Category Archives: Workshop Machines
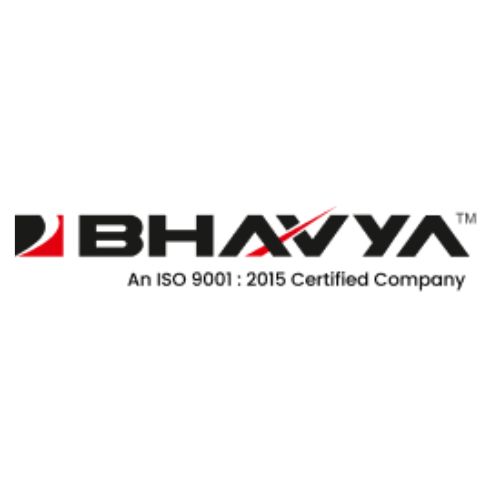
The Evolution of Lathe Machines in Bangladesh’s Textile Industry
Lathe machines have played a transformative role in Bangladesh’s industrial sector, particularly in textile manufacturing. These machines, which shape metal and wood into precise forms, are essential for producing textile machinery components. Over the years, the demand for imported lathe…
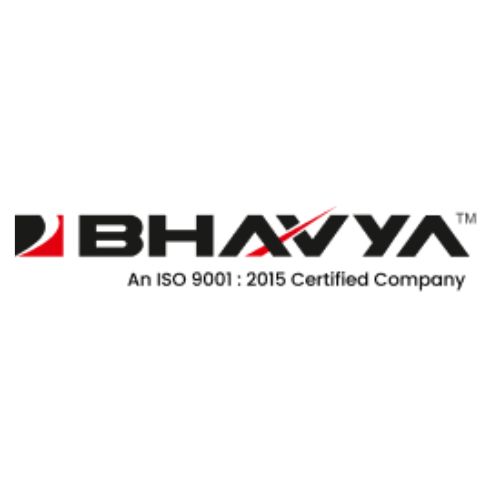
A World Without Machine
Are you fascinated by the world of machine? Can imagine a world without machine? It might be tougher question to answer than you think, as many people don’t actually know to which extent we are dependent on it. One can’t…
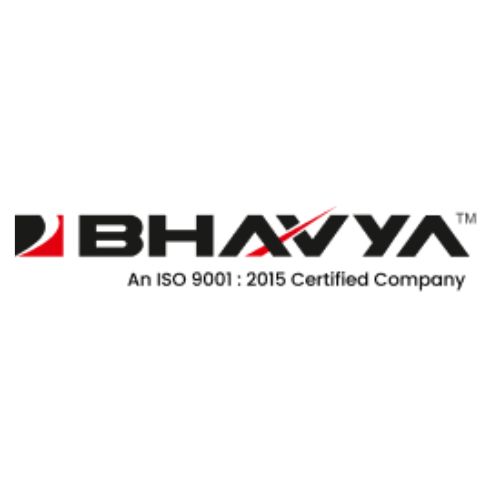
India is Growing as Global Hub in the field of Manufacturing Machine Tools
Machine tools manufacturing Industry is a very planned and important industry today. Indian manufacturing industry has grown many fold be it automobiles, aerospace, defense, electric machinery. For a country to progress, to become influential it must progress in technology. Today…
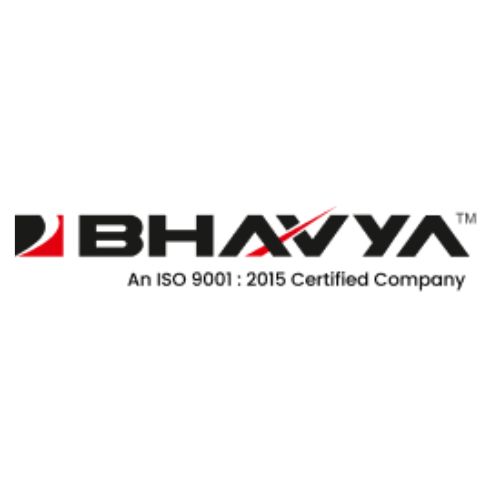
How to Set Up a Workshop for Metal Jobs?
Why A Workshop Is Necessary for Metal Working? The metal work will comprise of light metal applications such as jewelry to heavy duty applications such as automotive garage or building bridges. Metal work is an energy intensive activity that produces…
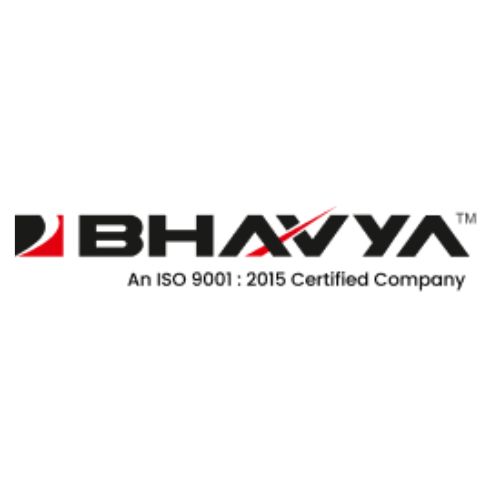
Benefits of Buying Machine Tools from Indian Manufacturers
The machine tool industry is regarded as the backbone of any industrial economy. It is basically the source through which a broad variety of industrial products and consumer goods are manufactured. India is a developing nation with a rising economy,…
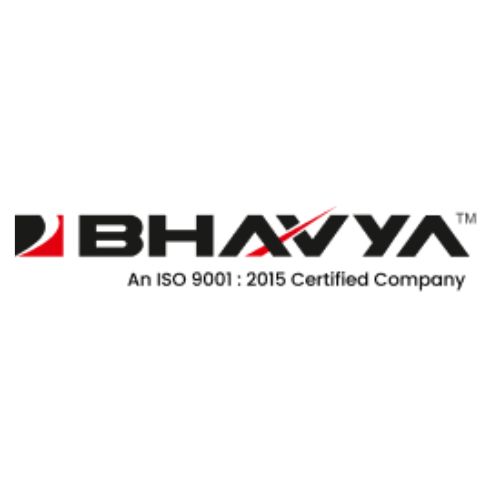
Why Quality Workshop Machinery is Very Important?
The research and development activities have resulted in manufacturing a variety of new products including several types of workshop machinery. In fact equipment play an important role everywhere and affect almost every person, in any part of the world. Today…
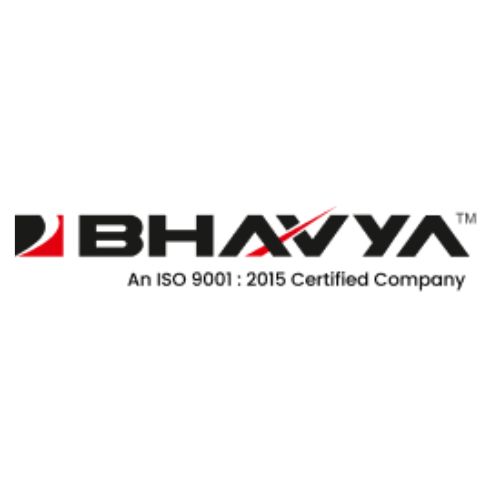
Lathe Machine Operations
Nowadays, the tool room work and workshop machine activities; are done by repairers or through suitable lathe tools. A lathe is a tool utilized to perform various functions like turning, cutting, drilling, grooving, knurling, parting, threading etc. They are used to produce accurate products made from…