Category Archives: Workshop Machinery
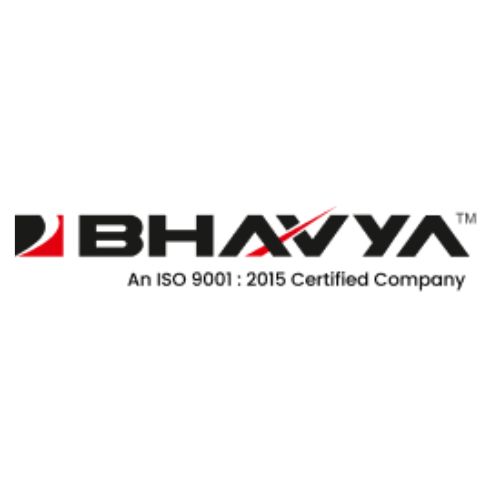
The Evolution of Lathe Machines in Bangladesh’s Textile Industry
Lathe machines have played a transformative role in Bangladesh’s industrial sector, particularly in textile manufacturing. These machines, which shape metal and wood into precise forms, are essential for producing textile machinery components. Over the years, the demand for imported lathe…
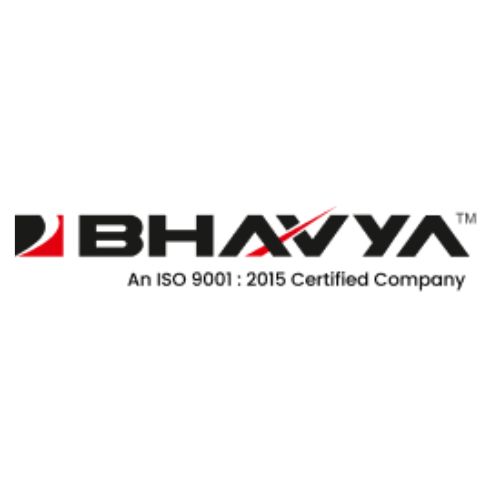
Machining Technology Developments Have Changed the Manufacturing Landscape
Recently, the machine tools industry is enjoying unprecedented surge in demand worldwide. To the surprise of many manufacturers, the output is still unable to satisfy this demand. There have been certain areas of the machine development and innovation that have…
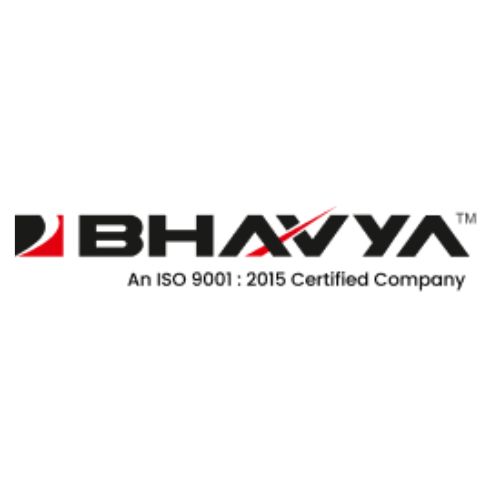
Bhavya Machine Tools – Symbol of Quality Machine Tools Manufacturing
Bending Machine The various types of bending machines include the bus bar bending machine, profile bender, pipe bending machines, metal sheet bender, motorized and manual pipe benders. These are innovative forming machines generating bends on a metal work piece. This…
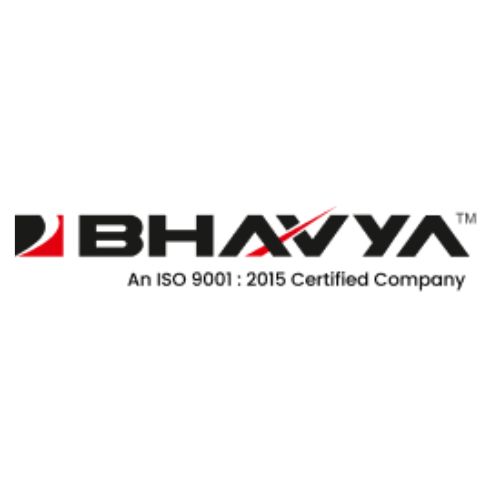
Workshop Machinery and Its Significance in Engineering World
Workshop is the core of learning about different Materials, equipment, tools and manufacturing practices that are observed in different manufacturing functions and operations. Workshop is also of prime importance when you want to gather about the practical knowledge. There are…
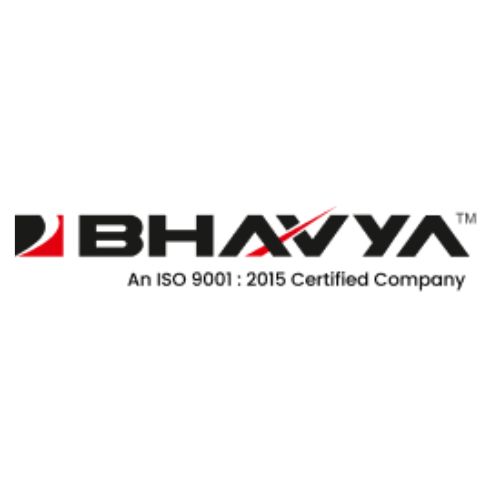
Working Principle & Significances of Shaping Machine
Working principle of shaping machine Among the range of workshop machineries available a shaping machine stays very useful to shape the surface of metal, wood or steel surfaces to a desired shape or dimension. It is quiet easy to obtain…
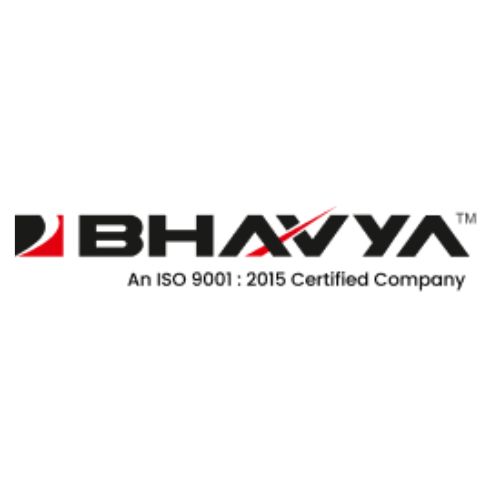
Safety Norms for Workshop Machinery
Bhavya Machine Tools is a leading supplier of work shop equipments suiting wide range of industries and as far as wood working machinery is concerned, they manufacture and supply plenty of wood working devices to handle different aspects of wood…
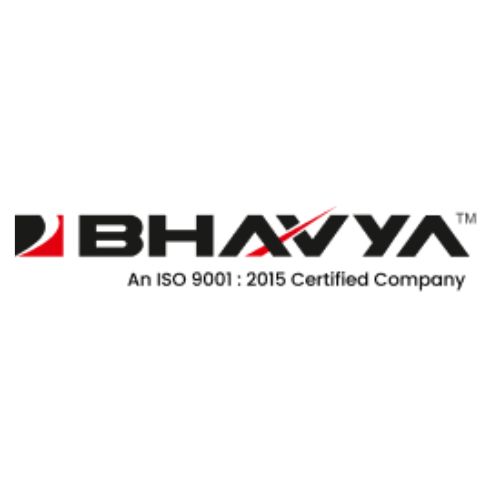
Operational Efficiencies and Drawbacks of a Turret Milling Machine
What is Turret Milling Machine? Workshop machineries stay useful for several core machining works. It is one of the workshop equipments that are used particularly for cutting metals into a predetermined shape. It is preferred for workshop process to obtain…
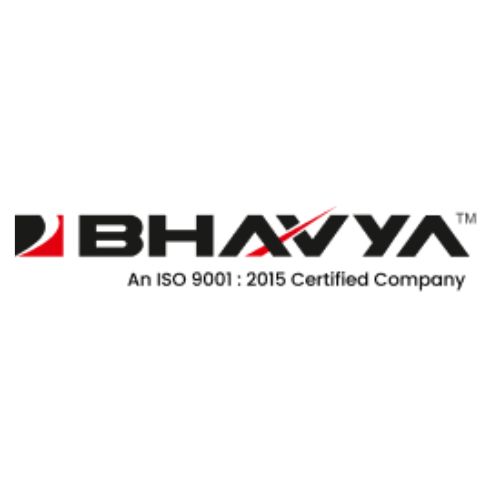
How to Set Up a Workshop for Metal Jobs?
Why A Workshop Is Necessary for Metal Working? The metal work will comprise of light metal applications such as jewelry to heavy duty applications such as automotive garage or building bridges. Metal work is an energy intensive activity that produces…
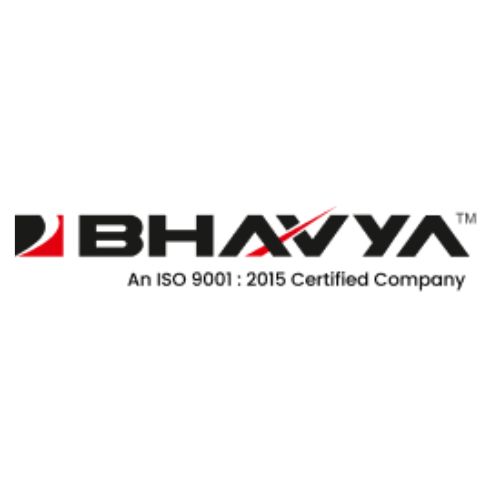
5 Most Important Machine Tools For Any Workshop [INFOGRAPH]
Nowadays, several types of workshop machine tools are manufactured in many countries around the globe. These tools are commonly used for different purposes in a wide range of industrial segments such as woodworking, automobile, electrical, construction, etc. This infograph give…
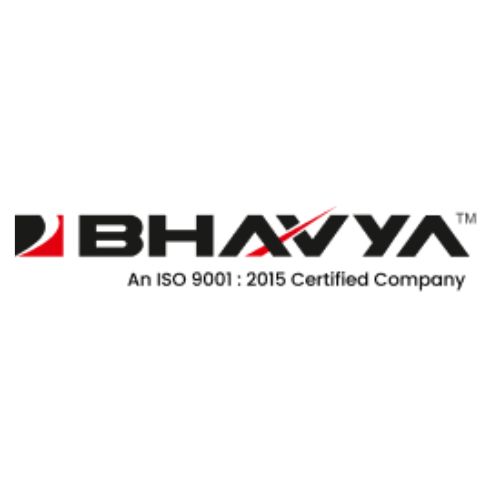
Rising Demand of Woodworking Machineries Across the World
Woodworking machines are highly popular and widely used equipments. They are basically utilized for performing various processes on wood, such as cutting, carving, drilling, finishing, grinding, joining, molding, sawing, sanding, shaping, etc. It help to avoid manual labor and the conventional…
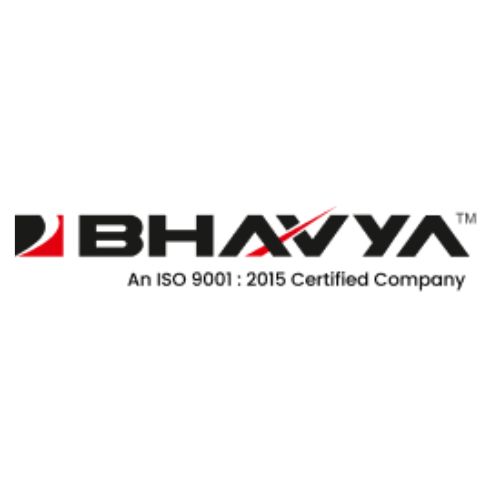
Popular Types of Woodworking Machinery Used in Workshops and Industries
Machines employed in a wood processing operation to cast the desired shape or dimensions from the wood work piece are known as woodworking machine. It may be manual operated or computer controlled machinery. Manual machines are good for the small…
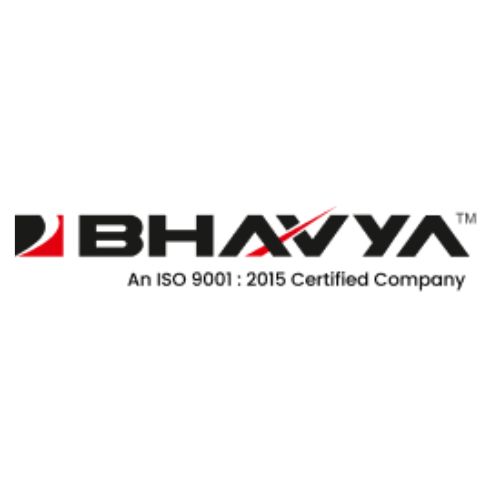
How to Use a Grinding Machine Safely?
The grinding machine is utilized in a tool shop for various purposes such as finishing, forming, sharpening, cutting, roughing, snagging, cleaning, polishing, buffing, etc. However, while operating a grinding device, it may cause serious injuries to the operator or any…
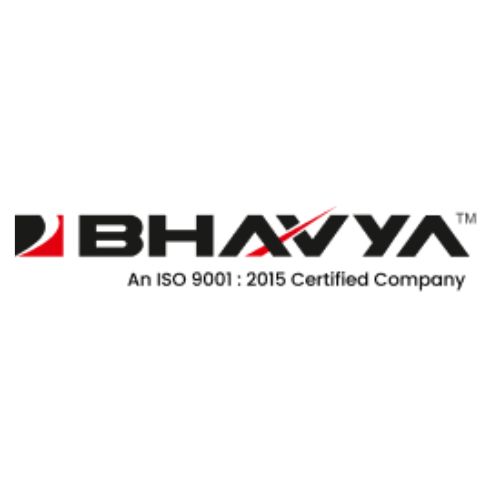
Significance of Buying Only Safe Workshop Machinery
These days, an extensive variety of workshop machinery is manufactured by several countries throughout the world. Besides this, regular research followed by constant development has resulted in the availability of new, as well as better equipments and latest tools like…