Monthly Archives: July 2013
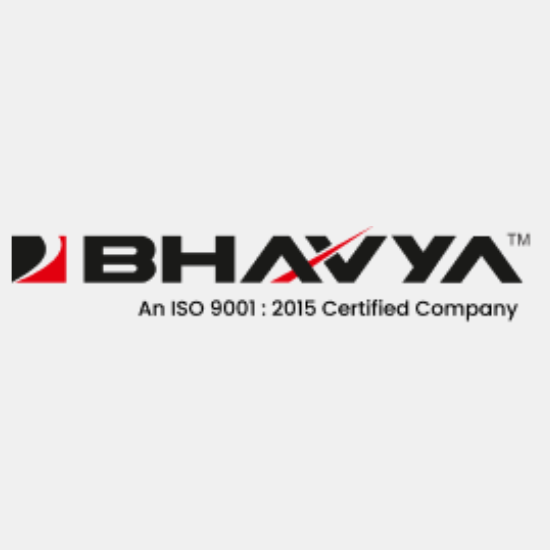
How are mechanical and hydraulic press brakes employed for sheet metal bending?
Press brake or break press is a equipments used for bending sheets of metals, or other materials. Prior to using a metal plate or a sheet it has to be shaped or formed. To do this a machine or a…
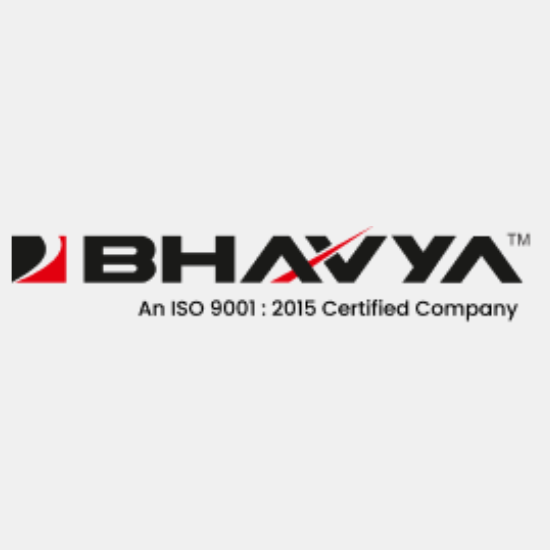
Features of a Sheet Bending Machine
With a sheet bending machine you can bend a sheet of metal. The whole sheet can be placed on the surface and bent according to your requirement to make metal structures. Pressure is applied to the metal sheet in order…
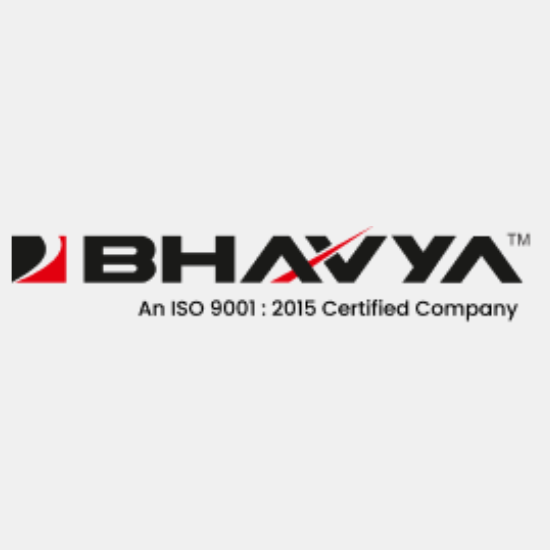
Importance of High Precision Drilling Machines in Metal Industries
Today, high precision drilling machines are regarded as one of the most important tools in the metal industry. This is because accurate drilling is always necessary for a vast number of manufacturing processes that are related to different types of…
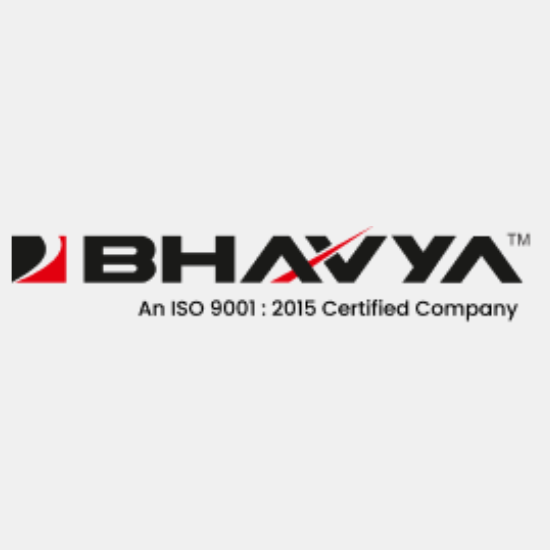
Popular Variants in V-Belt Drive Lathe Machine Available Today
The lathe is one of the most essential tools. It is used for numerous purposes such as boring, cutting, drilling, grinding, grooving, knurling, parting, polishing, reaming, threading, turning, etc. Actually, this versatile equipment helps to manufacture precise products made from various materials like metal,…
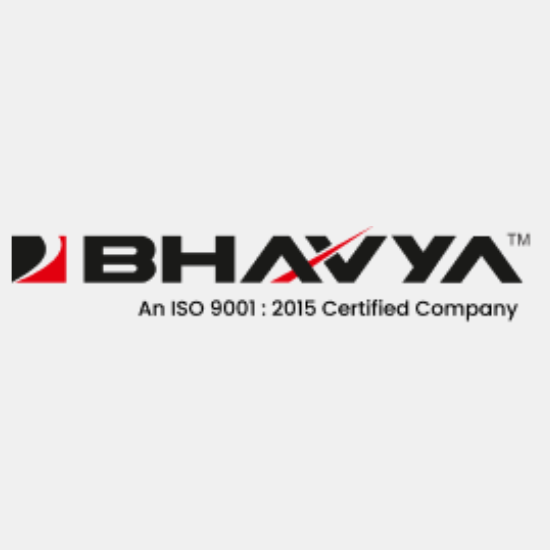
Lathe Machine – Types & Applications of Lathe Machines [INFOGRAPH]
Lathe machines are the tools to produce objects that have correspondence about an axis of rotation and used for precise machining to the relative hard materials. Thus this tool rotates the work piece on its axis to perform variety of…
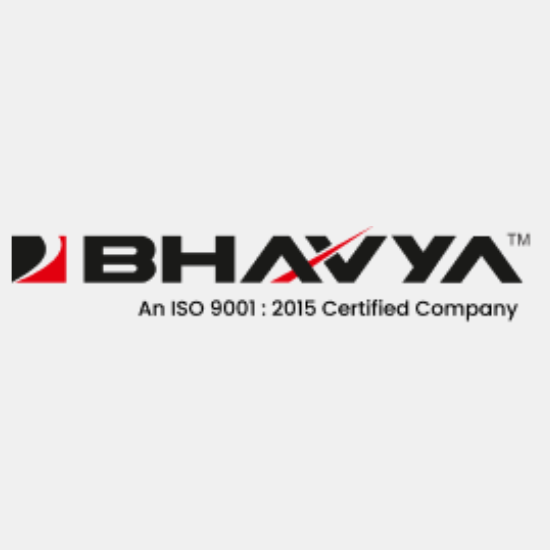
Difference between CNC turret Milling machine and a normal milling machine
Milling is the process by which rotating cutters remove extra material from a metal or wood piece of work to give it a definite shape by means of a machine. It is a frequently used process in the industry and…