Monthly Archives: September 2024
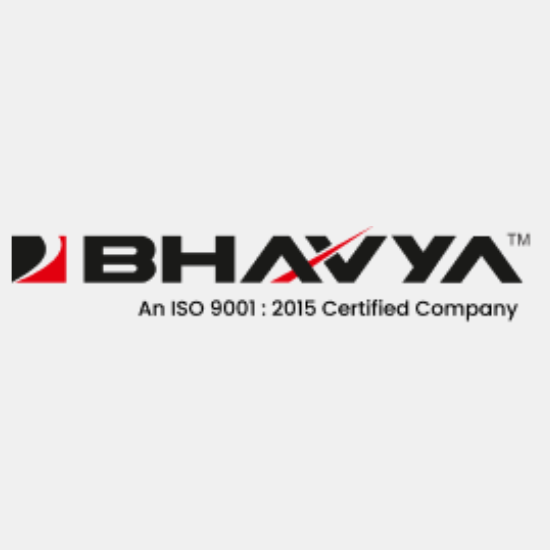
Surface Grinding Machines: Precision and Efficiency in Machining
Introduction Surface grinding machines are indispensable tools used for achieving precise and smooth surfaces. With the ability to remove any surface irregularities, they play a vital role in various industries, including automotive, aerospace, metalworking, and construction. The surface grinder works…
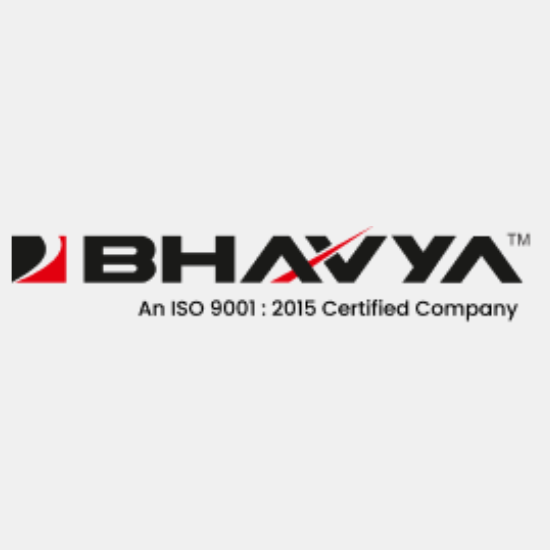
CNC Press Brake Machines: Precision, Efficiency, and Reliability for Industrial Bending
Introduction In today’s fast-paced manufacturing environment, precision and efficiency are critical for staying competitive. CNC press brake machines offer the perfect solution for precise bending and forming of various materials, particularly sheet metal. These machines provide user-friendly and cost-effective solutions…