Monthly Archives: February 2014
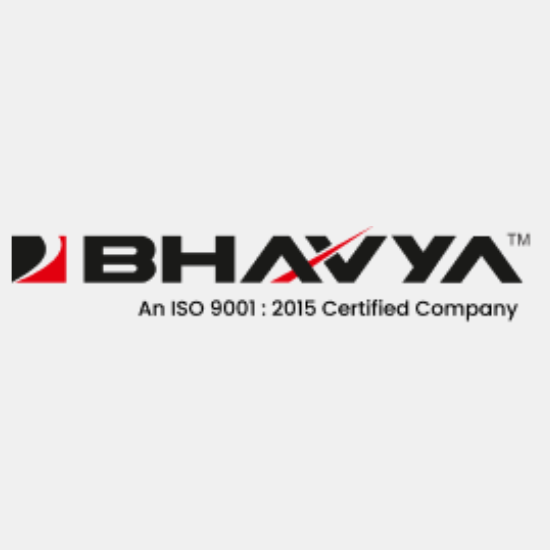
Perform Mechanical Operations on Sheet Metal Faster and Accurately Using Specially Designed Sheet Metal Forming Machines
Capitalize on your return and enhances production efficiency using sheet metal forming tools. These are well designed in ensuring efficiency accuracy and increases the mechanical performance in the metal forming industries. It is constructed with high quality materials enabling it…
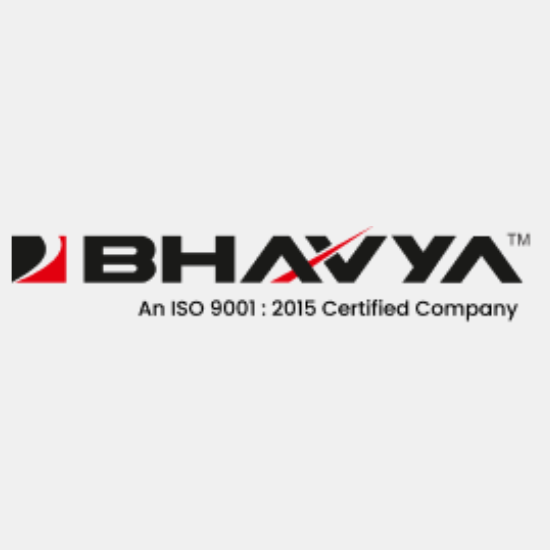
Cut Metal Work Pieces Faster and to High Precision Using Hydraulic Hacksaw Machines Tools
As the production metal cutting volume increases in the industries the hydraulic hacksaw tool offers the solution to accuracy and efficient metal cutting. The skilled and professional manufactures of hydraulic hacksaw equipments have manufactured high superior quality and durable for…
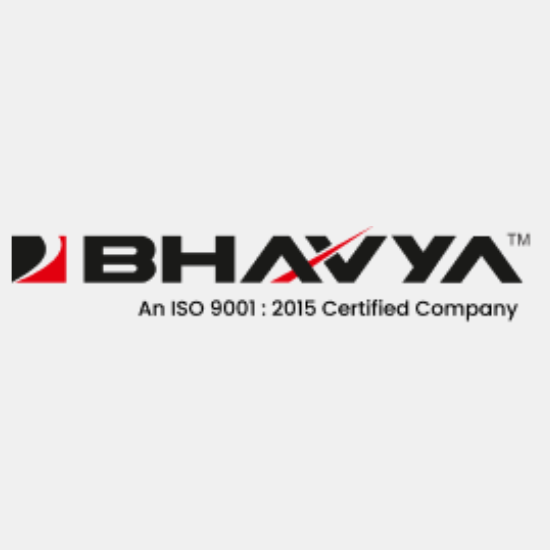
Use Boring and Honing Machines to Drill and Enlarge Holes on Work Pieces with Accuracy and Precision
Honing and boring operations are some of the most common finishing operations done on drilled parts and other hollow components. The two operations are widely used in engine block finishing. Honing and boring operations in workshops This operation entails the…
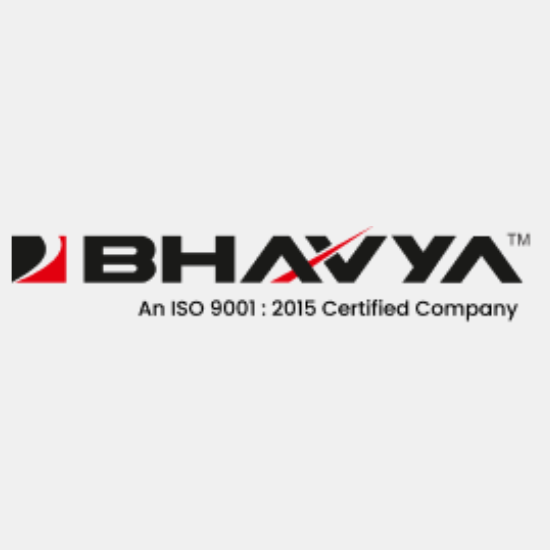
Perform Machining Operations Much Faster Using Specialized Lathe, Planning Machines, Gear Hobbing and Threading Machine Tools
As production volumes in industries increase various tools have been developed to handle complicated functions and heavy loads. These specialized tools include: threading and gear hobbing machines. Features and Industrial Applications of Capstan and Vertical Lathe Machines Capstan lathe are…
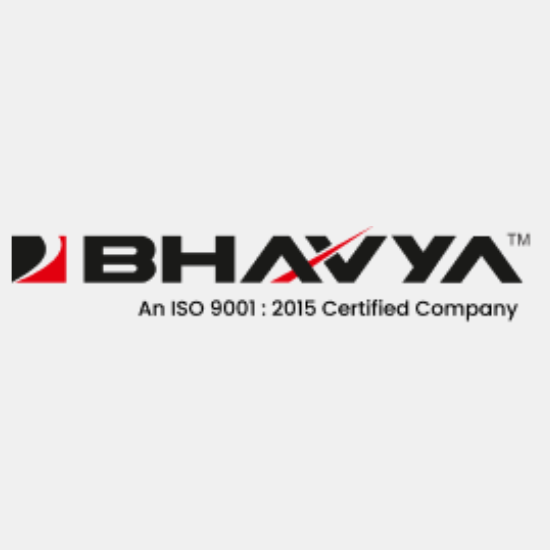
Cut Large Quantities of Sheet Metal Accurately and Effectively Using Manual and Hydraulic Powered Shearing Machines
Manual and hydraulic powered machines are most effective and accurate in cutting as they are used in fabricating and sheet metal machine operations. They are excellently designed in withstanding large loads makes work easier, cost effective and is more efficient.…
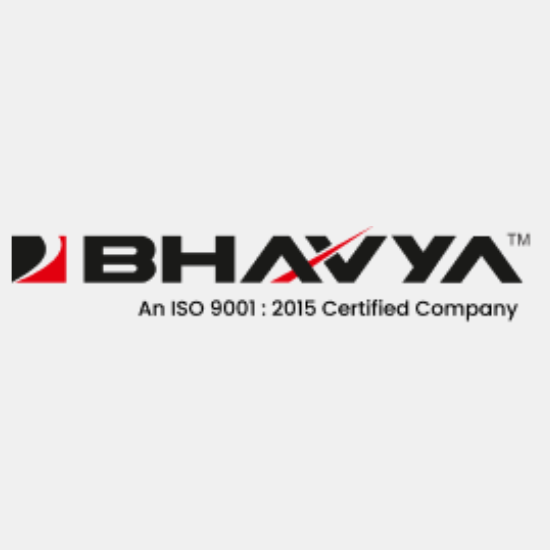
Woodworking Machinery
Bhavya Machine Tools is a pioneer is supplying workshop equipments to handle variety of machining jobs. Starting from drilling operation to cutting, shaping, surfacing, molding, etc it is the right place to search the precise machinery. Apart from traditional manually…
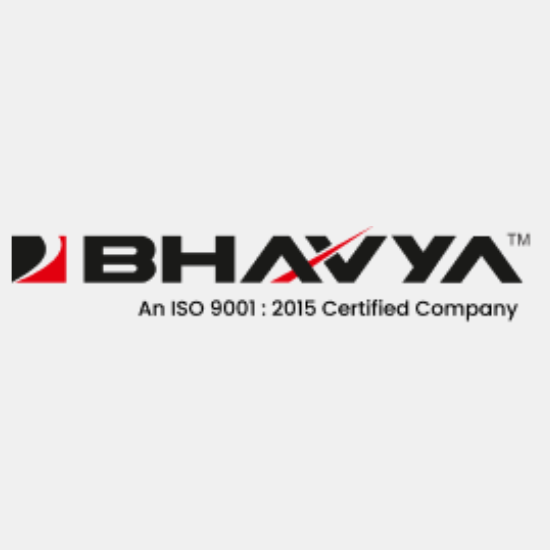
Safety Norms for Workshop Machinery
Bhavya Machine Tools is a leading supplier of work shop equipments suiting wide range of industries and as far as wood working machinery is concerned, they manufacture and supply plenty of wood working devices to handle different aspects of wood…