Monthly Archives: June 2015
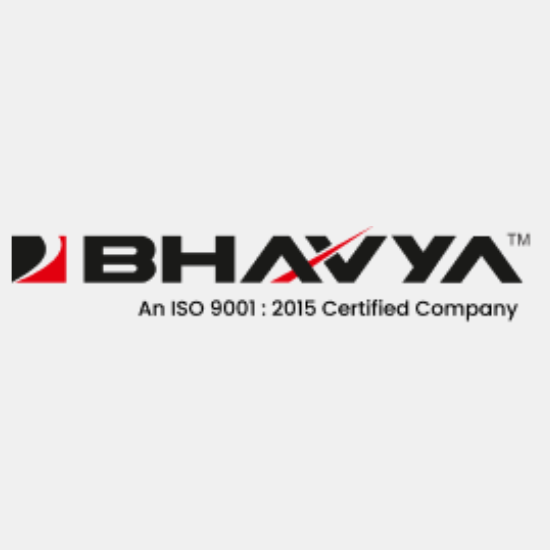
Channel Bending For Making Door and Window Frames
Creative Works using Metal Components Metal materials are also applied for making creative ideas like art work, designer steel doors, window frames, etc. However, range of bending operation varies when compared to customary ones. The type of reforming that suits…