Monthly Archives: May 2015
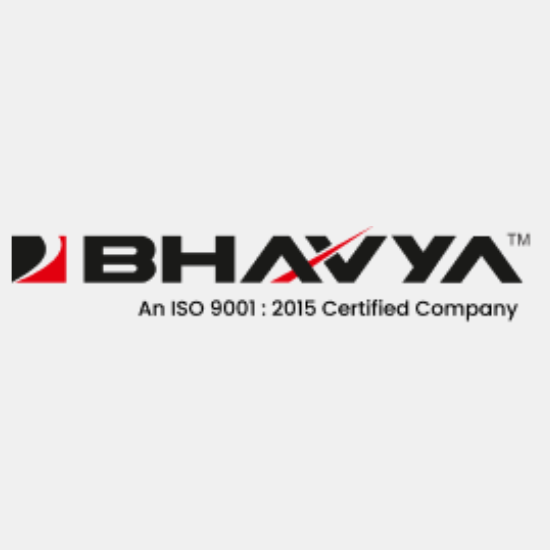
High Speed Production of Railway Line
High Tensile Materials for Making Rail Components Transporting vehicle needs excellent strength to bear load and support durability of usage. Cast or wrought iron are the most important raw ingredients considered for making cross sectional shapes of railway rail. These…