A CNC Bending Machine is a machine that automates bending metal tubes or wires. A single machine does the entire process, eliminating the need for a laborer or another machine to feed the metal tube or wire. This process reduces the cost of labor by eliminating manual labor. This machine can also reduce human error, as all operations can be completed by one machine.
Workbench in CNC Bending Machine
One of the key components to the CNC bending machine is the workbench. This is the platform that is used for processing the sheet metal components. It should be made of a durable material that can withstand the weight of bending components. A workbench of less than a few tons is ideal.
In this case, the workbench has three cylinders. One of the cylinders is positioned at the center and the other two on either side. The center one is always parallel to the worktable’s longitudinal axis. This compensation cylinder ensures that the workpiece is bent uniformly. It also improves the straightness of the workpiece. The computer will determine the necessary stroke length for the final bend.
The bending system can also display a 3D picture of the workpiece. It can automatically identify the workpiece, mould, and lathe bed. The bending machine can store up to 2500 programs and 90 dies with its graphical programming system. It also supports ten kinds of memory capacity and can automatically calculate the clamping point, bending pressure, and unloading distance.
The CNC bending machine is usually equipped with a workbench. The workbench and the clamping plate are connected to each other via hinges. The base of the CNC bending machine is equipped with columns. It supports all the components of the machine. The workbench is the platform where workpieces are positioned before the bending process. The workbench is also equipped with a back gauge which is used to position the workpiece properly before the bending process.
Slider Block in CNC Bending Machine
The CNC bending machine has several important features to achieve accurate bending. One of these features is the ability to make variable-radius bends. The interpolated axes system is used for making these bends. Other features of the CNC bending machine include ramps of acceleration, a stop/start function, and inversion and mirror cycles. Another feature of the CNC bending machine is the ability to connect to an external computer through RJ45 (LAN) for automatic setup, diagnostics, or programming. Other features include a USB connection for copying of bending programs, and remote connection for Industry 4.0 readiness.
The slide block for CNC bending machine is a steel plate cylinder that is fixed on both ends of the slider. The block is driven by a hydraulic piston rod. The sliding block is also controlled by a mechanical stop. In addition, the position of the mechanical block can be adjusted through a worm gear and travel counter. The slider is synchronized with the CNC bending machine through a synchronization mechanism using a torsion shaft.
When choosing the bending machine, take into account the amount of precision required. A CNC bending machine is capable of repeatability of up to 1deg, while a manual one requires 0.0004 inches. Also, the quality of the material is important. For example, stainless steel requires a load of 50 percent more than low-carbon steel or soft aluminum. You should check the tonnage tables provided by the CNC bending machine manufacturer.
Gear Pump in CNC Bending Machine
If you find that the Gear pump on your CNC Bending Machine is not working properly, there are several ways to solve the problem. The first step is to inspect the pump and its connection parts. You may find that the ram connection is not tight enough or that the nut between the ram and the cylinder has become loose. Other possible problems include a clogged damp hole, or a stuck cartridge valve. Check the valve for debris, and clean it if necessary.
Another way to check if the Gear pump is functioning properly is to check its clearances. When the clearances between the cog teeth and the casing increase, it reduces the efficiency of the gear pump. The flow slip increases proportionally to the size of the clearance. While this wear is relatively minor at first, it can quickly decrease the performance of the machine.
The other way to check whether the Gear pump on a CNC Bending Machine is working properly is to check the hydraulic oil level. Many CNC bending machines use hydraulic oil, which is a liquid that is continually running during the bending process. The downside of hydraulic oil is that it has a short oil change period and can be very expensive.
The Gear pump on a CNC Bending Machine is an integral part of the machine. It is responsible for bending the pipe. This component is necessary in the production process.
Stroke Adjustment in CNC Bending Machine
The first step in adjusting the stroke on a CNC bending machine is to align the plates with the bottom mold. The upper die should have sufficient clearance and must be positioned with enough angle to allow for plate thickness changes. If the plates are not aligned properly, the resulting gap may damage the mold or plate. The stroke adjustment can be performed either manually or electronically.
After selecting the desired angle, the CNC bending machine calculates the required length of the final stroke. The two rotating bending bolds give a signal to the computer that determines the final stroke. The system compensates for the spring back effect of bends and achieves an angle accuracy of 0.2o. This reduces material waste and improves precision.
A CNC bending machine can be programmed to be set at several different angles. The angle of the stroke is defined by calculating the bending force and the upper and lower molds. In some cases, the relief valve needs to be adjusted to ensure that the force is greater than the folded plate. It is also important to note that the angle of the stroke should be adjusted according to the actual situation. The bending notch must be positioned to the required angle.
Open height is the distance between the bottom of the upper beam and the top of the lower beam when the press is fully opened. It can be a critical factor in the selection of tooling. This measurement is crucial when bidding on contracts or ordering tooling. If you do not know the correct open height, you can cause major problems with the application.
Backgauge Adjustment on CNC Bending Machine
To perform Backgauge adjustment on a CNC bending machine, you need to adjust the axes of the machine. In general, there are three axes that are adjustable: the X-axis, Z-axis, and the variable speed point. Each axis has a different range of backgauge adjustment and can be adjusted independently of one another.
The first step in backgauge adjustment is to establish the center of the bend. The nose of the punch establishes this center, but if the bend is more than 90 degrees, the bending line needs to be adjusted accordingly. After doing this calculation, the next step is to measure the width of the die body from the front. You should include one-half the width of the die body for the backgauge adjustment.
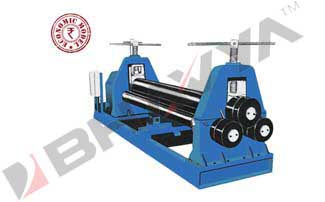
Another step is the back gauge distance adjustment, which is used to position the sheet along the length direction during the bending process. The machine will have a hand wheel that you can turn to fine-tune the backgauge to the right or left. In addition, CNC bending machines often have an electric quick-adjustment lever for the backgauge.
The backgauge adjustment of a CNC bending machine allows for the machine to reach the desired bending angle. It also enables the machine to achieve slide-down, jog, continuous, pressure-holding, and halfway stops. The machine also has the ability to complete multiple bends with the same angle or different angles.
Maximum Length of Component that can be Bent on CNC Bending Machine
The maximum length of a component that can be bent on a CNC Bending Machine depends on the length of the press brake bed and the thickness of the material being bent. The maximum thickness of a component is determined by its tensile strength and the tonnage available. For larger sheet metal components, the bend radius can be increased by using a larger bottom V block.
A CNC bending machine has the advantage of multi-radius and multi-strack designs. This feature facilitates rotary draw-bending and free-form bending. Its accuracy is extremely high, with tolerances of 0.05 mm and 0.05 degrees.
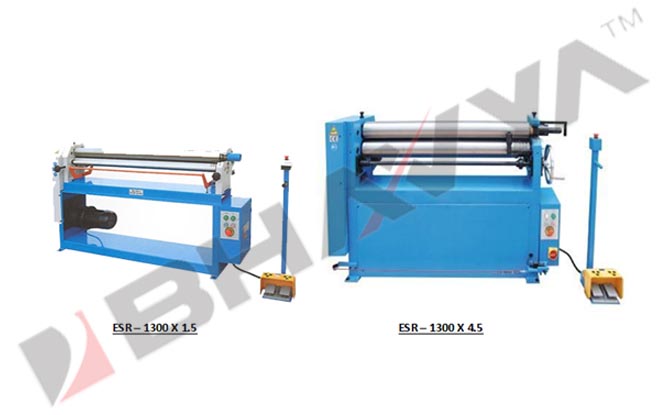
The maximum length of component that can be bent on a CNC Bending Machine depends on the material, tooling, and processing requirements. In general, +/-1 degrees are acceptable. In addition, the flange length must be at least four times the material thickness. The maximum bend radii are dependent on the material and the application, as lower bend radii can lead to material flow problems and fracturing. In addition, localised necking may occur.
A CNC Bending Machine can be used to bend components in batches. However, the process can be tedious and costly if the components are too long. Consequently, short bending lengths are more cost-effective. The machine’s tonnage is also dictated by the length of the component that can be bent on it.