A centerless grinder is a precision machine that produces a wide variety of parts, with superior accuracy and ease of operation. The ability to hold extremely close tolerances is a distinct advantage of this technology. Compared to conventional grinding machines, a centerless grinder is more effective for smaller job lots and shops with lower manufacturing costs. However, before purchasing a centerless grinder, be sure to research the machine’s capabilities. Here are a few important tips for selecting the right model:
Features of Centerless Grinder
The centerless grinder features fewer moving parts than other grinding machines, making it an excellent choice for parts requiring tight tolerances. A centerless grinder is ideally suited to finishing the outside diameter of small, cylindrical metal parts, and it is easy to use even by inexperienced workers. The process begins by pushing the workpiece into a regulating wheel. The regulating wheel, which operates at a slower speed than the grinding wheel, holds the workpiece in place as it rotates. The regulating wheel also determines the actual grinding speed.
Why Choose Centerless Grinder?
Unlike other grinding methods, the centerless grinding method is highly accurate and requires very tight tolerances on the OD. OD size, roundness, and high and low frequency lobe patterns must be within tight tolerances. This type of machine is often used for low-volume production and is economical to run. It can also produce very small parts in high volume. Regardless of the application, centerless grinding is an excellent choice for small-to-medium-sized jobs.
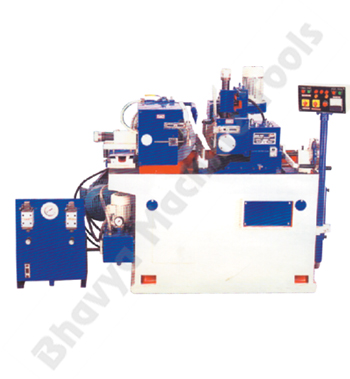
Benefits of Centerless Grinder
The centerless grinding process is highly accurate and precise. OD size, roundness, and lobe patterns must be tightly controlled. Throughfeed centerless OD grinding is an excellent option for parts requiring precise tolerances at an affordable processing cost. Unlike conventional methods, centreless grinding is also an effective solution for high volume production. It also offers ease of use for smaller batches. This feature of the centerless grinder makes it a preferred choice for small-scale manufacturers.
Types of Centerless Grinder
The two types of centerless grinders are end-feed and in-feed. The former involves feeding the workpiece into the machine and the latter is the best option for irregularly shaped workpieces. The end-feed method is ideal for tapers, while the in-feed method is good for cylindrical shapes. With centerless grinding, the workpiece is kept concentrically between the grinding wheels. In-feed grinding is more convenient and a better option for large-scale production.
In Conclusion
There are many advantages of centerless grinding. It is fast and can be used by less experienced individuals, and has a high rigidity. It is also easy to operate and produces high-quality output. The downsides of a centerless grinder include the need for fixturing and the need for long tool changes. Whether you need a large-scale production, or a small scale production, centreless grinding is the way to go.
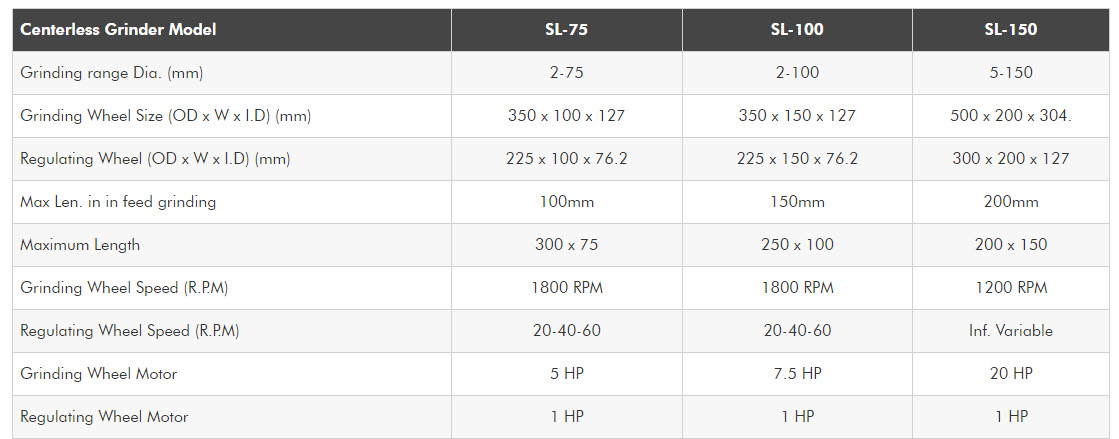