A press brake machine is a type of mechanical device which helps to prevent a part from being bent, which means the machine can be used for pressing the end of a piece of material. There are several types of press brakes including servo-electric and hydraulic. There are a number of jobs that are associated with these machines, so if you want to work in the industry, you’ll have plenty of opportunities.
Hydraulic Press Brakes
Hydraulic press brakes are used for various purposes. They are widely used in the manufacturing industry to produce sheet metal parts by bending them. They are reliable and safe, unlike the flywheel-driven presses.
This type of press is a cost-effective bending process. It produces accurate, high-quality products.
The machine can be operated manually or automatically. The operator steps on the foot pedal to begin a bending cycle. The press brake can be set for a variety of angles. It can also be adjusted to compensate for deflection.
It is important to maintain the proper oil level in the pump. The hydraulic fluid enters the system via an air inlet valve. It then flows to the drain through a bail hose.
The press brake is designed to be vibration-free. It can work with heavy loads. It can be used for stripping, painting and lifting. It can be made of different materials depending on the application. Its components are generally made of bronze and steel.
Servo-driven systems have been used in punching and laser cutting for a long time. This allows for a more accurate bending process. However, they are usually used for lower tonnage applications.
There are many manufacturers of hydraulic press brakes. They offer a wide range of sizes, styles, and types. They are available for both hydraulic and electric models. The most reliable models have on-screen help and training buttons.
In addition, they offer robust Human Machine Interface (HMI) that reduces programming time. It offers 3D bend simulation, precise control of auxiliary components, and tool storage. It can help operators make accurate bends.
These are ideal for manufacturing operations. The company’s product quality can improve. Its price can be reduced by reducing labor rates.
These presses are designed to be durable and to withstand a variety of different materials. The machines can be customized according to customer requirements. The designs are available in 2, 2.5, 3 and 4 meter dimensions. The use of hydraulic press brakes has helped to shape the sheet metal industry. It is now possible to produce almost any shape of metal.
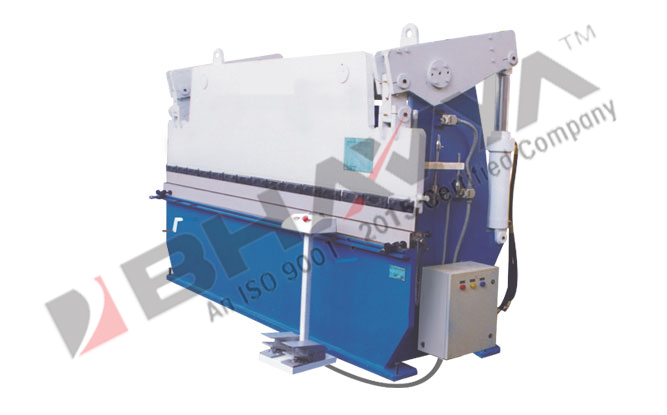
Mechanical Press Brakes
There are many different types of press brakes to choose from. They can be used in a wide range of applications from interiors and furniture to architectural metalwork.
One of the most common uses for press brakes is in sheet metal forming. For this purpose, a mechanical or hydraulic ram is attached to the workpiece and is pushed to form a curved shape.
There are two main types of presses. The first is the hydraulic. In a hydraulic press, a piston is mounted in the press and acts as a pump. The piston is a bit larger than the ram, which creates a higher mechanical force. This is good for bending thick steel. However, hydraulic presses are slower than their counterparts.
Another type of press is the pneumatic. This type is faster than hydraulic presses, but has a lower tonnage limit. In this case, a compressed gas is fed into the cylinders. The potential pressure that this produces is what drives the ram down onto the material.
There are also a variety of other types of press brakes, including those for bending metal sheets, and those that are designed to form a variety of shapes. For example, a servo-electric model utilizes an electric motor to drive the ram, while a hydraulic press uses a piston and hydraulic fluids.
A press brake can also be integrated with other equipment, including cutting and joining equipment, to produce a finished product. For example, a press brake can be used to create a curved fender for a car.
For the most part, press brakes are manually operated. Some machines have tools that can be programmed to help with a variety of different tasks, such as setting the bend direction, positioning the material, and creating a graphical representation of the finished product.
For most people, a press brake is an indispensable piece of machinery. But not all of them are created equal. So, it’s important to know what to look for when choosing a machine. The best press brake for your needs will depend on the job in hand.
Job Description for an Operator
A Press Brake Operator is an expert on the use of press brakes, which are used to bend metal, plastic, and structural steel. They are responsible for ensuring that the work is done according to specifications. They may also be responsible for troubleshooting issues with machines.
Most employers seek to hire employees with previous manufacturing experience. They want their workers to be experts in the use of press brakes. They also require that the operators are familiar with safety regulations. They might also need their operators to communicate with other employees. Some companies prefer to have their operators have an associate’s or bachelor’s degree.
Press Brake Operators need to be adept at interpreting blueprints and sketches. They must also have an eye for details. A Press Brake Operator’s job description includes completing the layout, fitting the structural steel, and configuring the bend allowances for sheet metal. They are also required to maintain raw material stocks and follow safety standards.
Press Brake Operators are responsible for maintaining the cleanliness of their machine and tooling. They also inspect the manufactured parts for quality problems. They are usually monitored by shift supervisors.
Press Brake Operators must be skilled at operating machinery, troubleshooting, and resolving emergencies. They may also be responsible for matching customer specifications. They are also trained to operate automated systems.
As automation advances, the need for press brake operators will be limited. Some industries are investing in more advanced equipment, which will reduce the need for these types of workers.