In the manufacturing world, precision and efficiency are paramount, particularly when it comes to metalworking and component finishing. Two common machines used in grinding processes are the centerless grinder and the hydraulic cylindrical grinder. Although both machines perform the same fundamental function – grinding materials to precise dimensions – the way they achieve this differs significantly. Understanding these differences is crucial for businesses in industries such as automotive, aerospace, packaging and metal processing to choose the right machine for its specific needs.
What is a Centerless Grinding Machine?
A centerless grinding machine is designed to grind cylindrical parts without the need for a central axis to hold the workpiece. The mechanism of the centerless grinder is unique, as it uses two primary wheels: a grinding wheel and a regulating wheel. The grinding wheel removes material from the workpiece, while the regulating wheel controls the speed and rotation of the part. A critical feature of the centerless grinding machine is that it does not require additional methods of holding or clamping the part, which is one of the reasons why it is ideal for high-volume manufacturing.
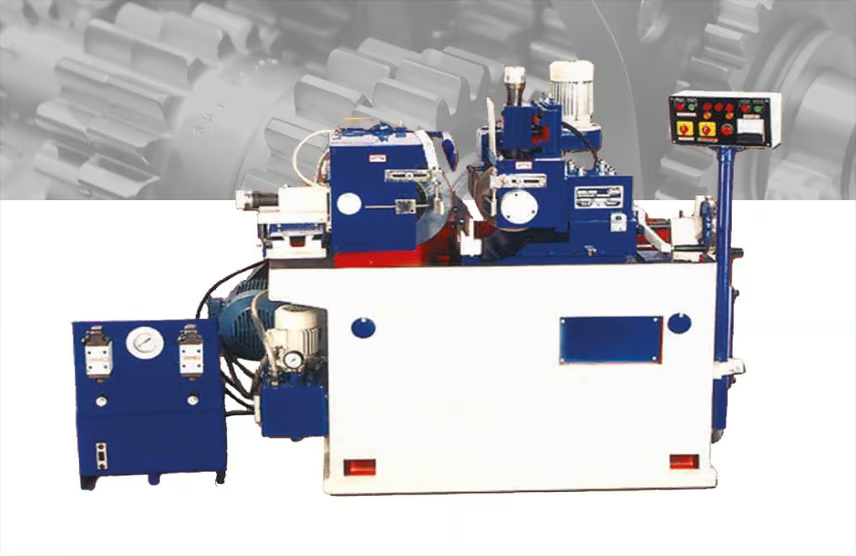
Mechanism of the Centerless Grinder
The mechanism of the centerless grinder operates by feeding the workpiece between the grinding wheel and the smaller regulating wheel. The part is supported by an angled workpiece support, which allows it to remain stable during the grinding process. Additionally, there is a blade-like device positioned between the grinding wheel and the regulating wheel. This device helps guide the workpiece, ensuring that it maintains its correct position while moving through the grinding process.
One of the key advantages of this setup is that the centerless grinder does not require the workpiece to be centered or clamped like in traditional cylindrical grinding. This allows for faster processing times and reduces setup requirements, making it an excellent choice for mass production.
What is a Cylindrical Grinding Machine?
A hydraulic cylindrical grinder is a traditional grinding machine used to grind cylindrical components, typically by holding them between two centers or by using a chuck. This type of machine uses a rotating abrasive wheel to smooth the surface of the workpiece. Unlike the centerless grinding machine, which does not require clamping or centering, the cylindrical grinding machine relies on precise mounting of the workpiece to ensure uniform grinding.
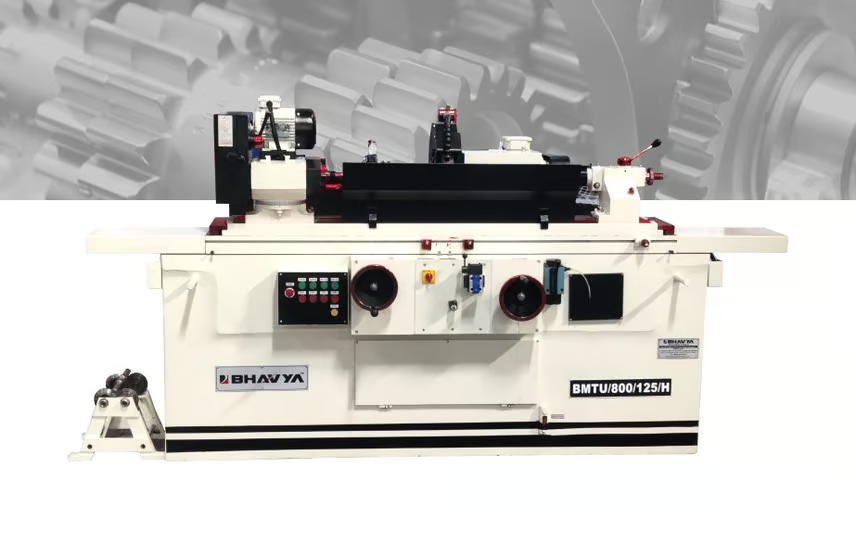
Applications of the Hydraulic Cylindrical Grinder
The cylindrical grinding machine finds wide use in industries that require high precision and intricate machining of cylindrical components. One major industry that benefits from this machine is the packaging industry, where it is used to manufacture dies, hydraulic housings and axial pump pistons. These components often require precise tolerances and complex geometries, making the cylindrical grinding machine the ideal solution for these applications.
Additionally, the hydraulic cylindrical grinder is commonly used in metal processing industries, where it plays a crucial role in fine-tuning the surface finish of components. For instance, components like shafts, gears andvalves can all be processed using cylindrical grinders, especially in industries where high-precision workpieces are critical. The ability to fine-tune these parts ensures they meet strict standards for performance and quality.
Another important application of the hydraulic cylindrical grinding machine is in the production of large, complex industrial equipment. The machine’s versatility in handling a range of materials and parts makes it indispensable in the manufacturing of industrial components, including bearings, gears andspindles.
Key Differences Between Centerless Grinding Machines and Cylindrical Grinding Machines
While both the centerless grinding machine and the cylindrical grinding machine are used for grinding cylindrical workpieces, the mechanisms and ideal use cases for each are different. Below, we explore the key differences between the two machines.
Setup and Mechanism
The setup and mechanism of each grinder are significantly different. The centerless grinder does not require the workpiece to be centered. Instead, it is supported by a blade-like device and is held in place by the grinding wheel and the regulating wheel. This mechanism allows for continuous feeding of workpieces, making it ideal for high-volume production runs.
In contrast, the hydraulic cylindrical grinder requires the workpiece to be placed between two centers or in a chuck. The workpiece must be precisely centered and the grinding wheel rotates to grind the surface. This traditional setup means the hydraulic cylindrical grinding machine may involve more setup time compared to the centerless grinder, especially for high-volume runs.
Efficiency and Speed
When it comes to speed and efficiency, the centerless grinding machine is typically faster. The continuous feeding process and the fact that parts are not manually centered or clamped reduce the setup time and increase production rates. This makes it a preferred choice for industries that need to grind large quantities of small cylindrical parts quickly, such as in the automotive or consumer electronics industries.
On the other hand, the cylindrical grinder is generally slower, as each part must be clamped and centered before grinding. This makes it more suited for operations where higher precision is required or where parts have more complex shapes.
Precision and Tolerances
The cylindrical grinding machine tends to provide higher precision and tighter tolerances. This makes it the ideal choice for industries where precision is critical, such as in the production of gears, shafts andbearings in the aerospace or automotive industries. The ability to maintain tight tolerances is essential in these sectors to ensure proper fit and function of the parts.
Although centerless grinders are highly accurate, they are not typically used for applications that require the extremely tight tolerances that a hydraulic cylindrical grinding machine can achieve. However, they are more than sufficient for high-volume production where the parts are of a uniform size and geometry.
What Our Customers Say
“Largest Display of Machinery across India. Wide range of Machines. Very Co-operative staff. Range of Tapping Machine and Re-sharpening Machines are outstanding. Very Cost effective and useful in Precision Machining Work. Their staff is co – operative for after sales support.”
Tirth Bhojani On Google
Suitable Applications
The centerless grinding machine excels in applications where high-speed and high-volume grinding are required for small to medium-sized cylindrical parts. It is ideal for industries that produce large quantities of parts with simple geometries, such as shafts, pins andbearing races. Industries like automotive, medical andconsumer electronics benefit greatly from the efficiency of the centerless grinder.
The hydraulic cylindrical grinding machine, in contrast, is better suited for applications where complex geometries or very precise tolerances are necessary. It is ideal for grinding larger parts or parts that require both internal and external grinding. Industries such as aerospace, medical device manufacturing and metal processing often use cylindrical grinders for their more complex workpieces.
Which Grinding Machine is Best for Your Business?
When selecting between a centerless grinding machine and a hydraulic cylindrical grinding machine, businesses must consider their specific needs. For high-volume production of simple cylindrical parts, the centerless grinder is the best option, offering faster processing speeds and lower setup times. On the other hand, businesses that require high precision and tight tolerances for complex components should consider investing in a hydraulic cylindrical grinding machine.
For industries such as automotive, aerospace andmedical manufacturing, where complex parts with intricate designs are required, the hydraulic cylindrical grinder is indispensable. However, for companies involved in high-volume production, such as those in the packaging or consumer electronics industries, the centerless grinder is likely the more cost-effective and efficient option.
Conclusion
Both centerless grinders and cylindrical grinding machines offer unique advantages depending on the type of workpieces being produced and the specific needs of the business. Centerless grinding machines are ideal for high-speed, high-volume applications, where parts have simple geometries and consistent dimensions. In contrast, hydraulic cylindrical grinders are better suited for applications requiring high precision, complex shapes and tight tolerances. By understanding the differences between these two types of grinding machines, businesses can make informed decisions and select the right equipment to optimize their production processes.
FAQs
What are the main benefits of using a centerless grinding machine?
The main benefits of a centerless grinding machine are its ability to handle high-volume production runs with minimal setup, faster processing speeds and the ability to grind parts without requiring additional clamping or centering.
Can a cylindrical grinding machine be used for both internal and external grinding?
Yes, a cylindrical grinding machine can be used for both internal and external grinding, making it versatile for a wide range of applications, particularly those requiring complex geometries.
Which industries are best suited for centerless grinders?
Centerless grinders are ideal for industries that require high-volume, precision grinding of small cylindrical parts, such as the automotive, medical andconsumer electronics industries.
How do I know which grinding machine is right for my business?
Consider factors such as the size and complexity of the parts you need to grind, the precision required and the volume of production. For high-speed, simple parts, centerless grinders are a great choice, while cylindrical grinding machines are better for complex or precision-required components.