Monthly Archives: October 2015
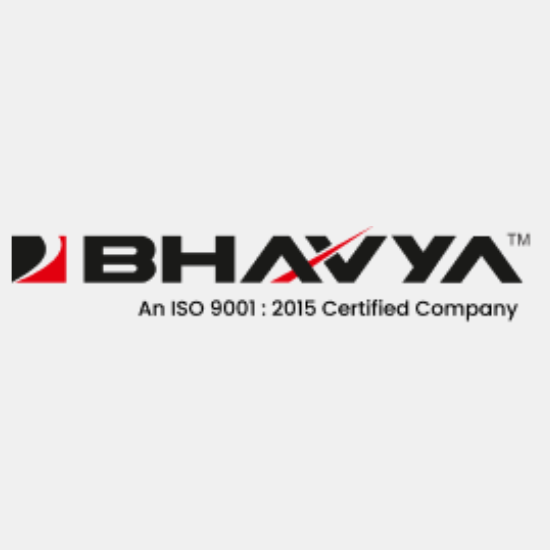
Applications of the Lathe Machine in the Petroleum Industry
The importance of machine tools can never be underestimated industry and one of the most critical of these tools is the lathe machine. The equipment is basically used in shaping metallic pieces such as tubes, engine shafts, bolts and nuts.…
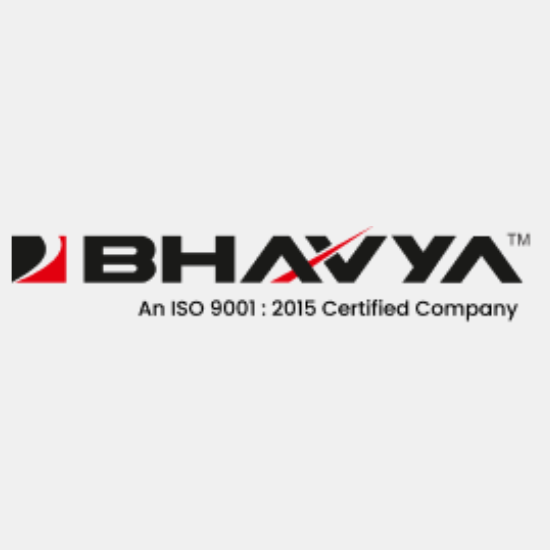
How Industrial Efficiency and Bulk Productivity can be Achieved?
Research and development has led to the availability of many new and better products across many industries throughout the world. This has resulted in designing and producing a vast range of innovative machinery including tool room units for the local…