Monthly Archives: May 2013
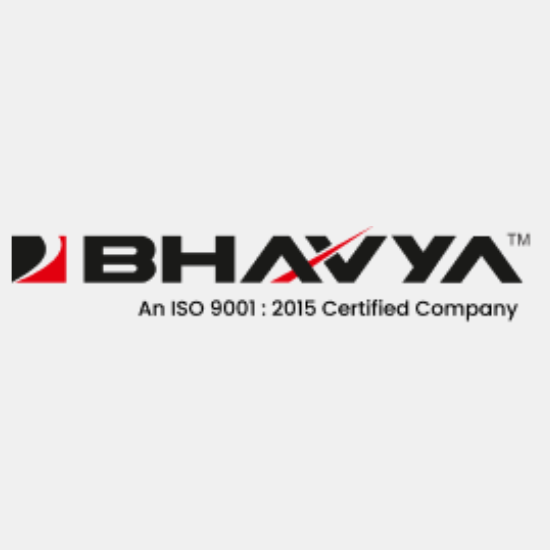
Evaluation History of Power Press for Its Significant Placement in Present Machine Tool Industry
The power press is an important machine tool which is used to change the shape of a workpiece. In the ancient times metal was shaped manually using a hand hammer. Later on big hammers were used to press large quantities…
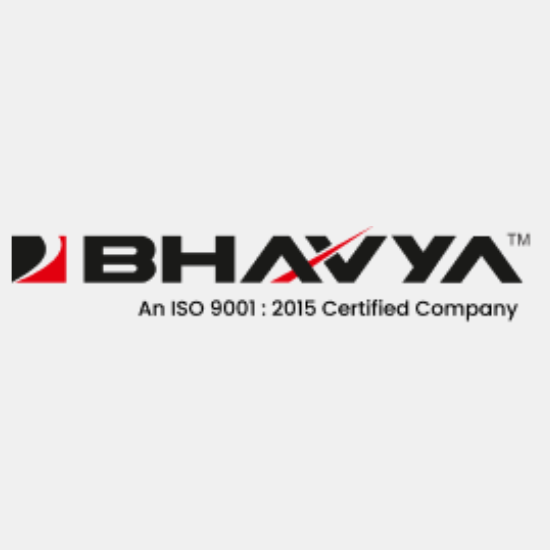
Pros & Cons While Selecting Indian Lathes & Imported Lathe Machines
The lathe machine is the most common tool in a workshop. It is mainly used for producing objects that have symmetry about their axis of rotation; as well as for precisely machining comparatively hard materials. Earlier lathes were simple and…
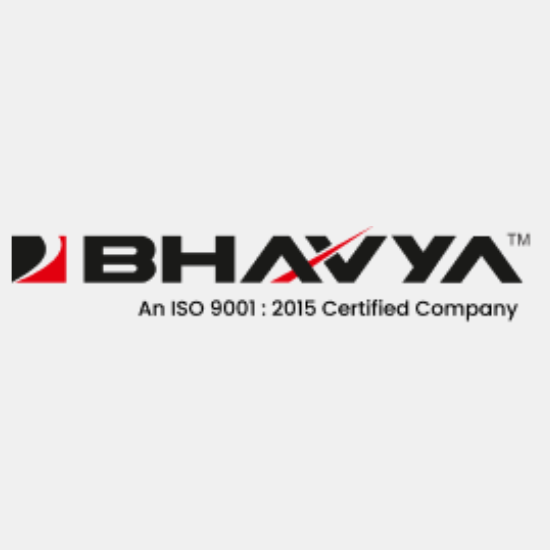
How to Choose Right Bandsaw Machine for Woodworking & Metal Shaping
The bandsaw is one of the most important equipment in any workshop. It is also regarded as an ideal tool for accurately cutting different types of materials that includes wood, metal, plastic, etc. In fact, besides cutting curves a bandsaw can…
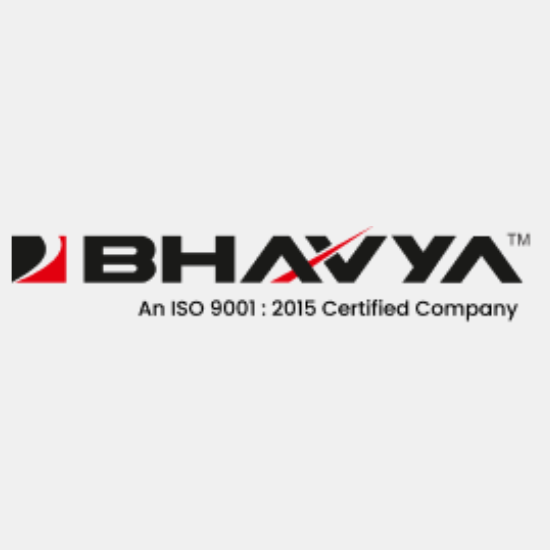
Benefits of Buying Machine Tools from Indian Manufacturers
The machine tool industry is regarded as the backbone of any industrial economy. It is basically the source through which a broad variety of industrial products and consumer goods are manufactured. India is a developing nation with a rising economy,…
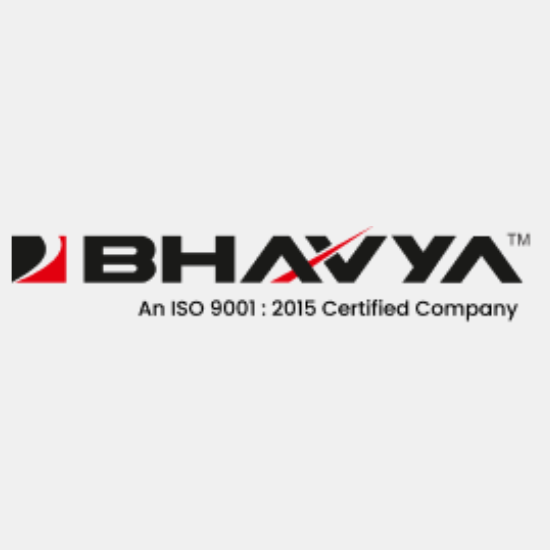
Useful Buying Tips for Drill Machine & Radial Drill Machine
A drill machine is primarily utilized to drill a variety of wooden and metal items. It is also commonly applied in construction work, drilling foundations, breaking boulders, quarry work, etc. These are easy to operate and highly reliable. They can…
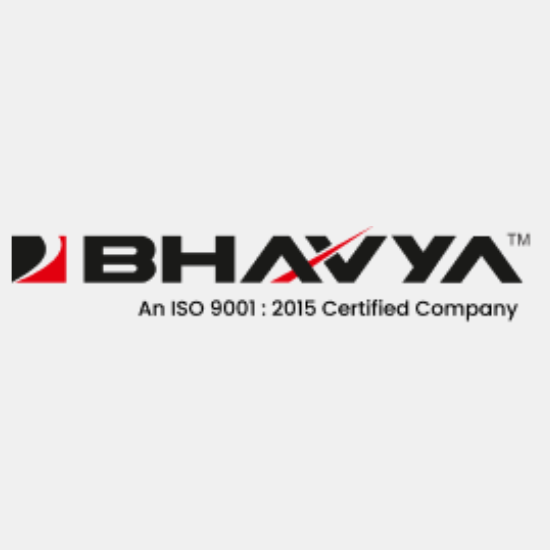
5 Most Important Machine Tools For Any Workshop [INFOGRAPH]
Nowadays, several types of workshop machine tools are manufactured in many countries around the globe. These tools are commonly used for different purposes in a wide range of industrial segments such as woodworking, automobile, electrical, construction, etc. This infograph give…
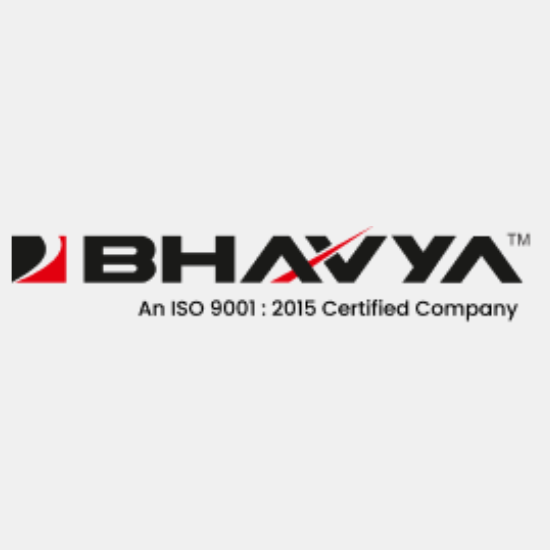
Set Up Procedure for Mechanical and Hydraulic Press Brake
Introduction - Press Brake It is a kind of bending machine used for bending sheet metal into a predetermined shape. The bending depends upon the shape of the punch and the die. These are being widely used in metallurgy, aircraft…
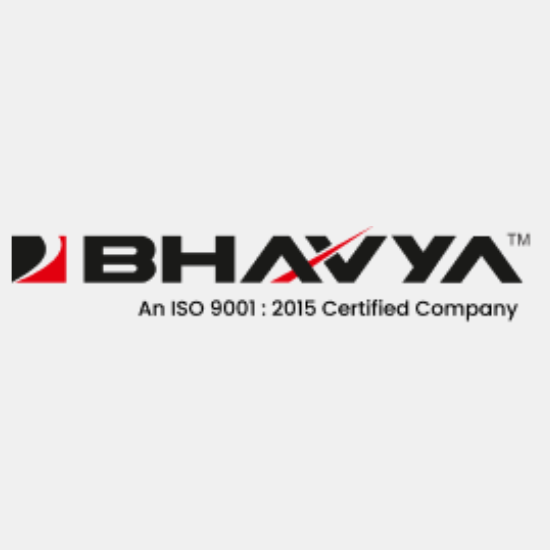
How does a Hydraulic Press Brake work to give a Customized Sheet Metal Bending Operation?
It is important equipment for the industries having jobs related to the metal shaping or bending. Two types are popular among metal fabricators – the manually operated press brakes and the press brakes which operate on the hydraulic power. The…
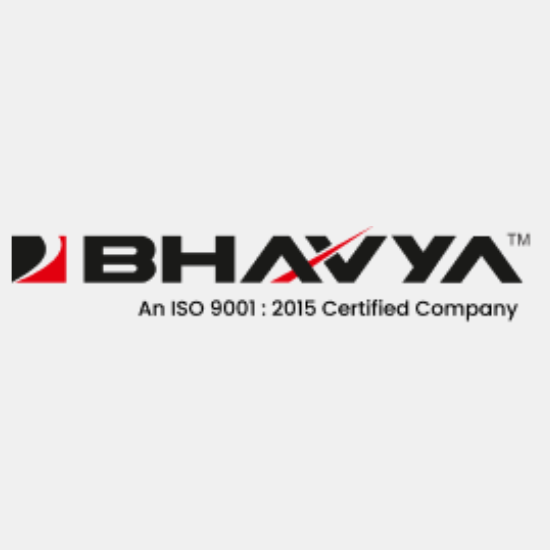
Make Work Easier with one of Technology’s Latest Drill Machines!
Drill machines have come a long way in history because of the value they add in numerous areas such as: infrastructure, mining and many fields that involve building, demolishing or exploring. There are various types of drills available in the market…