Monthly Archives: March 2013
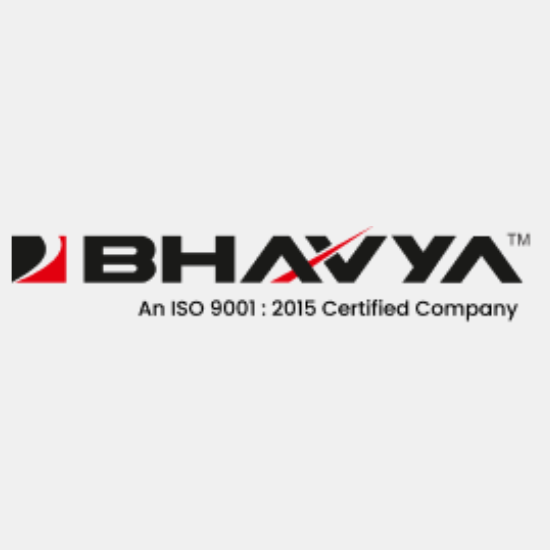
Industrial Applications of Different Sheet Metal Machineries
Metals play an important part in our lives today. Think of any object around us and either it is made of metal or some part of it is of metal. Metals are an integral part of our lives today. A…
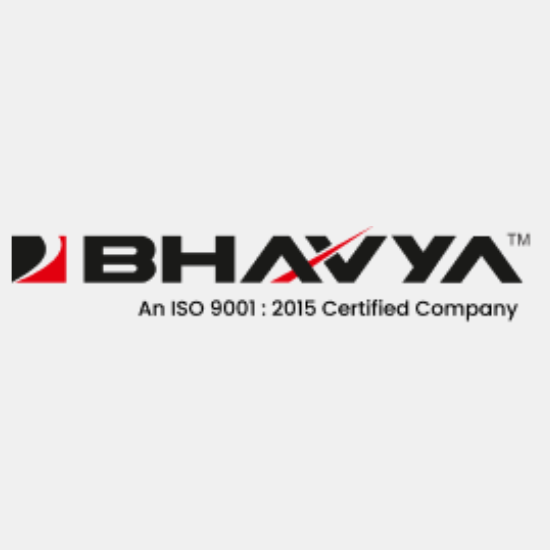
C Type Power Press – An Efficient Machine Tool for Different Industrial Applications
A number of items are made from a variety of metals. Different techniques and equipments are used to give shape to these hard and soft metals. To bend and give different shapes to hard metals special tools are used in…
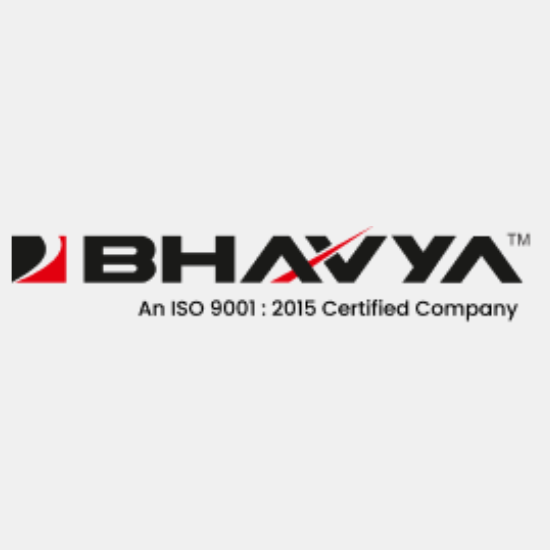
Woodworking Machinery – Efficient Solution for Wood Shaping Applications
Woodworking machinery or tools are used to cut, carve or shape wood. A tool with a motor reduces the work of the operator and increases the production. In a wood processing business these are craft the desired shape or dimensions from…
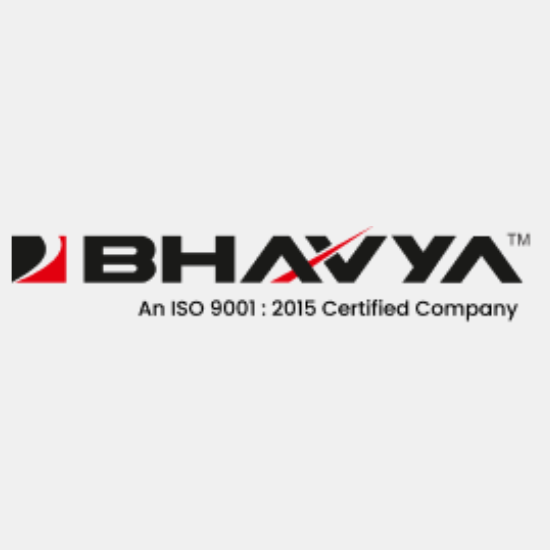
Significance of a Press Brake in Metal Cutting Applications
A number of machines are used in the process of fabrication of sheet metal parts. Fabrication is the process of collective operations which are used to give a shape to the metal sheet. This involves a number of equipments like…
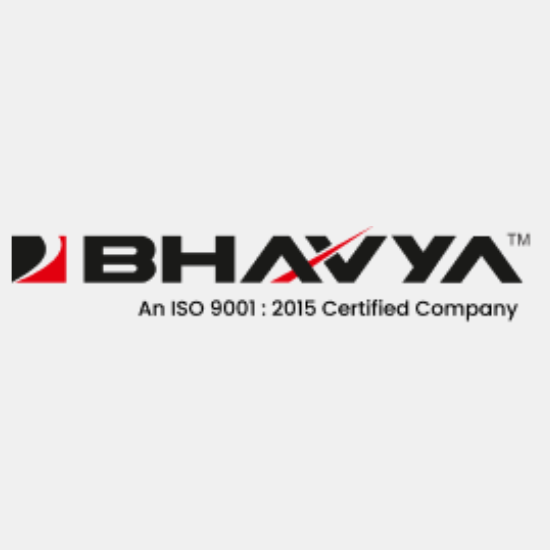
Facts About a Surface Grinding Machine
To give a meticulous smooth finish to the surface, as regards the level, size or finish of the surface of a flat metallic or non-metallic object, surface grinding tools are used. In order to make the surface flat and smooth…
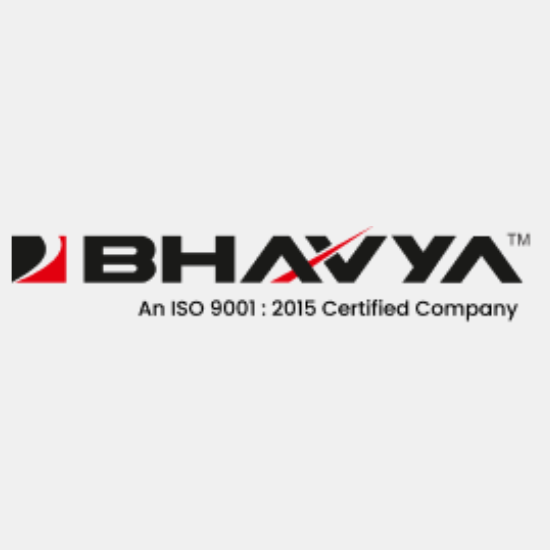
Applications of a Horizontal Bandsaw Machine
A machine that is used for cutting wood, metal, plastic and a variety of materials into straight, curved or irregular shapes is called a horizontal bandsaw. A wide range of bandsaw equipments are available in the market. They are made from cast…
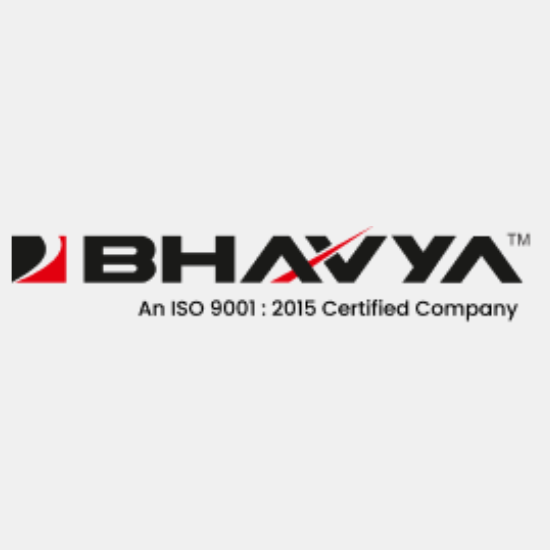
All About a Drilling Machine
Machines make our work simple, reduce the effort and increase the efficiency. It used for holes in a work-piece are known as drilling machines. It is the process of making a circular hole with a rotating cutter, called drill, in…
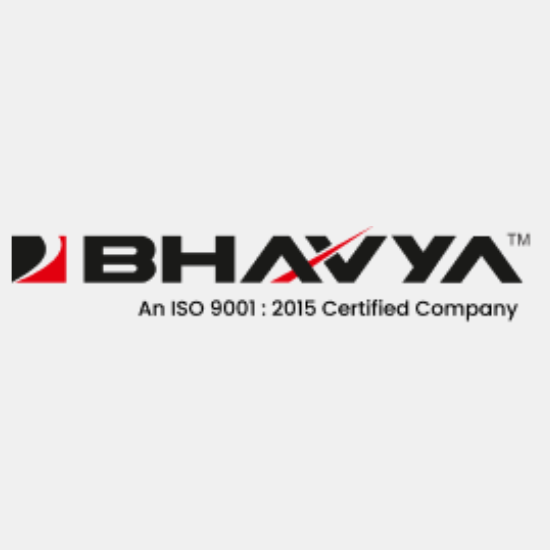
Popular Types of Woodworking Machinery Used in Workshops and Industries
Machines employed in a wood processing operation to cast the desired shape or dimensions from the wood work piece are known as woodworking machine. It may be manual operated or computer controlled machinery. Manual machines are good for the small…