Monthly Archives: April 2014
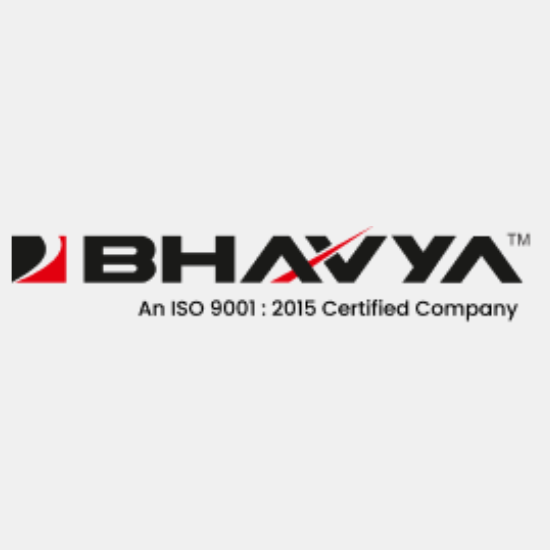
The Vertical Machine Center – Advanced Milling Techniques that Deliver High Quality Workmanship
Milling requirements have been changing in accordance with the industrial requisites. There are innovations made in milling specifications and vertical center is one among them that is suitable to obtain rigid and flexible milling in fragile work materials. Development of…
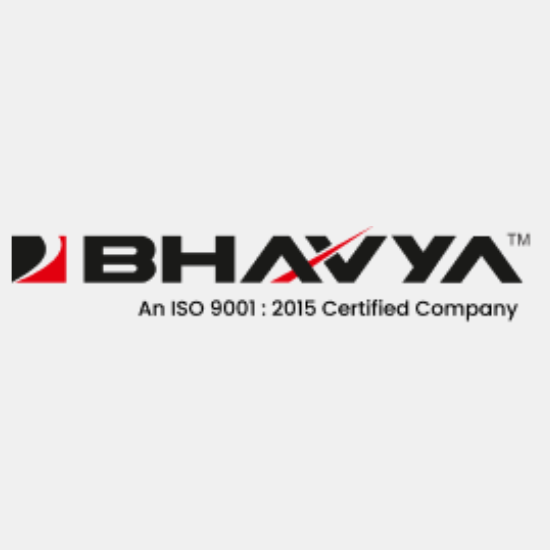
The Drill and the Grinder – Indispensable Equipment in the Machine Tools Industry
Simple grinding operations to work on smaller to medium size work piece materials can be done with the help of compact grinding and drilling equipments. We provide grinding compact grinding equipments which can be applied for drilling and grinding as…
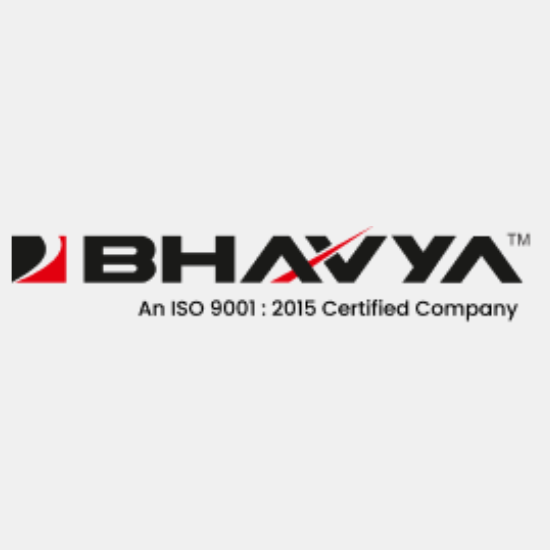
Powerful and Durable Welding Equipment for Fabrication
Welding is of different sorts and it starts from minute to higher level operations. We present powerful and durable equipments of various types that can be used for fabrication works. Flexibility and Portability of Table Mounted Spot Welding Spot welding…
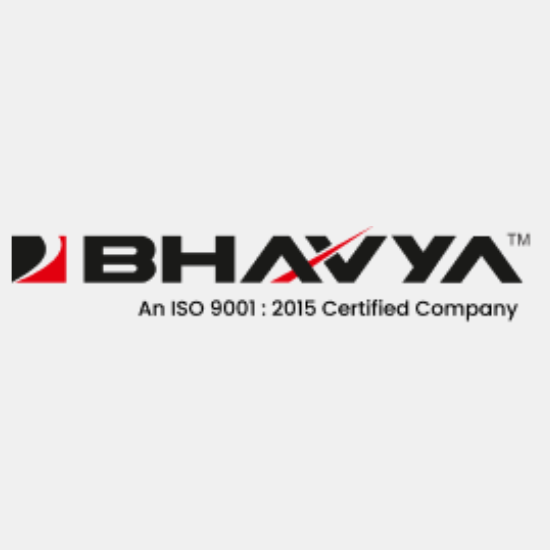
Best Features Provisioned in Imported Lathe Machines
Lathe machines are considered prominent component in majority of workshops. When it comes to machining with specific functionality it stays the right choice. We provide at reliable standards. Our device are made of high grade materials and are designed…
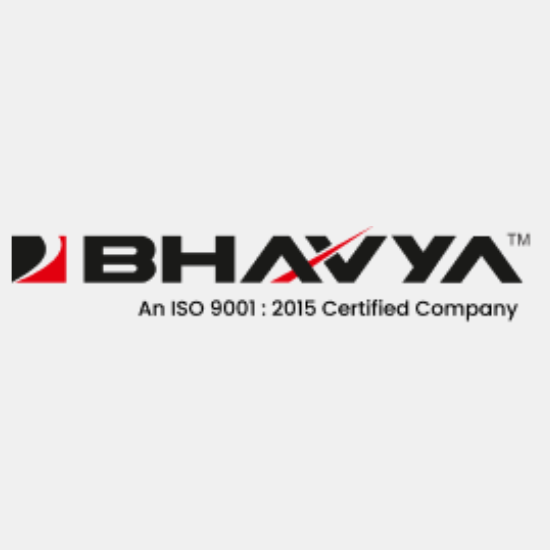
India is Growing as Global Hub in the field of Manufacturing Machine Tools
Machine tools manufacturing Industry is a very planned and important industry today. Indian manufacturing industry has grown many fold be it automobiles, aerospace, defense, electric machinery. For a country to progress, to become influential it must progress in technology. Today…
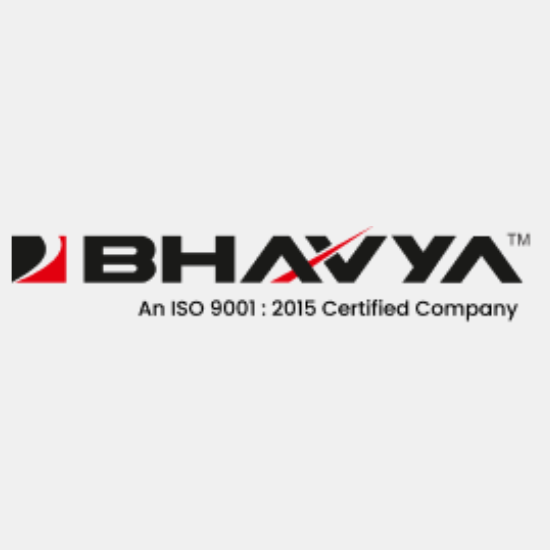
All About CNC workshop Machineries
Automated Operation Features in Workshop Machineries Machines that are applied to carry out critical core engineering works are termed as workshop components. These components were in use since several years back; however, with the advent of designing machines with computer…