Monthly Archives: February 2016
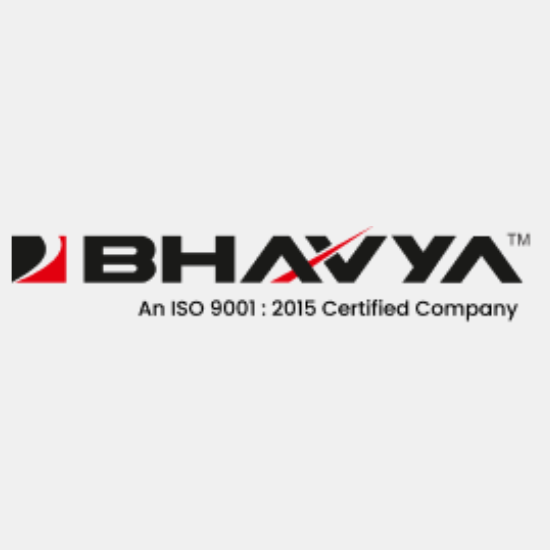
The Sheet Bending Machine in Iron Sheet Manufacturing
Introduction to Sheet Bending Machine Iron and steel are the most common fabrication material in manufacturing and repair shops. They are widely used in construction, assembly, vehicle manufacture, processing and packaging industry. Large metal plates are produced in form of…