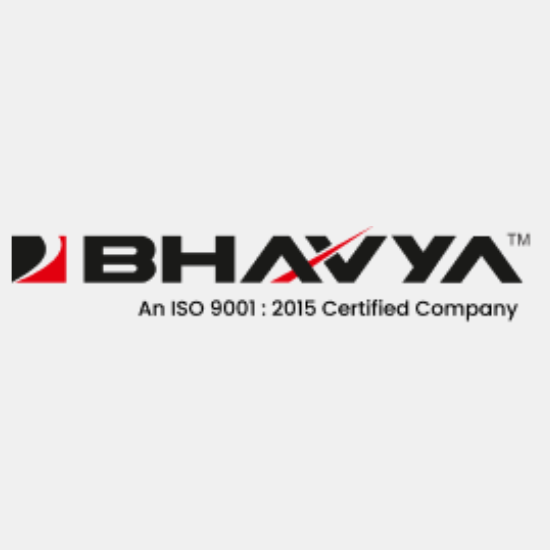
Operational Efficiencies and Drawbacks of a Turret Milling Machine
What is Turret Milling Machine? Workshop machineries stay useful for several core machining works. It is one of the workshop equipments that are used particularly for cutting metals into a predetermined shape. It is preferred for workshop process to obtain…
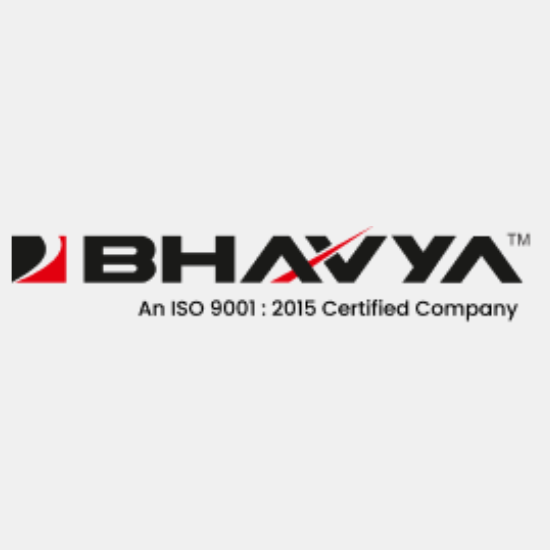
How to Set Up a Workshop for Metal Jobs?
Why A Workshop Is Necessary for Metal Working? The metal work will comprise of light metal applications such as jewelry to heavy duty applications such as automotive garage or building bridges. Metal work is an energy intensive activity that produces…