A CNC Press Brake machine is a great option for a company that produces large quantities of finished products. The main considerations for selecting a CNC Press Brake are the complexity of the designs to be created, how many axes will be needed, and the workspace size. Here are some tips for making the best choice.
CNC Press Brakes Precision
Your Precision CNC Press Brake will not do the job properly if its tooling is not in good condition. The tools are the only machine parts that touch the finished product, so it is essential to invest in good press brake tools. A poor press brake tooling can render a high-quality machine useless.
The accuracy of tooling will directly affect the accuracy of the bent work piece. The upper and lower dies must match in terms of angle and edge. The die compensation device also plays a major role in the accuracy of the work. A numerically controlled compensation device is able to compensate for a wide range of plate positions, whereas a manually adjusted compensation device will require artificial compensation.
Different materials require different bending forces. For example, thick materials need higher bending force, and this will require a higher press brake load limit. The standard press brakes have capacities of 400, 300, 160, and 80 tons. However, if you need to bend sheets with a different thickness, you can use an Adjustable Die System.
A Precision CNC Press Brake also features a deflection compensation system that automatically adjusts the angle between the top and bottom ram. This device also compensates for deformation in the upper ram. This feature improves the accuracy of a precision CNC Press Brake and also lowers labor intensity.
Speed of CNC Press Brakes
CNC press brakes are capable of bending materials with greater precision. These press brakes can be easily operated and feature a user-friendly control unit. They also offer a rigid body frame and high efficiency. Moreover, they are CE-certified and come with a suitable price range. If you have sufficient funds to invest in a CNC press brake, it’s an ideal choice.
CNC press brakes have a smooth speed conversion and can achieve up to 200mm/s. Their synchronization can be adjusted through a proportional electro-hydraulic valve group. They also have grating rulers that allow users to see errors in real-time. In addition to high bending accuracy, CNC press brakes have fast down and return speeds, averaging at 13 or 15 mm/s.
High-speed CNC press brakes are available for the North American and European markets. The frame of these machines is welded steel and has a single oil cylinder. The working table, oil box, slider, and CNC control system are all integrated into the compact frame of this machine. The die is also included in the compact CNC press brake.
CNC press brake machines are highly versatile and can be customized to meet the needs of your specific business. When buying a CNC press brake, consider the number of axes it has, the complexity of the designs, and the size of the workspace.
Springback in CNC Press Brake
The amount of springback in a CNC press brake is dependent on several factors. These include the material tensile strength, tooling type, and bending speed. This makes accurate springback prediction extremely important, especially when working with materials with deep bends and thick, high-strength material.
The angle difference between the tooling and workpiece during the bend process is used to calculate springback. The angle is then divided by the tooling angle to get the total springback. The springback will vary depending on the material and the bend radius. Calculating the initial angle is simple. Double the final angle to determine the desired result.
Conventional press brakes bend sheet metal to a predetermined angle, then spring back the material to a lesser bend than the desired angle. The operator chooses the terminal punch position manually and then reverses the ram’s movement at a predetermined point. This results in the piece being bent to a loaded angle th1, after which it returns to a relaxed position. The process repeats itself until the workpiece is fully unloaded.
The final angle and radius are calculated by using a springback calculator. Although these calculators are not 100% accurate, they help determine the right press brake tools for your needs. Generally, the amount of springback increases with the IR/MT ratio, so the higher the IR/MT ratio, the greater the springback. For example, 1.8 degrees of springback corresponds to a final radius of.510mm, or about 0.2% larger than the punch radius.
Cost of CNC Press Brake
When you are choosing a CNC press brake for your manufacturing business, you have many factors to consider. First, you will need to determine the thickness of the material to be bent. You will need a large bending force for thicker materials. In general, a press brake should be able to handle up to 200mm of thickness. Besides, you should consider the quality of the CNC machine, its accuracy, and the controls.
Other costs that you will want to consider are the operator salary, the hydraulic fluid, and the tooling. The machine will also cost you electrical costs. In addition, you will have to account for the downtime you will experience when performing routine maintenance. These costs can be a major factor in deciding between two machines.
Purchasing a new CNC press brake will cost you a lot of money. Depending on the size of the press brake, you can spend anywhere from $50,000 to $120,000 for it. Of course, there is another option – reconditioning an old press brake. This option is cheaper than purchasing a new machine, but it will cost more than buying a used one.
CNC press brakes can have advanced features that help make manufacturing easier. Many have multi-axis capabilities that can assist you in your manufacturing needs. They can also be equipped with a CNC backgauge for faster bending.
Installation of CNC Press Brake
A CNC Press Brake is an automated metal-bending machine that produces precision parts. Its automated process eliminates manual work by identifying the correct tooling for each job. The software also determines the proper tooling layout on the machine. This reduces the risk of human error and ensures accuracy and consistency.
Before starting the calibration process, the press brake should be thoroughly cleaned. It has likely traveled long distances and may have been covered in Cosmoline by the factory. It should be checked by staff for loose or broken parts. Then, it can be calibrated. Once cleaned, the machine can be used.
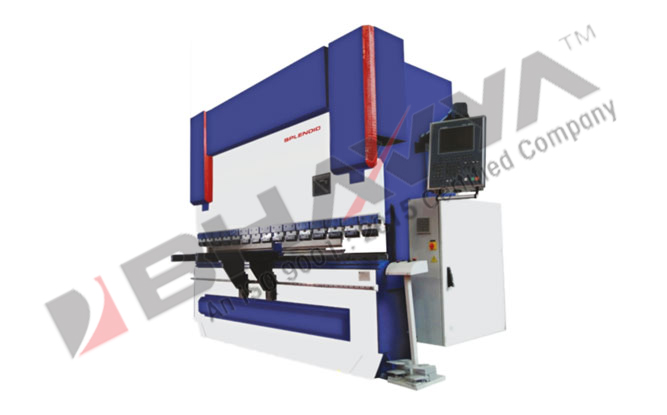
Programming the CNC press brake is a complex process, especially for beginners. It involves setting up the machine, programming the CNC system, and adjusting its parameters. Typically, the ESA CNC controller allows multiple work steps to be programmed. Using the “editor” page of the software, you can input the material, width, thickness, punch, die, and more.
A CNC press brake machine is a useful tool for the manufacturing industry. Whether you need to make complex parts for a mass production, CNC press brakes can provide the accuracy and precision you need to meet production needs. CNC press brake machines are versatile and can be customized to meet your needs.
CNC Press Brakes Maintenance
In order to get maximum efficiency from your CNC press brake, you must regularly perform a series of preventive maintenance procedures. These measures include lubrication and checking the function of the control equipment. For example, you should inspect the longitudinal rulers, electric valves, sensors, and pneumatic valves. In addition, you should check the condition of the matrix mandrels. If they show signs of wear, you must return them to the manufacturer.
The hydraulic oil pipe should be properly tightened. The hydraulic oil circuit should have a good level of hydraulic oil. It is also important to replace the seals in time. If the seals are not properly installed, the press brake may not be able to work correctly. The hydraulic oil should also be filled to the maximum capacity.
It is also important to regularly check electrical connections and switches on your press brake. When performing these maintenance checks, you should always do it with the system turned off. However, there are some maintenance tasks that should be performed with the press brake still under power. When you are working on your CNC press brake, always take precautions. Make sure you do the work in a hygienic environment.
After the press brake is installed, you must conduct a periodic inspection of the hydraulic system. This includes cleaning the hydraulic oil filter and changing the hydraulic oil every three months. Checking the hydraulic oil level is essential to prevent erratic operation of the ram. If the level of the hydraulic oil is low, you will endanger the hydraulic pump and reduce its lifespan.