CNC hydraulic press brakes are an integral part of modern manufacturing in various industries, including HVAC, automotive and electrical cabinet production. These machines provide a high degree of precision and efficiency, making them essential in creating the metal components that are fundamental to each of these sectors. In this guide, we will explore how CNC hydraulic press brakes are used in HVAC, automotive and electrical cabinet industries, delving into their roles, applications and importance in these fields.
What is the Role of CNC Hydraulic Press Brakes in the HVAC Industry?
The HVAC (Heating, Ventilation and Air Conditioning) industry requires high-quality metal components, such as ductwork, ventilation covers and HVAC system frames, which must be fabricated to precise specifications. CNC hydraulic press brakes play a pivotal role in the creation of these components, providing a precise and reliable method for bending sheet metal.
Bending Ductwork and Metal Panels
One of the most common applications for CNC press brakes in HVAC manufacturing is the fabrication of ductwork and metal panels. These components often need to be bent into complex shapes and angles to fit the specifications of HVAC systems. The CNC hydraulic press brake allows manufacturers to achieve highly accurate bends, ensuring that ducts fit perfectly and panels are aligned with the system’s design.
Additionally, these machines can handle a wide range of materials, from aluminum to galvanized steel, making them versatile for HVAC manufacturers who need to process different metal types. The use of CNC technology in this process also ensures that each component meets the necessary dimensional tolerances, allowing HVAC systems to be assembled efficiently and effectively.
Custom Shaping of HVAC Components
HVAC systems often require custom-built components that need to fit into unique or constrained spaces. CNC press brakes offer the flexibility to create these custom parts, bending metal sheets to precise measurements based on the design requirements. The automated nature of CNC press brake systems also means that manufacturers can replicate the same custom designs across multiple units, ensuring consistency in production.
What is the Role of CNC Hydraulic Press Brakes in the Automotive Industry?
The automotive industry demands precise, high-performance metal components that are critical for vehicle safety, structure and functionality. From the chassis to body panels and interior parts, automotive manufacturing requires high-quality metalwork that must meet stringent industry standards. CNC hydraulic press brakes are key to achieving the precision and consistency required in the production of these automotive parts.
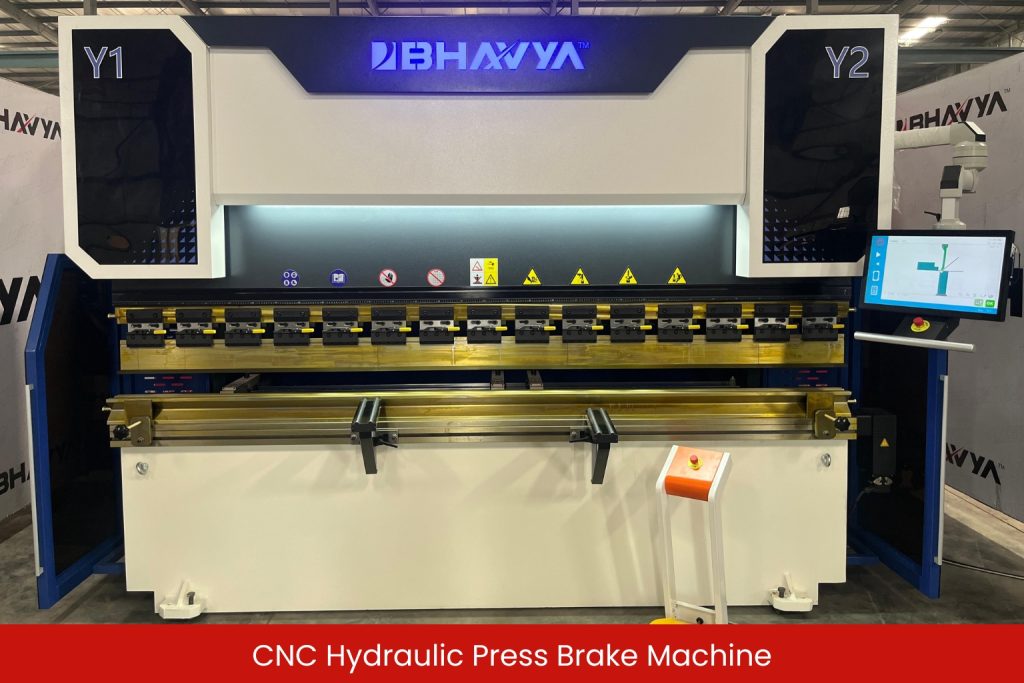
Forming Automotive Sheet Metal
In automotive manufacturing, CNC press brakes are used extensively to form sheet metal components for vehicles. The press brakes bend large sheets of metal into the exact shapes needed for car frames, body panels and other structural parts. Precision is crucial in automotive manufacturing, as each component must fit together perfectly to ensure the vehicle’s performance and safety. With CNC hydraulic press brakes, manufacturers can achieve the required precision without the need for manual adjustments, reducing human error.
In addition to large components, these machines can also handle smaller, more intricate parts, such as brackets, reinforcements and interior fittings. Their versatility makes them essential in the production of both major automotive components and smaller, detailed parts that contribute to the overall functionality of the vehicle.
High-Volume Production of Automotive Parts
CNC hydraulic press brakes support the high-volume production needs of the automotive industry. These machines are capable of operating continuously and efficiently, producing a large number of parts in a relatively short amount of time. This is especially important in the automotive sector, where mass production is a standard requirement. With CNC press brake machine, manufacturers can produce components in high quantities while maintaining the same level of precision for each part.
The ability to program CNC machines for specific bending sequences also allows manufacturers to optimize the production process. This means that automotive parts can be produced with minimal setup time, enabling manufacturers to increase throughput while maintaining quality.
How CNC Hydraulic Press Brakes Work in the Electrical Cabinet Industry?
Electrical cabinets house essential electrical components, such as circuit breakers, switches and wiring, in both industrial and commercial settings. To ensure these cabinets are durable and functional, manufacturers must create metal enclosures that meet specific design and dimensional requirements. CNC hydraulic press brakes are vital tools in producing the metal frames and panels used in electrical cabinet manufacturing.
Bending Panels for Electrical Cabinets
The primary role of in electrical cabinet manufacturing is bending metal sheets to form the panels and frames of the cabinets. These enclosures are often designed to house sensitive electrical equipment, so the metal panels must be shaped to precise angles and sizes to fit the components inside. CNC press brakes allow manufacturers to create these panels with exceptional accuracy, ensuring that each piece meets the required specifications.
Electrical cabinet manufacturers use CNC press brakes to bend metal sheets made of materials such as stainless steel or aluminum. These materials offer durability and resistance to corrosion, which are essential qualities for electrical enclosures. The precision of CNC hydraulic press brake machine technology ensures that the metal components fit together perfectly, creating a robust and secure housing for electrical equipment.
Custom Bending for Unique Cabinet Designs
In the electrical cabinet industry, some projects require custom designs to accommodate specific electrical components or to meet unique space requirements. CNC hydraulic press brakes are capable of producing these custom components with ease. Manufacturers can input specific measurements into the CNC system and the machine will automatically adjust to create the desired shape or cutout for the cabinet. This customizability makes It is a valuable tool for manufacturers who work with a variety of designs and specifications.
Whether it’s creating openings for cable entry, forming internal dividers or shaping cabinet doors, CNC press brakes provide the flexibility needed for these specialized tasks. The automation of the process ensures that the parts are consistently produced to the exact dimensions, reducing errors and the need for rework.
How CNC Hydraulic Press Brake Work and Their Role in Precision Metalworking?
Across all three industries – HVAC, automotive and electrical cabinet manufacturing – the role of CNC hydraulic press brakes in precision metalworking cannot be overstated. These machines enable manufacturers to achieve high levels of accuracy when bending metal components, which is crucial for ensuring that each part fits within the overall system or assembly.
The CNC technology used in these machines provides several benefits, including the ability to make adjustments for specific angles, depths and bending sequences. The precision offered by CNC hydraulic press brakes reduces the risk of errors that could affect the functionality or safety of the final product, whether it’s a component in an HVAC system, a part for an automotive vehicle or a metal panel for an electrical cabinet.
Moreover, these machines can handle a wide range of materials, from thin gauge sheet metal to thicker, more robust materials. This versatility makes mini CNC press brakes indispensable in industries where different types of metals are used for various applications.

Conclusion
CNC hydraulic press brakes are integral to the production processes in the HVAC, automotive and electrical cabinet industries. By offering the precision and versatility needed to manufacture a wide range of metal components, these machines ensure that each part meets the required specifications and fits seamlessly into larger systems. In HVAC manufacturing, they shape ductwork and custom panels; in automotive production, they form structural components and body parts; and in electrical cabinet manufacturing, they create precise enclosures for sensitive electrical equipment. The efficiency, consistency and precision of CNC hydraulic press brakes make them a cornerstone in modern metalworking, helping these industries meet the demands of high-quality production.
FAQs About CNC Hydraulic Press Brakes
How does a CNC hydraulic press brake improve the precision of metal parts?
A CNC hydraulic press brake uses computer-controlled programming to ensure that each bend is executed with high accuracy. The machine’s automated adjustments reduce human error, providing consistent and precise results for metal components.
Can CNC press brakes handle different types of metals?
Yes, CNC press brakes can be used to bend a variety of metals, including aluminum, stainless steel and galvanized steel. The machines are versatile enough to accommodate different material types, making them suitable for various applications.
What types of components are commonly produced using CNC hydraulic press brakes in the HVAC industry?
CNC hydraulic press brakes are primarily used in the HVAC industry to fabricate components such as ducts, ventilation covers and custom metal panels that are required for HVAC systems.
How are CNC press brakes used in automotive manufacturing?
In the automotive industry, CNC press brakes are used to bend sheet metal components for vehicle frames, body panels and other structural elements. These machines provide the necessary precision to meet automotive safety and performance standards.
What is the role of CNC press brakes in electrical cabinet production?
In electrical cabinet manufacturing, CNC press brakes are used to bend metal sheets into precise shapes to create the frames and panels of electrical enclosures, ensuring that each component fits correctly and meets design requirements.