Monthly Archives: March 2014
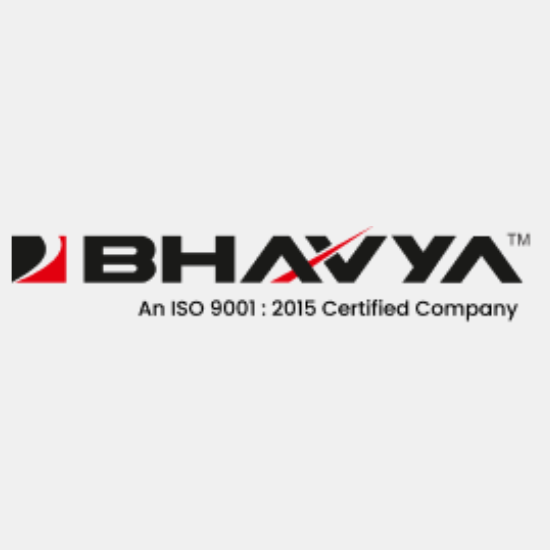
Environment Friendly Features of Press Brake
Machineries, Industry and Environment Industries that depend on machineries remain hindrance to environment in terms of the noise emitted from the industrial premises and the wastes removed. These factors certainly pollute the atmosphere in some way or other. Common Hindrance…
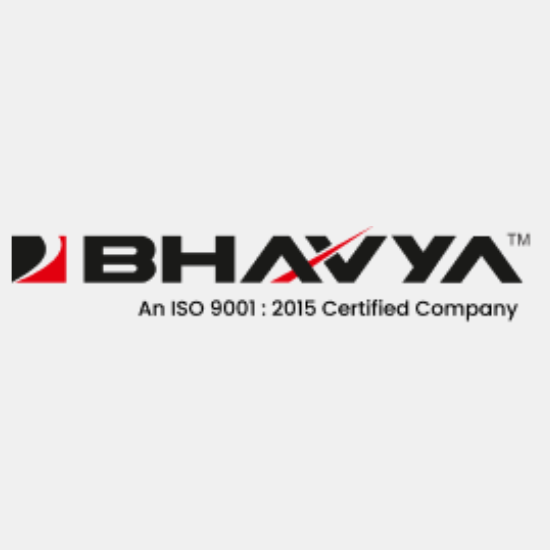
Essential Activities Followed by Machine Designers While Designing Milling Device
Innovations Introduced in Machine Design Unlike earlier days, designers no more need to depend on pencil drawing over graph sheets to bring a new equipment design. It is hard to imagine that tools can be designed with the help of…
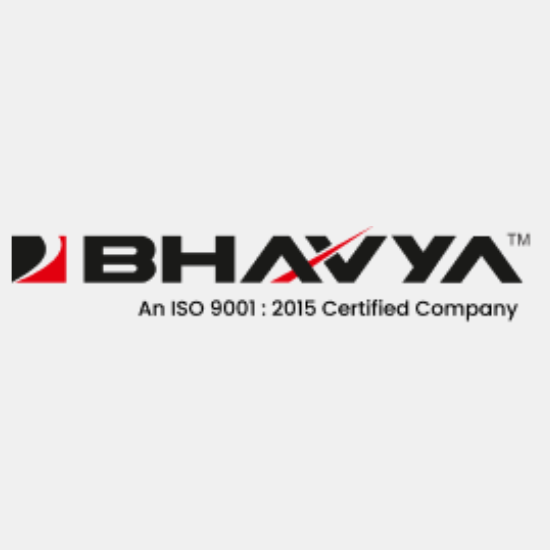
Learn about the Industrial Preference of Bend Angle and Bend Size in Sheet Bending Equipment
One Machine to Handle Variety of Metals Steel, brass, aluminum, copper, etc. these metals can be converted to variety of shapes even when they are existing in varying thicknesses. Important Aspects to be looked for in Sheet Bending Equipment Starting…
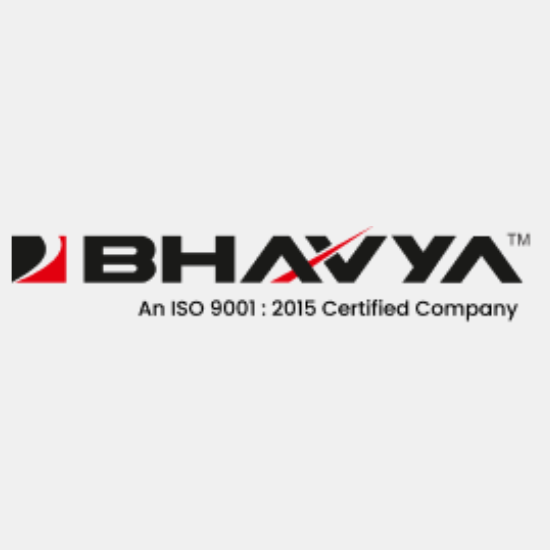
Know About the Self Protection Tips in Operating Bench Type Lathe Machine
Self Protection in Machining Works-A Mandatory Aspect to Consider Workshop machineries are of different sorts and each workshop device performs exclusive machining operations. However, there are risk factors present in working with workshop and lathe device is one among them.…
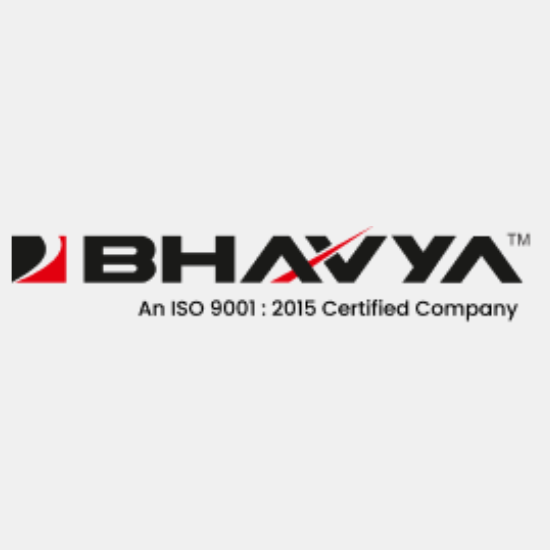
Multiply Your Investment Revenue with CNC Lathe Machine
CNC Lathe for Higher Performance and Productivity CNC lathe is a revolutionary invention for the machining processes. Though this is relatively expensive than bench and table mount models, yet while comparing the performance and productivity. More Productivity in less Timing…