A lathe machine is one of the most important tools in manufacturing, offering precise control over the shaping and finishing of various materials. With its versatility and ability to create highly accurate parts, it is widely used in industries such as automotive, aerospace and metalworking. In this comprehensive guide, we answer the most common questions related to lathe machines to help you understand how they work, their types and how to select and maintain them.
What is a Lathe Machine and How Does It Work?
A lathe machine is a tool used in manufacturing for shaping and machining materials like metal, wood and plastic. It works by rotating a workpiece on a spindle while a cutting tool is applied to shape it into the desired form. The lathe machine is essential for creating cylindrical shapes such as shafts, pipes and bolts.
Here’s how it operates:
- Workpiece Rotation: The material is mounted on a rotating spindle.
- Tool Movement: A cutting tool, which moves along different axes, is applied to the rotating workpiece.
- Shaping: The cutting tool removes material to create the desired shape and finish.
Lathe machines are fundamental in producing symmetrical and complex components with high precision. They are used for turning, drilling, threading and facing operations.
What are the Different Types of Lathe Machines?
Lathe machines come in various types, each designed for specific applications. Here are some of the most common types:
Engine Lathe
This is the most commonly used type of lathe in general machining. It is versatile and can be used for turning, facing and drilling operations.
CNC Lathe
A Computer Numerical Control (CNC) lathe automates the machining process. It uses a computer to control the movement of the cutting tool, offering high precision and repeatability. CNC lathes are ideal for mass production and complex designs.
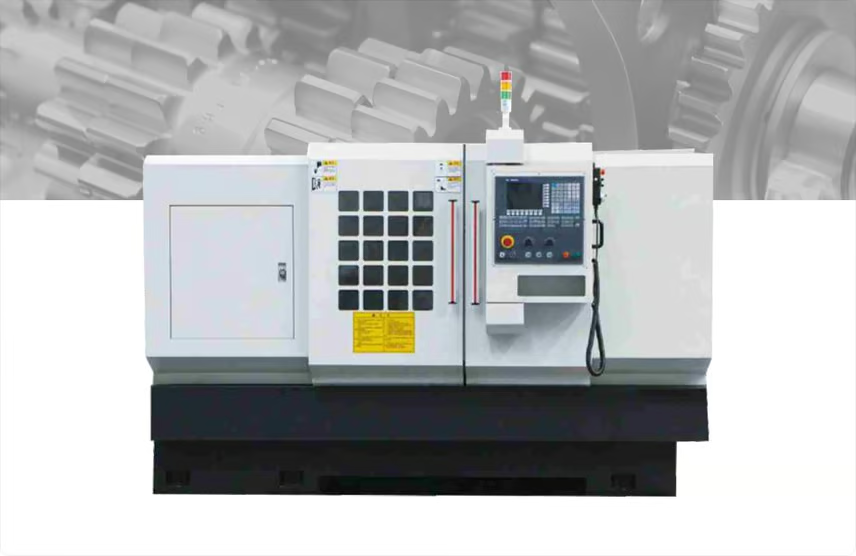
Turret Lathe
This lathe features a turret that holds multiple tools, allowing the operator to quickly switch between them without removing and replacing tools manually. It’s commonly used in high-volume manufacturing.
Tool Room Lathe
A tool room lathe is typically used for making precise and small tools. It’s more accurate and stable than engine lathes and is often found in workshops that focus on high-quality, small batch production.
Bench Lathe
Small and compact, bench lathes are designed for light-duty work, often used for hobbyists and small workshops. They are typically used for turning small parts like gears and shafts.
Swiss-Type Lathe
A Swiss-type lathe is a high-precision machine designed for machining small, complex parts with high accuracy. It’s used for parts that require intricate features, commonly found in medical and aerospace industries.
Each of these lathe types serves different production needs and selecting the right one depends on the scope of the project, material type and the precision required.
What Materials can be Machined Using a Lathe Machine?
Lathe machines are versatile tools that can handle a wide range of materials. Here are the most common materials that can be machined:
- Metals: Lathe machines are frequently used for machining metals like steel, aluminum, brass and copper. These materials are ideal for turning, drilling and threading.
- Wood: Lathes specifically designed for woodworking are used to turn wood pieces into various shapes, such as furniture legs, bowls and spindles.
- Plastics: Lathes can also machine plastics like acrylic, PVC and polycarbonate, which are commonly used in prototyping and lightweight parts.
- Composites: Advanced lathes can machine composite materials like carbon fiber and fiberglass used in industries such as aerospace and automotive.
The material you choose to machine on a lathe depends on the application, with each material requiring specific settings and cutting tools.
How Do You Choose the Right Lathe Machine for Your Needs?
Selecting the right lathe machine for your project depends on several factors. Here’s what to consider when choosing a lathe:
Type of Work
Determine the type of work you will be performing. If you need high-volume production, a CNC lathe may be the best choice. For small-scale or one-off projects, a manual engine lathe might suffice.
Material
Consider the material you will be machining. Some lathes are designed to work with specific materials, such as metals or wood, while others can handle a variety of materials.
Size of Workpieces
Evaluate the size of the workpieces you will be machining. Larger workpieces will require a lathe with a larger swing capacity and extended bed length.
What Our Customers Say
“Good service. Providing full and real information before delivering the product.I purchased lathe machine and many more products from Bhavya.From Gujrat to Kashmir long distance, with proper packaging received lathe machine 100% in good condition.Worked on machine,The accuracy is too good. Thanks Team Bhavya”
Nasir Hayat On Google
Precision Requirements
If you need extreme precision, such as in aerospace or medical applications, opt for a CNC lathe, which offers superior accuracy and repeatability.
Budget
Lathe machines come in a range of prices. CNC lathes tend to be more expensive than manual lathes due to their automated features. Consider your budget and production requirements when making a choice.
Power and Speed
Different lathes offer varying speeds and power. High-speed lathes are ideal for soft materials, while slower speeds work better for hard metals.
In short, choosing the right lathe requires assessing the specific needs of your project, including the type of material, the complexity of the task and the precision required.
What are the Key Features of a CNC Lathe Machine?
CNC (Computer Numerical Control) lathes are an advanced version of traditional lathes, incorporating computer control for automated, precise machining. Here are the key features of a CNC lathe machine:
Automated Control
CNC lathes are controlled by pre-programmed software, meaning they can automatically execute complex machining tasks with high accuracy and repeatability. Operators input the design into the computer and the machine does the rest.
Multi-Axis Capabilities
Modern CNC lathes have multi-axis capabilities, allowing them to perform intricate cuts and shapes on a workpiece without needing to be repositioned. Most CNC lathes operate on 3, 4, or even 5 axes.
Increased Efficiency
CNC lathes can run continuously, reducing the need for constant supervision. They offer high-speed production with minimal human intervention, making them ideal for mass production.
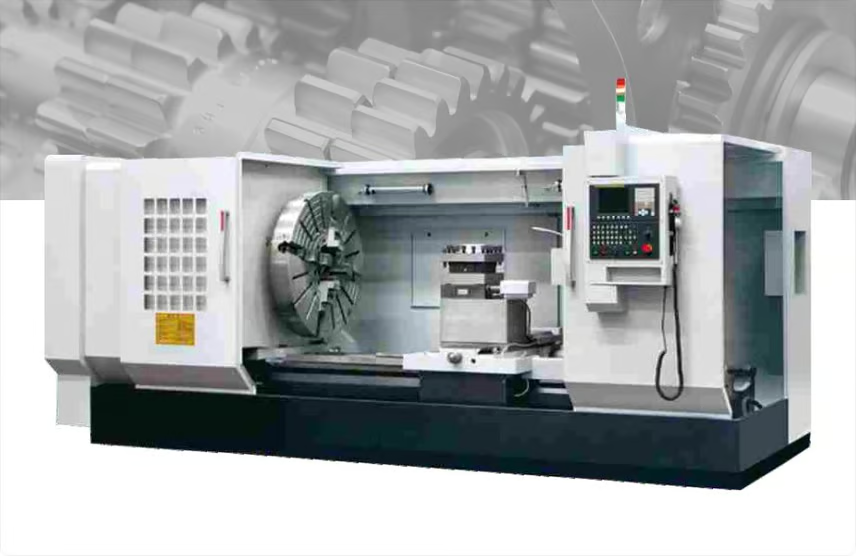
High Precision
CNC lathes deliver exceptional accuracy. This makes them invaluable for creating high-tolerance components used in industries such as aerospace, automotive and medical.
Flexible Programming
CNC lathes allow for easy reprogramming, making them suitable for custom orders, prototyping and quick adjustments. Programs can be saved and reused for consistent results in future production runs.
Integrated Safety Features
Many CNC lathes come equipped with safety features such as automatic shutoffs, sensors and guarding systems to protect operators.
CNC lathes have revolutionized the manufacturing industry by offering greater precision, automation and efficiency, making them ideal for modern production environments.
What are the Common Lathe Machine Parts and Its Functions?
A lathe machine consists of several essential components that work together to perform various operations. Here are the most common lathe machine parts and their functions:
Bed
The bed is the foundation of the lathe, providing a rigid support for all other components. It ensures the stability of the machine during operation.
Headstock
The headstock contains the spindle, which holds and rotates the workpiece. It also houses the gears and motor that control the rotation speed of the spindle.
Tailstock
The tailstock supports the other end of the workpiece, ensuring it remains steady during machining. It can also hold tools like drills for certain operations.

Carriage
The carriage moves the cutting tool along the bed. It can be adjusted to control the tool’s position in relation to the workpiece.
Cross Slide
The cross slide is part of the carriage and moves the tool in and out, allowing for precise adjustments in depth during the cutting process.
Tool Post
The tool post holds the cutting tools and allows them to be easily adjusted. It can accommodate multiple tools, especially on turret lathes.
Chuck
The chuck is a clamp that holds the workpiece in place. It can be a three-jaw or four-jaw chuck depending on the type of workpiece and its symmetry.
Lead Screw
The lead screw is used for moving the carriage in a linear direction for threading operations.
These parts work together to allow the lathe machine to function smoothly, offering precise machining capabilities for various applications.
How Can I Maintain My Lathe Machine for Optimal Performance?
Proper maintenance of a lathe machine is crucial to ensure its longevity and optimal performance. A well-maintained lathe not only operates smoothly but also helps prevent costly repairs. Here are some key steps to maintain your lathe machine:
Regular Cleaning
Dirt, dust and metal shavings can accumulate on the lathe, affecting its operation. Regularly clean the machine, especially the bed, carriage and spindle, using a soft brush or cloth. For stubborn dirt, use compressed air to remove debris from hard-to-reach areas.

Lubrication
Regular lubrication is essential for smooth operation and to prevent wear on moving parts. Check the oil level in the machine and replace it as needed. Ensure that all moving parts, including gears, lead screws and bearings, are adequately lubricated to reduce friction.
Inspecting the Parts
Frequent inspections of key components like the spindle, chuck and tailstock are essential. Look for any signs of damage or wear, such as rust, cracks, or loose parts. Early detection can help prevent major breakdowns.
Tightening Loose Components
Over time, parts like bolts, nuts and clamps may loosen due to vibrations and repeated use. Regularly tighten these components to prevent accidents and ensure the machine remains stable during operation.
Checking Alignment
Ensure the machine is properly aligned to avoid inaccuracies during machining. Misalignment can lead to defects in the workpieces and cause unnecessary strain on the lathe. Use a dial indicator to check the alignment of the machine’s components periodically.
Tool Maintenance
The cutting tools need to be inspected and maintained as well. Over time, tools can become dull or damaged, affecting the quality of the workpiece. Sharpen or replace tools as necessary.
By following these maintenance practices, you can ensure that your lathe machine operates efficiently and has a long lifespan.
What Safety Precautions Should be Taken While Using a Lathe Machine?
Safety is paramount when operating a lathe machine, as the tool involves rotating parts and sharp cutting tools that can pose serious hazards. Here are some essential safety precautions to take while using a lathe:
Wear Appropriate Personal Protective Equipment (PPE)
Always wear the necessary PPE, such as safety glasses, ear protection and gloves, to protect yourself from flying debris, noise and sharp edges. Avoid loose clothing or jewelry that could get caught in the machine.
Keep the Work Area Clean
A cluttered work area can lead to accidents. Keep the lathe and the surrounding area clean and free from any obstacles. Ensure that all tools and materials are properly stored.
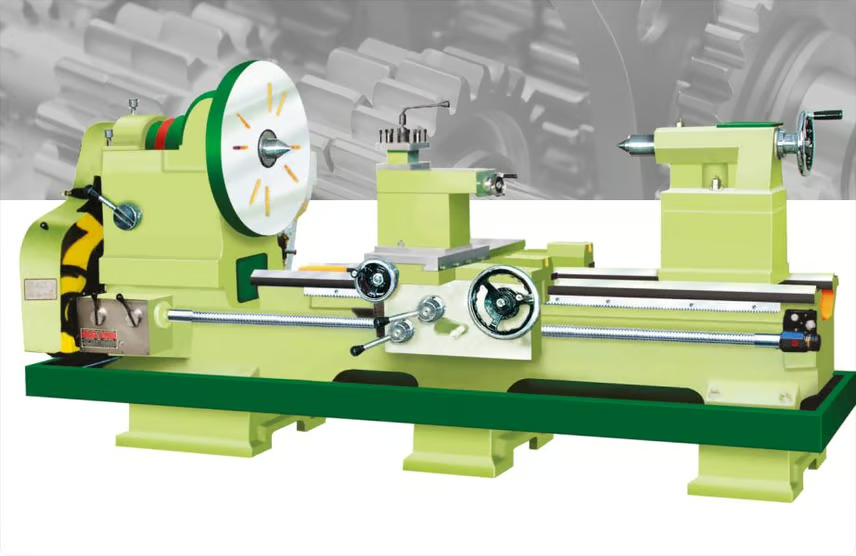
Secure the Workpiece
Ensure that the workpiece is securely fastened to the chuck before beginning any machining operation. A loose workpiece can fly out of the machine, causing serious injury.
Never Reach Near Moving Parts
Never reach into the lathe while it is running. Always wait for the machine to stop before adjusting, cleaning, or removing parts. Be aware of the moving parts and keep your hands and other body parts away from them.
Follow Proper Setup Procedures
Before starting the machine, double-check the setup. Ensure the tool is securely mounted, the workpiece is aligned correctly and the lathe settings (speed, feed, etc.) are appropriate for the job at hand.
Understand the Machine’s Operation
Before operating a lathe, make sure you understand its features, controls and capabilities. Familiarize yourself with the specific model you’re using, as different lathes may have different safety features and settings.
By adhering to these safety precautions, you can minimize risks and ensure a safe working environment when using a lathe machine.
What are the Advantages of Using a Lathe Machine Over Other Machines?
Lathe machines offer numerous advantages over other machines in terms of versatility, precision and efficiency. Here are some of the key benefits:
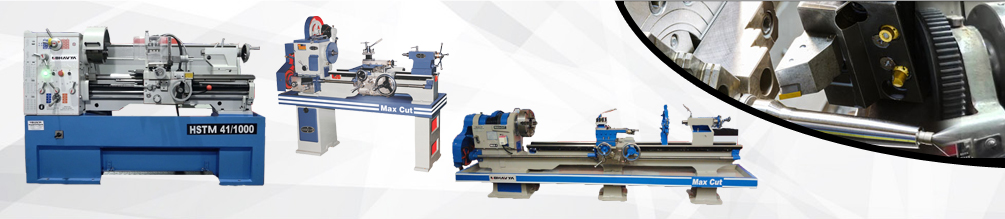
Versatility
Lathe machines can be used to machine a wide range of materials, from metals to plastics to wood. This versatility makes them essential tools in many industries.
Precision
Lathe machines are designed to produce highly accurate and precise workpieces. The ability to make fine adjustments allows for exceptional accuracy in turning, drilling and threading operations.
Complex Shaping
Unlike other machines that are limited to simple shapes, lathe machines can produce complex, symmetrical shapes like cones, spheres and cylinders. This capability is particularly important for industries that require intricate parts.
High-Speed Operation
Modern CNC lathes are capable of running at high speeds, which helps increase production rates. The automation of the process minimizes human error and improves overall efficiency.
Reduced Material Waste
Lathes offer precise material removal, which reduces waste compared to some other machining processes. This efficiency can help save on raw material costs.
Adaptability
Lathe machines can be used for both small-scale, custom jobs as well as large-volume manufacturing. Whether you’re creating a single part or a thousand, a lathe can handle both scenarios effectively.
Overall, the lathe machine is a versatile and reliable tool that provides significant advantages in both performance and cost-efficiency, making it a key player in many industries.
How Does a CNC Lathe Machine Differ from a Manual Lathe Machine?
CNC (Computer Numerical Control) lathes and manual lathes are both used for machining, but they differ significantly in terms of operation, precision and automation. Here’s how they compare:
Automation
CNC lathes are fully automated, relying on a computer program to control the tool movement, speed and other parameters. Manual lathes, on the other hand, require the operator to control every aspect of the machine, including tool position and speed.
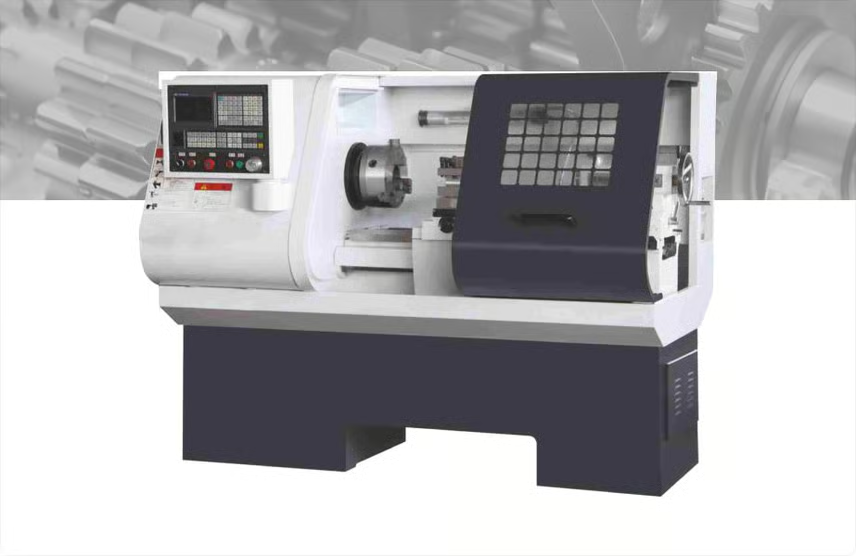
Precision
CNC lathes offer higher precision due to their ability to execute repetitive tasks with exact measurements. This is particularly beneficial for mass production and complex designs. Manual lathes may have more variability in precision, depending on the operator’s skill and experience.
Complexity
CNC lathes can perform complex operations that would be difficult or impossible with manual lathes. With multi-axis capabilities, CNC lathes can handle intricate geometries and precise cuts. Manual lathes are better suited for simple tasks or one-off projects that don’t require advanced features.
Speed
CNC lathes are faster because they can operate without human intervention once programmed. Manual lathes, however, depend on the operator’s speed, which can slow down the overall process.
Cost
Manual lathes are generally less expensive than CNC lathes, making them a more affordable option for smaller workshops or hobbyists. CNC lathes, while more expensive, offer significant productivity and precision benefits, making them ideal for larger manufacturing operations.
In summary, the primary difference lies in automation and precision. CNC lathes are ideal for mass production, complex machining and high precision, while manual lathes are more suited for simpler tasks, small-scale production and customized work.
How Can I Troubleshoot Common Lathe Machine Problems?
Lathe machines, like any other equipment, can encounter problems during operation. Here are some common issues and troubleshooting tips:
Machine Vibration
Vibration can affect the precision of the machine. Ensure that the lathe is properly aligned, the workpiece is securely fastened and that the cutting tools are sharp.
Poor Surface Finish
If the workpiece has a rough finish, check the tool condition, spindle speed and feed rate. A dull tool or incorrect settings can cause poor surface quality.
Unusual Noise
Unusual noises can indicate a mechanical issue, such as a loose part or a problem with the motor. Check for loose bolts, worn-out bearings, or damaged components.
Inaccurate Machining
Inaccurate machining can be due to misalignment or worn-out parts. Check the alignment of the machine, replace worn parts and recalibrate the tool settings.
Electrical Issues
If the lathe isn’t powering on, check the electrical connections, circuit breakers and fuses. Electrical problems may require professional inspection and repair.
Regular inspections and maintenance can help minimize these issues and keep your lathe in good working condition.
What are the Essential Tools and Accessories Needed for a Lathe Machine?
To get the most out of your lathe machine, you’ll need several essential tools and accessories:
- Cutting Tools: Various types of cutting tools are needed, such as turning tools, boring tools and threading tools.
- Chucks: These secure the workpiece in place during machining. Common types are three-jaw and four-jaw chucks.
- Tool Holders: Tool holders are used to secure cutting tools on the carriage and ensure accurate machining.
- Live Centers: These are used to support the workpiece from the tailstock end.
- Faceplates: These are used to hold irregularly shaped workpieces.
- Collet Chucks: Used for holding small parts with high precision.
These accessories are vital for achieving accurate and efficient machining results.
Conclusion
Lathe machines are essential tools in modern manufacturing, offering precision, versatility and efficiency across various industries. Whether used for simple tasks with manual lathes or complex operations with CNC lathes, these machines provide high-quality results and improve overall production. Understanding their types, components and functions helps ensure the right machine choice for your needs, ultimately enhancing productivity.
Proper maintenance, safety precautions and troubleshooting techniques are key to maximizing the lifespan and performance of your lathe machine. By following best practices, you can ensure smooth, safe and effective operations, contributing to the success of your projects and the longevity of your equipment.