The need for precision machining and tooling became indispensable when computers were first used in factories and later in the machining process itself. The development is further complemented by the growth of aerospace and automotive industries thereby compelling the need for CNC machines to create parts in different shapes and sizes. Computer numerical control (CNC) tool and cutter grinding machines are extensively used for honing tool bits and other machinery. This process produces a more intricate product at faster speeds than conventional machining procedures.
With this technology, it is now possible to cut and grind almost any surface including metal and even ceramics with a high degree of accuracy. A CNC milling machine operates by using computer numerical control to control the operation of a drill or cutter. Instead of manually operating the machine, commands are processed by the computer.
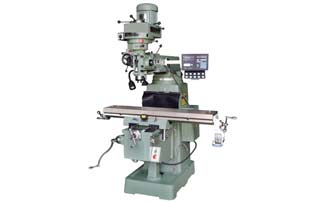
Features of the CNC Tool and Cutter Grinding Machine
One of the unique features of the CNC tool and cutter grinding machine is its multi-tasking capability. Tool and cutter grinding machines are built with several software options that allow users to switch between different functions at the click of a button. These include options for engraving, drilling, turning, etching and others. This allows the operator to perform various tasks simultaneously. This feature has made it very popular among industries as it enables them to work on several projects simultaneously.
Advantage of the CNC Tool and Cutter Grinding Machine
Another unique advantage of this machine tools is their extreme usability. They are designed for universal milling, drilling, turning, grinding, planning and other complex machining operations. They are also ideal for applications requiring extreme accuracy such as tool and die making, air cushion machining, surface roughing, etc. Furthermore, these tools are suitable for EDM (electronic data management) and CAM (Computer Aided Design) processes.
Applications of Tool and Cutter Grinding Machine
Tool and cutter grinding machine parts vary according to their specifications and application. For example, a diamond abrasive wheel may be used in abrasive milling and cutting in order to increase the grinding speed of CNC equipment. Alternatively, there are different types of abrasive wheels such as high carbon alloys and carbon black. A grinding machine part that may come in a variety of sizes and specifications to meet varied customer needs.
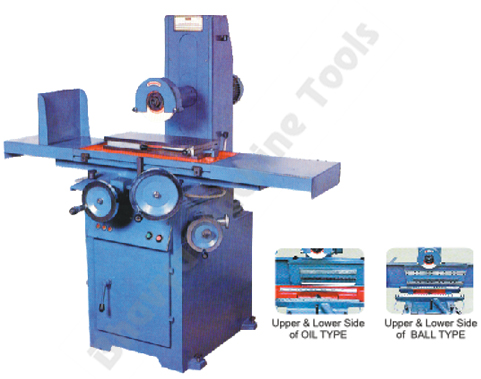
In general, CNC grinding machines use a cylindrical table for performing various machining operations. Usually a rotary table is attached to the machine so that it can rotate freely. However, CNC grinding machines may also use a linear table which may not rotate freely due to its fixed nature. The stationary types are usually used for cutting and sanding in work pieces while the mobile ones are used in the cases where accuracy and mobility are essential. In addition, both types of these machines are capable of providing high levels of precision.
Specifications of Tool and Cutter Grinding Machine
Tool and cutter grinding machines are made of a variety of materials including steel, aluminum alloy and even titanium. Some machines use a single piece of steel, while others are capable of using multiple pieces of steel. Regardless of the type of material used, the end result should always be durable and reliable. This is why manufacturers make sure that their machines are designed properly to ensure that they will last for a long time. They do this by ensuring that all machining parts are made out of the best possible material that has been approved by the manufacturer.
The Bottom Line
Tool and cutter grinding machines are manufactured and set up for specific purposes. In the case of CNC surface grinding, for example, the tool and die bed situated above the chuck perform grinding operation. There are different types of grinders suitable for different jobs. These are the reason why it is necessary to ask a lot of questions when you are buying your grinder so that you get the one that works best with your requirements.