Category Archives: Bolt Threading Machine
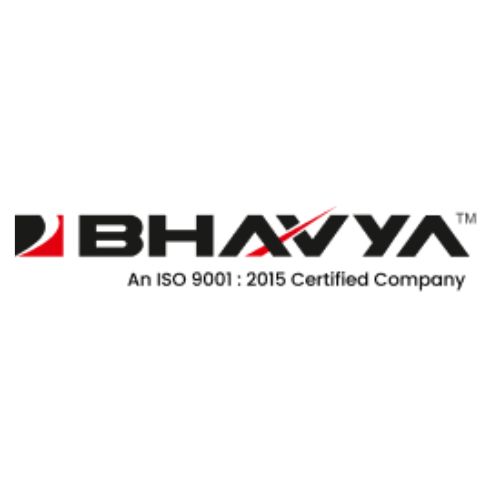
What to Look for When Shopping for Bolt Threading Machines?
Bolt threading machines provide high-quality machining services, maintaining consistency when threading various pipes and bolts. They are ideal for many industries, particularly those in harsh environments, which require consistent, reliable output and durability. Threading is a crucial process that directly…
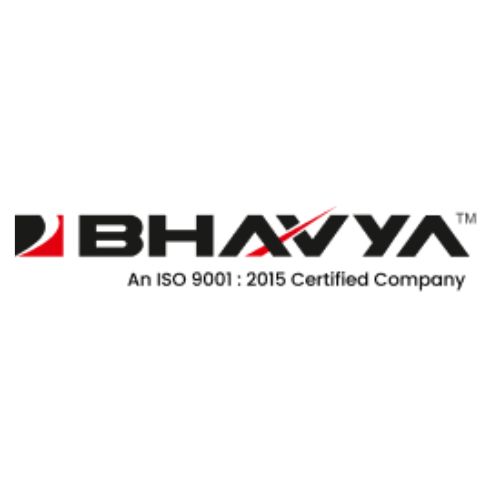
Special Purpose Machine Tools in the Ship Building and Industry
SPM machines are equipments designed to perform tasks that ordinary machining tools cannot handle due to the size, weight and unique features of the work piece. The ship building industry is characterized by larger and heavier size engines requiring heavy…