Monthly Archives: November 2012
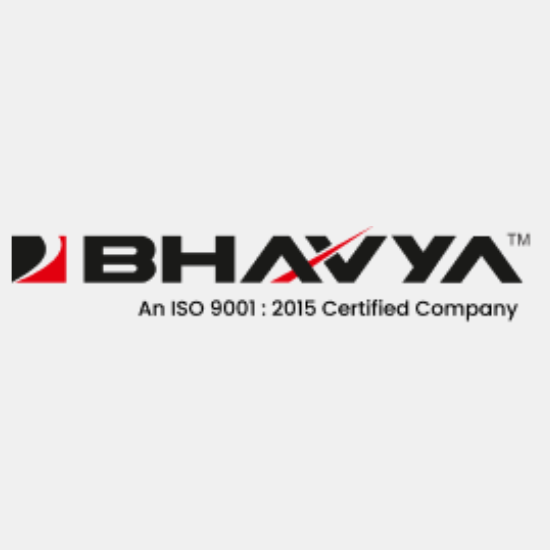
Types of Workshop Machinery Which can Enhance Efficiency and Productivity
These days, a variety of workshop machines are readily available in the market. Following are the different types which can enhance efficiency and productivity. A shaping machine is an exceptional workshop unit that is generally applied to shape flat or straight metals…
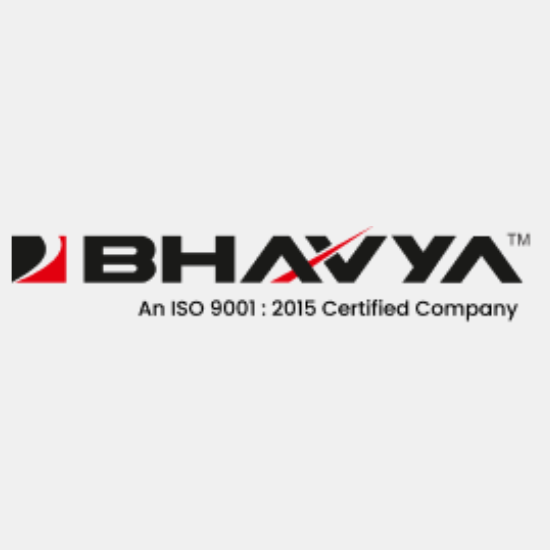
Things to Know Before Buying Sheet Metal Machinery
A sheet metal machine is used to cut, press, bend and form sheet metal into various shapes and sizes. These help to easily, quickly and effectively; perform a wide range of tasks, such as cutting, stamping, bending, perforating, ironing, spinning,…
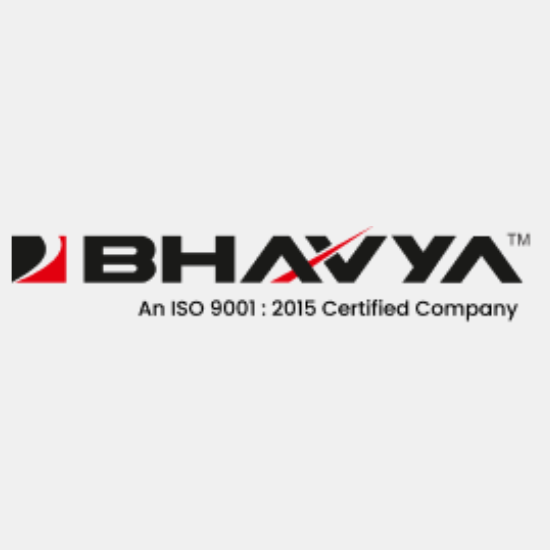
Mechanical Press Brake V/s. Hydraulic Press Brake – Which One is Better?
These days, various types of press brakes are available in the market, including mechanical and hydraulic. The main differences between a mechanical and a hydraulic is as follows. Hydraulic press brakes are simple to use and versatile for punching and…
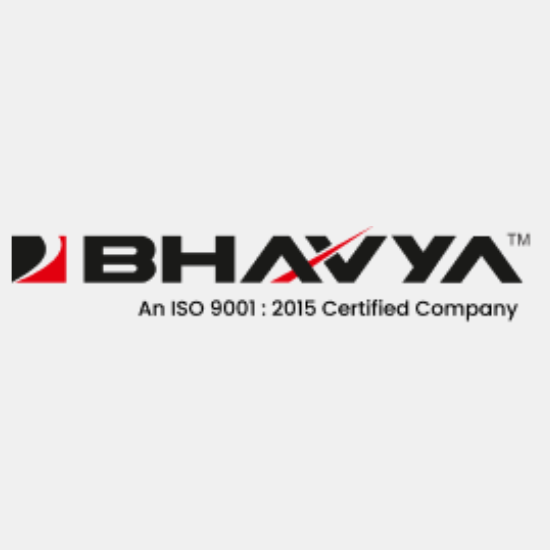
The Most Important Machine Tools Required in Any Workshop
The most important tools required in any workshop, nowadays are described below. Milling Machines The milling machine is used for milling, cutting, shaping, carving, planing, contouring, drilling, stamping, and die-sinking a variety of solid materials. The work piece is positioned, to…