In the world of precision engineering and manufacturing, cylindrical grinding plays a vital role in ensuring the production of high-quality, dimensionally accurate components. A hydraulic cylindrical grinding machine, often referred to as a Hydraulic Cylindrical Grinder, is one of the most commonly used machines for achieving superior finishes and tight tolerances in various industries. These machines are not only crucial in producing finely finished components but are also essential for achieving the desired geometries for complex parts.
Cylindrical grinders come in several types, including CNC cylindrical grinding machines, universal cylindrical grinders and high-precision cylindrical grinders, all of which cater to different levels of automation, accuracy and scale. This article delves into the key applications of cylindrical grinding machines and their importance across various industries.
Applications of Cylindrical Grinding Machines in Automotive and Aerospace?
Cylindrical grinding machines, particularly hydraulic cylindrical grinders, are widely used in the automotive and aerospace sectors for their ability to produce highly accurate and consistent components. These machines are essential in shaping parts that require a high degree of precision to ensure optimal performance and durability.
In the automotive industry, hydraulic cylindrical grinders are used for grinding crankshafts, camshafts, piston rods and connecting rods. These components demand very tight tolerances and perfect cylindrical geometries to ensure proper fitting and functionality in engines. A high-precision cylindrical grinder guarantees that the surfaces are smooth and free from defects, leading to better engine performance, reduced wear and longer service life.
In aerospace manufacturing, the requirements are even more stringent. Components such as turbine shafts, landing gears and various engine parts must meet the most precise specifications. The need for superior surface finishes and dimensional accuracy is critical and cylindrical grinding machines, especially CNC cylindrical grinders, play a crucial role. The ability to grind complex parts with varying diameters and tight tolerances ensures that components meet both safety and performance standards. Cylindrical Grinding Machines, in particular, are highly valued for their ability to handle multiple tasks simultaneously and to produce parts with high repeatability.
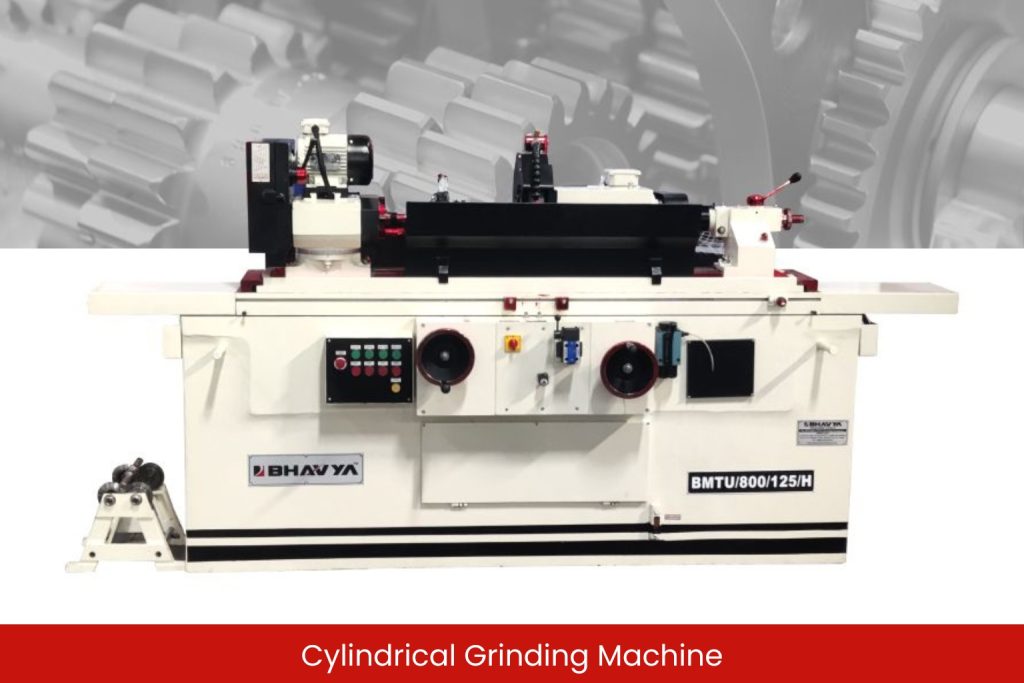
Why Cylindrical Grinding is Essential in Tool and Die Manufacturing?
Tool and die manufacturing relies heavily on cylindrical grinding machines for the production of tools, dies and molds that are required for stamping, molding and other manufacturing processes. Precision is paramount in this sector and cylindrical grinding ensures that the parts are made with the utmost accuracy.
A common application in tool and die manufacturing is the grinding of punches, dies and molds for producing parts in various industries. The precise control over the grinding process offered by hydraulic cylindrical grinders allows manufacturers to achieve the necessary geometries for these critical components. Additionally, the consistent surface finish produced by these machines is crucial for ensuring that the dies and molds perform optimally without wear and tear during high-volume production.
Universal cylindrical grinders are particularly useful in tool and die manufacturing because they are versatile and can handle a wide range of parts and sizes. These machines allow manufacturers to grind different types of materials, from metals to hard alloys, with precision and efficiency. Furthermore, cylindrical grinding machines in tool and die production provide a high level of automation, which enhances productivity and minimizes human error.
What is the use of Cylindrical Grinding in Precision Shaft and Bearing Production?
The production of precision shafts and bearings is another area where cylindrical grinding machines are indispensable. These components are used across a wide range of industries, from automotive to heavy machinery and their performance is directly linked to their accuracy and surface quality.
For shafts, cylindrical grinding is used to achieve the required surface finish, roundness and dimensional accuracy. Hydraulic cylindrical grinders can process shafts of varying lengths and diameters, ensuring that they meet the strict tolerances required for their application. High-precision cylindrical grinders are particularly valuable in this process, as they offer extremely tight tolerances that are essential for the functionality of the final product. For example, shafts used in machinery need to rotate smoothly within their housings, which requires a flawless surface finish that cylindrical grinding can provide.
Similarly, cylindrical grinding machines are essential for the production of high-quality bearings. Bearings need to be perfectly round and smooth to reduce friction and wear during operation. Cylindrical grinding machines, especially high-precision models, are used to grind both the inner and outer races of bearings to ensure they operate efficiently. The process helps improve the performance of bearings, reducing noise and increasing their lifespan. In many cases, CNC cylindrical grinders are employed to provide a high degree of automation and ensure consistency across large batches of parts.
How Cylindrical Grinding Enhances Surface Finish in Critical Components?
One of the key benefits of cylindrical grinding is its ability to provide superior surface finishes, which is essential in producing critical components used in high-performance applications. These components, often found in industries such as aerospace, automotive and medical device manufacturing, require precise surface finishes to ensure optimal function and reliability.
Cylindrical grinders, especially high-precision cylindrical grinders, are capable of achieving surface finishes that are smooth and free from any imperfections. These machines can work with a variety of materials, including hardened steels, alloys and ceramics, to deliver finishes that meet the strict requirements of critical applications. For instance, components used in aerospace engines must have smooth surfaces to minimize friction and prevent heat buildup, which could cause performance degradation or failure.
The use of cylindrical grinder machines further enhances the ability to achieve superior surface finishes. With computer-controlled precision, these machines can produce parts with a consistent finish, ensuring that every piece meets the same high standards. Additionally, cylindrical grinders are capable of automating the grinding process, which improves efficiency and reduces the potential for human error.
Conclusion
Cylindrical grinding machines are indispensable tools in many industries that require precision and high-quality surface finishes. From automotive and aerospace manufacturing to tool and die production, these machines play a critical role in ensuring the accuracy and performance of components. With their ability to handle complex geometries and tight tolerances, cylindrical grinders help produce parts that meet the most demanding specifications.
As industries continue to evolve and the demand for precision increases, the role of cylindrical grinding machines will only become more significant. The advancement of technology, particularly in CNC cylindrical grinders, will further enhance their capabilities, allowing manufacturers to produce even more precise and efficient components.
FAQs About Cylindrical Grinding Machine
What is the primary use of a hydraulic cylindrical grinding machine?
A hydraulic cylindrical grinding machine is primarily used for grinding cylindrical parts with high precision and smooth surface finishes. These machines are ideal for manufacturing parts like shafts, crankshafts and camshafts in industries such as automotive, aerospace and heavy machinery.
How does CNC cylindrical grinding improve manufacturing processes?
CNC cylindrical grinding machines enhance manufacturing by offering automated control over the grinding process. This leads to high repeatability, tight tolerances and the ability to produce complex parts with minimal human intervention. This increases efficiency and consistency in production.
What industries benefit most from cylindrical grinding machines?
Cylindrical grinding machines are crucial in industries such as automotive, aerospace, tool and die manufacturing, precision shaft production and bearing manufacturing. These sectors require high accuracy, tight tolerances and superior surface finishes, all of which are achievable with cylindrical grinding machines.
Why is surface finish important in cylindrical grinding?
Surface finish is crucial in cylindrical grinding because it impacts the performance and longevity of the component. A smooth surface reduces friction, wear and heat buildup, ensuring that parts function efficiently and reliably, especially in critical applications like aerospace and automotive engines.
What is the difference between universal cylindrical grinders and high-precision cylindrical grinders?
Universal cylindrical grinders are versatile machines capable of grinding various types of parts with a wide range of sizes. High-precision cylindrical grinders, on the other hand, are specifically designed to achieve extremely tight tolerances and smooth surface finishes, making them ideal for highly demanding applications in industries like aerospace and medical device manufacturing.